Exploring Welding Technician Jobs: A Comprehensive Overview
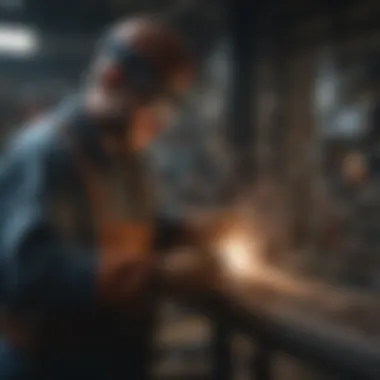
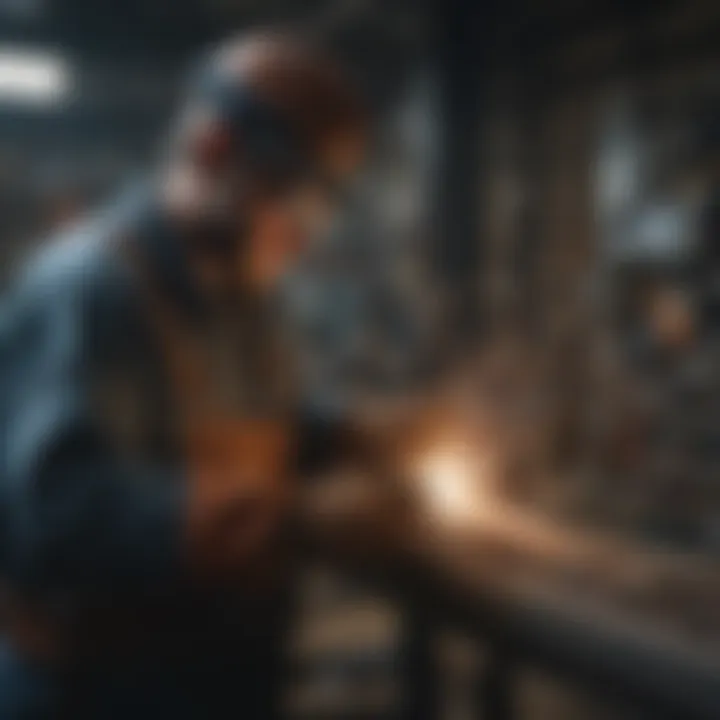
Intro
Welding technician jobs are often at the crossroads of various industries, playing a crucial role in the efficiency and safety of numerous projects. The profession demands not only a solid understanding of welding techniques but also a grasp of practical applications and the evolving technology that defines the modern welding landscape. This article aims to provide a comprehensive overview of welding technician jobs, offering valuable insights into the skills required for success, potential career paths, and relevant industry trends that are shaping the future of this essential trade.
Key Concepts and Terminology
Definition of Terms
To effectively communicate about welding technician jobs, it is essential to understand some key terms:
- Welding: The process of joining materials, typically metals or thermoplastics, through the application of heat.
- Welder: A skilled professional who performs welding tasks across various industries.
- Welding Technician: A professional who not only welds but also inspects, tests, and ensures that welding tasks meet required specifications.
Overview of Relevant Practices
Welding practices encompass various styles and methods, each with unique applications. The most common types include:
- Arc Welding: A widely used technique involving an electric arc to create heat for melting and joining materials.
- MIG Welding: Metal Inert Gas welding, popular for its ease of use and speed.
- TIG Welding: Tungsten Inert Gas welding, known for producing high-quality welds in thin materials.
Understanding these concepts is vital for grasping the broader implications of welding within varied sectors such as construction, manufacturing, and aerospace.
Current Trends and Innovations
Latest Research and Developments
The welding industry is experiencing notable advancements. New materials and methodologies are constantly emerging, driven by the demand for improved efficiency and sustainability. For example, research on advanced alloys and composites is influencing the types of materials that welding technicians are now expected to work with.
Emerging Technologies and Tools
The landscape of welding technology is shifting. Innovations such as robotic welding and automation are becoming more prevalent. Robotic systems enhance precision and reduce human error. The use of augmented reality for training and troubleshooting is also making waves in the industry, allowing welding technicians to learn and adapt in real-time.
Practical Applications
Step-by-Step Guides
For aspiring welding technicians, the following steps can serve as a guide to getting started in the profession:
- Gain Basic Knowledge: Understanding the types of welding processes and tools is fundamental.
- Hands-On Training: Enroll in a vocational program or apprenticeship to obtain practical experience.
- Obtain Certifications: Certifications from recognized institutions can boost employment prospects and validate skills.
Troubleshooting Common Issues
Welding technicians often encounter issues that require immediate attention. Common problems include:
- Inadequate penetration in welds, which may lead to structural weaknesses.
- Porosity, resulting from trapped air in the weld, potentially compromising integrity.
Identifying these issues promptly is crucial to maintaining safety and quality in projects.
โThe role of a welding technician is evolving, with skills in technology becoming increasingly important.โ
This overview serves to lay the groundwork for a deeper discussion on welding technician jobs, including salary expectations, certifications, and future job market trends. By understanding the complexities and requirements of this profession, professionals and enthusiasts can better navigate their career paths within the welding field.
Understanding the Role of a Welding Technician
The role of a welding technician is crucial in various industries, including construction, manufacturing, and aerospace. These professionals are responsible for joining materials together using different welding techniques and equipment. Understanding this role helps in appreciating the processes involved and the skills required to excel in the field. The significance of welding technicians lies not only in their technical abilities but also in their contributions to the integrity and safety of structures and products.
Welding technicians must possess a blend of knowledge, skills, and hands-on experience. This complexity requires a thorough exploration of the responsibilities and environments where these technicians operate. It enables aspiring welders and employers alike to gauge the expectations and importance of this profession.
Defining Welding Technician Responsibilities
Welding technicians have defined responsibilities that encompass a range of tasks.
Some primary responsibilities include:
- Interpreting blueprints and technical drawings: Understanding these documents is critical for accurately executing welding tasks.
- Selecting appropriate welding methods: Different materials and project requirements dictate which welding technique to use, whether it be MIG, TIG, or another method.
- Setting up welding equipment: Ensuring that the tools and machines are prepared correctly influences the quality of the weld.
- Performing inspections: Regularly checking the quality of welds and identifying any defects is an integral part of the job.
- Maintaining safety standards: Adhering to protocols is essential to prevent accidents and injuries.
Each responsibility requires careful attention to detail and a commitment to high standards, reflecting the technical and safety importance of this role in welding.
Working Environments for Welding Technicians
Welding technicians work in diverse environments that affect their day-to-day activities. Depending on the field, these environments can vary significantly:
- Manufacturing plants typically have large infrastructures with specialized equipment dedicated to mass production. It often involves repetitive tasks, focusing on efficiency and precision.
- Construction sites demand adaptability, as technicians may work outdoors and face changing environmental conditions. Here, they must often collaborate with other construction professionals.
- Shipyards present unique challenges with metal structures often requiring specialized welding techniques tailored to marine applications.
- Automotive facilities focus on producing high-quality welds that meet strict industry standards. Technicians work with automated systems and newer technologies.
In each setting, welding technicians encounter specific challenges and opportunities for growth, enhancing their skills and career prospects in the welding industry.
Skills Required for Welding Technicians
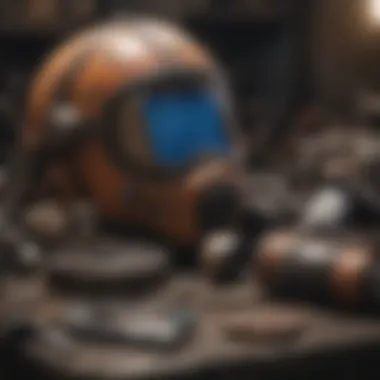
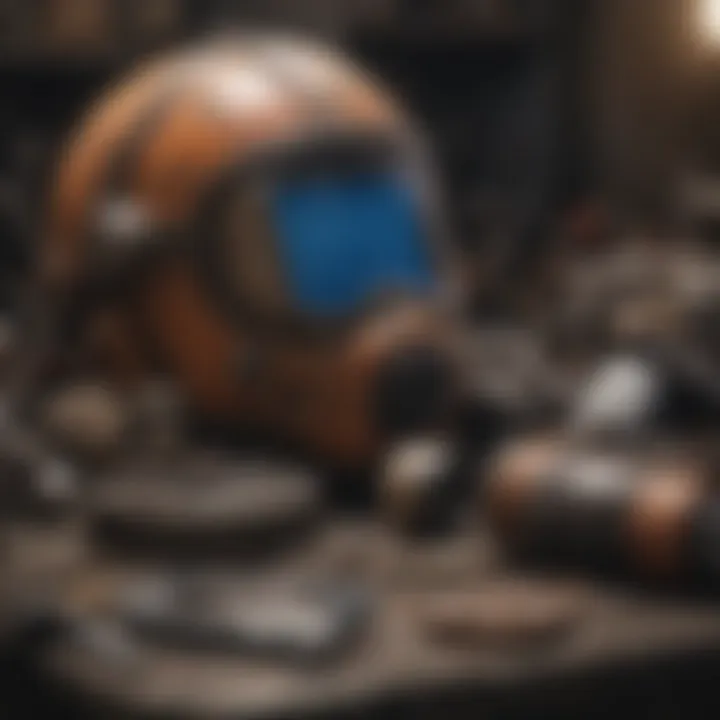
The role of a welding technician demands a wide variety of skills that go beyond just knowledge of welding techniques. This section illustrates the necessary technical and soft skills that enhance a welder's capability and adaptability in various job environments. These skills not only help in achieving quality work but also support in ensuring safety and efficiency at the workplace.
Technical Skills: Tools and Techniques
Technical skills form the backbone of a welding technician's capabilities. These include proficiency in using various welding tools and techniques. Familiarity with equipment such as MIG welders, TIG welders, and stick welding machines is crucial. Each type of welding technique serves distinct purposes and understanding their applications is essential. For instance, MIG welding is popular for its speed and ease of use, making it suitable for fabricating materials in construction and manufacturing.
Moreover, knowledge of different materials is vital. A welding technician must be adept in welding metals like steel, aluminum, and stainless steel, as the properties of these materials affect the welding approach.
Understanding safety protocols while handling these tools is equally important. For example:
- Proper setup for electrical connections
- Safe handling of gas cylinders and flammable materials
- Awareness of ventilation requirements to prevent harmful fumes
These factors contribute to a safer working environment. Continued training in new welding technologies also enhances a technician's adaptability in an evolving job market. As regulations and technologies develop, keeping skills current is crucial for long-term career success.
Soft Skills for Successful Welders
While technical expertise is foundational, soft skills are equally significant in welding technician roles. These skills facilitate effective communication and teamwork in often high-pressure environments. A welder frequently collaborates with engineers, designers, and other tradespeople, which necessitates clear communication. For effective teamwork, a welder musnโt just understand their work but also comprehend how it fits into the larger project.
Problem-solving skills are vital. In the field, situations may arise requiring quick thinking, such as repairing a weld or adjusting a technique mid-project. Adaptability and resilience help technicians face challenges without compromising quality.
Additionally, attention to detail cannot be overlooked. Precision is paramount in welding. A minor error can lead to substantial issues down the line, affecting the structural integrity of the finished product.
Effective time management also plays a role in meeting project deadlines. A skilled welding technician should balance quality with efficiency to stay on schedule.
"The combination of technical skills and soft skills creates a well-rounded professional who can thrive in the welding industry."
In summary, both technical and soft skills are critical to the success of welding technicians. Mastering these abilities not only elevates one's work standards but also enhances opportunities for career advancement.
Education and Training Paths
In the field of welding, education and training paths are crucial for aspiring technicians. Understanding these paths allows candidates to make informed choices about how to enter and succeed in the welding profession. This section will discuss formal education options as well as apprenticeships and on-the-job training.
Formal Education Options
Formal education for welding technicians often involves programs at trade schools or community colleges. Many institutions offer specialized courses in welding technology. These programs typically cover foundational knowledge in metallurgy, welding processes, and safety protocols.
Benefits of formal education include:
- Structured learning curriculum that ensures comprehensive coverage of essential topics.
- Access to experienced instructors who provide guidance and insights into the industry.
- Opportunities for networking within the welding community, which can lead to job placements.
- Hands-on training in well-equipped labs, simulating real-world experiences.
Courses often lead to certifications or diplomas. Students become familiar with various welding techniques, such as MIG, TIG, and stick welding. Graduates can demonstrate a strong grasp of both theory and practical skills, making them more attractive to employers.
Apprenticeships and On-the-Job Training
Apprenticeships offer another viable path for becoming a welding technician. This method combines classroom instruction with hands-on experience. Apprentices work under the supervision of seasoned professionals, enabling them to learn practical skills required for the job.
The benefits of apprenticeships include:
- Learning in a real work environment, which enhances the understanding of workplace dynamics.
- Earning a salary while studying can reduce financial strain during training.
- Gaining invaluable mentorship from skilled welders, which provides insight and support.
On-the-job training is often part of vocational programs and can also occur after being hired. Many employers prioritize candidates with a mix of formal training and practical experience. This combination ensures readiness to tackle various welding tasks in real situations.
"Hands-on experience is one of the best ways to learn in welding. Seeing things done in real time is invaluable, especially when it comes to complex tasks."
Overall, both formal education and apprenticeship pathways are essential for those pursuing welding technician roles. These processes not only build skills but also instill confidence in future professionals.
Certifications in Welding
Certifications in welding are fundamental for establishing credibility and showcasing expertise in the field. They serve not only as proof of a welder's skills but also as a gateway to advanced career opportunities. For professionals and enthusiasts alike, pursuing appropriate certifications is not just beneficial; it is often essential for long-term success in welding technician jobs. As industries evolve and new technologies emerge, certifications help workers stay relevant amidst changing demands.
Benefits of Certification
- Increased Employability: Employers favor certified welders. Having recognized certifications can make candidates stand out in a competitive job market.
- Higher Earning Potential: Certified welders typically command higher salaries. The investment in certification often leads to better compensation.
- Professional Development: The process of earning certification enhances oneโs knowledge and skills. This ongoing learning is crucial for career growth.
Welding certifications can differ widely by industry and specialization, leading to various programs for technicians to choose from. Understanding these different types can assist individuals in finding the right fit for their career objectives.
Types of Certification Programs
Certification programs in welding come in many forms and cover various techniques and applications.
- American Welding Society (AWS) Certifications: Recognized globally, AWS certifications validate skills in various welding processes.
- National Center for Construction Education and Research (NCCER): This organization offers a standardized curriculum that includes a range of certifications, from basic to advanced levels.
- Specific Manufacturer Certifications: Some manufacturers offer training and certifications on their products and processes. This can be vital for welders working in specialized industries, such as aerospace or automotive engineering.
Each certification has its own set of requirements, fees, and duration of validity. Prospective welders should evaluate these factors carefully.
Importance of Certification for Career Advancement
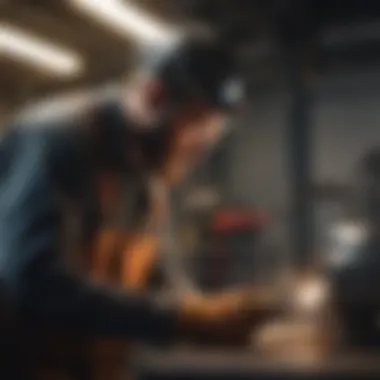
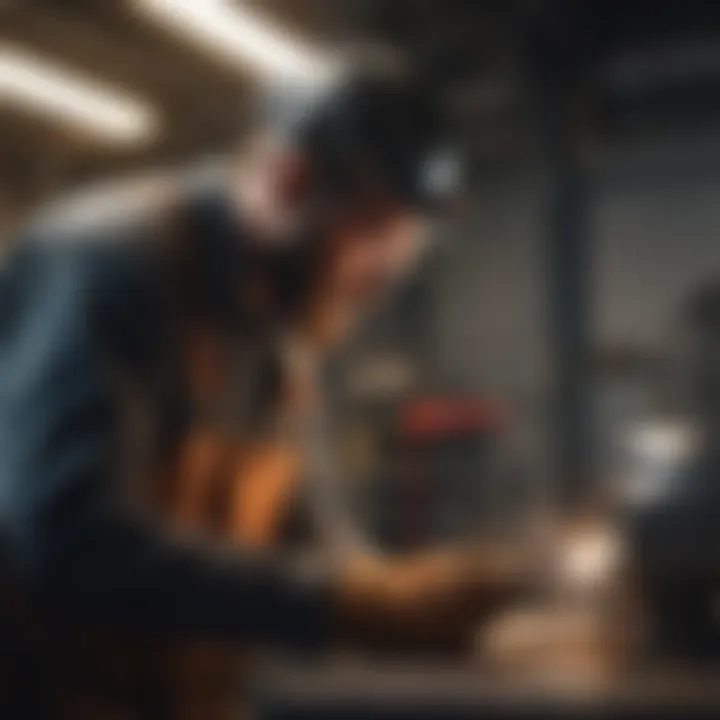
Acquiring certifications is a strategic move for welders aiming for career advancement.
- Career Differentiation: In a field with diverse skill sets, certifications help distinguish professionals from their peers. Employers often seek candidates with specific certifications for certain roles.
- Networking Opportunities: Participating in certification programs can lead to connections with industry professionals. Networking through organizations such as AWS can open doors to new job prospects and collaborations.
- Continuous Advancement: Certification typically requires ongoing education, which encourages welders to continue learning. This proactive approach helps them keep pace with advancements in welding technology.
"Certifications not only validate skills but can substantially impact career trajectories in welding. They represent commitment to the profession."
Career Paths for Welding Technicians
Exploring career paths for welding technicians is crucial. This section provides insight into entry-level positions and advanced roles, revealing the diverse opportunities available in this field. It is essential for aspiring welders and those already working to understand their options and the potential for career growth.
Entry-Level Positions
Entry-level positions in welding are an ideal way to begin a career. These roles often require a high school diploma and some vocational training. Typical entry-level jobs include:
- Welder's Helper: Assists experienced welders with tasks like preparing materials and setting up equipment. This role offers practical experience in the field while learning essential skills.
- Fabrication Technician: Engages in the assembly of various metal components by following blueprints and specifications.
- Shop Welder: Works in a factory or workshop setting, performing welds on metal parts and assemblies, often on different projects.
These roles provide foundational experience and help unfamiliarize individuals with welding processes. They also establish a basis for moving into more specialized positions or advancing training. Entry-level work often cultivates a strong understanding of safety protocols, tool usage, and teamwork, which are vital in welding.
Advanced Roles in Welding
As welders gain experience and certifications, they can move into advanced roles. These positions typically require a high level of expertise and may involve supervising others or overseeing projects. Key advanced roles include:
- Certified Welder: Obtains certifications from recognized organizations. This status assures employers of oneโs skills and knowledge.
- Welding Supervisor or Foreman: Manages welding teams, ensuring quality control and adherence to safety regulations. Their leadership skills become vital as projects become larger or more complex.
- Welding Engineer: Involves designing welding processes and methodologies. This role often suits those with a background in engineering.
Each of these roles provides significant benefits including higher salaries and greater responsibilities. Experts in the field enjoy ongoing professional development opportunities, enabling them to stay current with technological advancements in welding.
"The journey from entry-level positions to advanced roles can be both rewarding and lucrative for welding technicians."
Understanding these career paths helps individuals make informed decisions about their future in welding. Continuous learning and skill enhancement are essential for progress in this field.
Salary Expectations and Job Market Trends
Understanding salary expectations and job market trends is crucial for those considering a career in welding. It offers insights into what welders can anticipate in terms of compensation and job availability. A clear grasp of these aspects can significantly influence career decisions and strategies for professional development.
Average Salary for Welding Technicians
The average salary for welding technicians can vary widely based on several factors, including experience, geographic location, and industry specialization. As of recent data, the median annual wage for welding technicians in the United States is around $44,000. This figure can serve as a useful benchmark, though many welders earn more or less depending on their specific circumstances.
Welding technicians with several years of experience or those who have specialized in high-demand areas, like aerospace or underwater welding, can often command salaries exceeding $60,000 or even $70,000 annually. Moreover, local economic conditions play an essential role; regions with significant infrastructure projects or manufacturing facilities may offer higher wages due to increased demand for skilled professionals.
It is important to note that wages may also be affected by seasonal fluctuations in industries reliant on welders. For instance, construction work may peak during warmer months, leading to temporary increases in demand and wages.
Job Growth Projections
Regarding job growth projections, the welding technician field is poised for steady expansion. According to the Bureau of Labor Statistics, the demand for welding professionals is expected to grow by 3% over the next decade. This growth rate, while modest, translates into thousands of new jobs opening up as the industry adapts to technological advancements and evolving market needs.
Several factors contribute to the increasing demand for welders:
- Infrastructure Development: Ongoing investments in infrastructure create a consistent need for welding services. Repair and maintenance of existing structures will also sustain job levels.
- Technological Advancements: Automation and robotics in welding enhance productivity and may increase the demand for skilled technicians who can operate and maintain advanced equipment.
- Industry Diversification: As industries evolve, new sectors like renewable energy are emerging, which rely on welding expertise.
Health and Safety Considerations
Health and safety are paramount in the welding industry, influencing not only the well-being of technicians but also the quality of work produced. Welding involves exposure to various hazards including fumes, heat, and physical dangers from equipment. Therefore, a comprehensive understanding of safety protocols is essential for effective risk management.
Effective safety measures contribute to creating a secure working environment, reducing accidents, and enhancing overall productivity. Welding technicians must comply with established safety regulations and continually educate themselves about best practices in the field. This proactive approach not only protects individual workers but also cultivates a culture of safety within the organization.
"Prioritizing health and safety in welding is not just a requirement; it is a commitment to excellence in the profession."
Safety Protocols in Welding
Safety protocols in welding serve as guidelines to mitigate risks associated with the trade. These protocols include the following:
- Proper Ventilation: Adequate ventilation is crucial for dissipating harmful fumes and gases produced during welding. Technicians should work in well-ventilated areas or use exhaust systems.
- Fire Safety Measures: Working with flammable materials makes fire safety critical. This includes keeping fire extinguishers accessible and removing combustibles from the work area.
- Electrical Safety: Welders must ensure that all electrical equipment is in good condition and correctly grounded. Regular inspections and using equipment according to manufacturer guidelines are essential to prevent electrical hazards.
Additionally, technicians must follow specific welding standards established by organizations such as OSHA. Being familiar with these regulations can not only ensure compliance but also enhance workplace safety.
Protective Equipment and Best Practices
Protective equipment is a fundamental component of safe welding practices. The following items are vital for minimizing exposure to hazards:
- Welding Helmets: These protect the face and eyes from harmful UV rays and flying debris. Automated darkening helmets offer the advantage of instantaneous adjustments to light levels.
- Gloves: Heat-resistant gloves are essential for protecting hands from burns and injuries. Proper fit ensures better control and dexterity while welding.
- Respirators: When working in environments with harmful fumes, using appropriate respirators can prevent respiratory issues.
- Protective Clothing: Flame-resistant clothing should fit well to prevent entrapment while allowing free movement.
In addition to these protective measures, adhering to good practices is critical. This includes:
- Periodically inspecting all gear for damage.
- Maintaining a clutter-free workspace to reduce trip hazards.
- Continuously educating oneself about new safety practices and technologies.
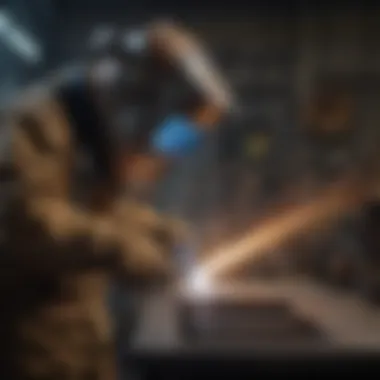
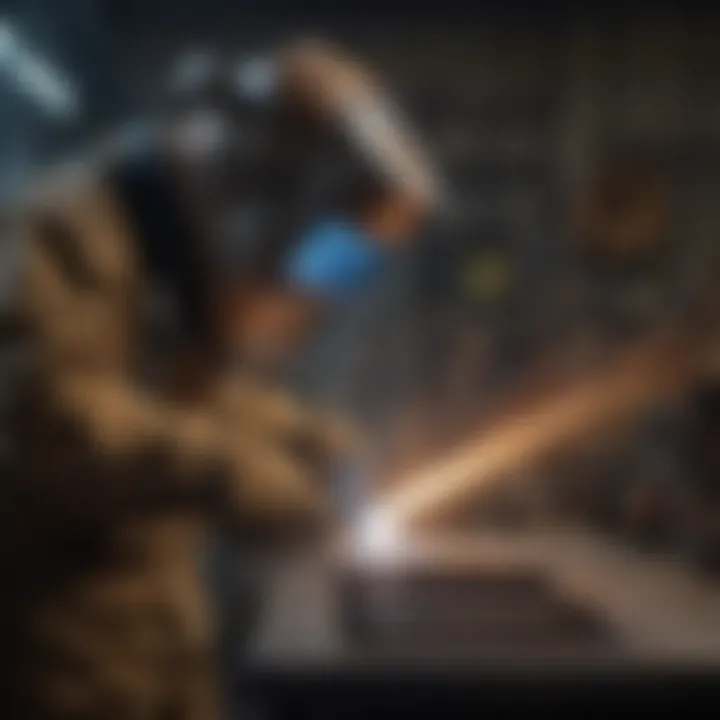
By understanding and implementing stringent health and safety protocols, welding technicians can safeguard their health and create a safer workplace for all.
Technological Advances in Welding
In the last few decades, the welding industry has been transformed through significant technological advances. These adaptations not only streamline processes but also enhance the quality and safety of jobs. Understanding these advances is vital for welding technicians, as they are key to remaining competitive and efficient in the field. The integration of modern machinery and digital solutions represents a leap forward that cannot be overlooked.
Automation and Robotics in Welding
Automation in welding has revolutionized traditional processes. Robotic welding systems, such as those developed by companies like ABB and KUKA, can execute repetitive tasks with precision and speed. This leads to:
- Increased efficiency
- Reduced human error
- Consistent output quality
Moreover, the utilization of robotic arms reduces labor costs, making production more viable economically. In industries like automotive and aerospace, where precision is critical, robotic welding minimizes the risk of defects and enhances overall productivity.
However, the shift to automation requires a skilled workforce that understands both the technology itself and welding techniques. Technicians must adapt to operate and maintain these systems, which often includes programming and troubleshooting. This creates a need for ongoing training to ensure that professionals are well-versed in modern equipment.
Emerging Welding Technologies
Emerging welding technologies offer innovative solutions to traditional problems. For instance, laser welding technology, which uses focused beams of light to melt materials, provides high precision and is often used in the electronics and medical sectors. Key benefits include:
- High speed
- Less heat input, resulting in a smaller thermal affect area
- Ability to weld thin materials without distortion
Furthermore, friction stir welding is gaining traction, especially in manufacturing and shipbuilding. This technique involves mechanically stirring the materials to be joined, creating a solid-state weld without melting. Such advancements lead to stronger joints and create possibilities for new applications in materials that are typically challenging to weld.
In addition to these technologies, the development of advanced welding consumables has greatly improved overall performance. New alloys and filler materials are designed to enhance strength, corrosion resistance, and weldability, making them suitable for diverse applications.
Adapting to these emerging technologies is crucial for welding technicians. Continuous education remains essential for achieving mastery in these methods and maintaining a competitive edge in a rapidly evolving job landscape. As welding becomes increasingly sophisticated, professionals who engage with these advancements will benefit from improved job security and expanded career possibilities.
"Being at the forefront of welding technology allows professionals not only to excel in their workmanship but also to open doors to new and innovative project opportunities."
Ultimately, embracing technological advances is not just a choice but a necessity for those in the welding field. As industries continue to evolve, the demand for skilled technicians who are proficient in both traditional and cutting-edge techniques will only grow.
Industry Applications of Welding
Welding is a fundamental process that plays a crucial role across various industries. Understanding the industry applications of welding helps to highlight the versatility and importance of the welding technician profession. Welders are not only essential for fabricating structures but also for maintaining and repairing existing frameworks. This section elucidates the specific roles welding plays in diverse sectors, emphasizing the skills technicians need to thrive in these environments.
Welding in Construction
The construction industry heavily relies on welding as a method for joining materials, particularly metals. Buildings, bridges, and infrastructures require robust connections, and welding offers strength that other joining methods often cannot match. Tasks may include steel framework assembly, pipeline installation, and metal sheeting for roof construction.
Welders in construction must possess an understanding of structural engineering principles. They need to interpret blueprints effectively, ensuring that designs are accurately executed. Safety is crucial, as construction sites can be hazardous. It is vital for welders to adhere to strict safety protocols to prevent accidents. The ability to work outdoors and adapt to various environmental conditions is also essential.
Moreover, construction welding is often time-sensitive, which means welders should be skilled in both techniques and equipment usage. Automated welding tools, such as robotic welders, are becoming more prevalent in this sector, requiring technicians to stay updated on technology advancements. Strong collaboration skills are necessary as welders frequently engage with other tradespeople to complete projects efficiently.
Aerospace and Automotive Welding
Welding in the aerospace and automotive industries presents unique challenges and demands a higher level of precision compared to other sectors. In aerospace, components must meet stringent safety standards as they are integral to flight safety. Welded parts must undergo rigorous testing to ensure they can withstand extreme conditions. This includes using advanced materials that often require specialized welding techniques such as TIG (Tungsten Inert Gas) welding.
In the automotive sector, welding is crucial for assembling various vehicle parts. Modern vehicles often use lightweight materials to enhance fuel efficiency, and customizations require skilled welders who can adapt to different materials. Knowing how to weld aluminum and advanced high-strength steel is increasingly important.
Both industries benefit from a focus on continuous improvement and innovation. Welders must engage in ongoing training to keep up with industry standards and technological advancements. The trend towards sustainable manufacturing also impacts welding practices in these fields, with an emphasis on reducing waste and emissions.
"Welding is not just about joining materials; it's about ensuring structural integrity and safety across diverse applications."
In summary, the industry applications of welding underscore the profession's significance. Whether the task is erecting skyscrapers or fabricating components for commercial aircraft, welding technicians play an invaluable role. Their adaptability, technical skill, and commitment to safety position them as essential players in modern manufacturing and construction.
Future of Welding Technician Jobs
The welding industry is evolving rapidly, driven by technological advancements and changing market demands. A clear vision of the future reveals opportunities and challenges that welding technicians must navigate. The role of a welding technician is becoming increasingly crucial not only in manufacturing sectors but also in industries like renewable energy and robotics. As such, it is essential to stay informed about emerging trends that could impact career prospects and job requirements.
This section explores key elements that define the future of welding technician jobs, highlighting the benefits of continual learning and the necessity for skilled professionals who can adapt to new technologies. A proactive approach can ensure that technicians remain relevant in an ever-evolving field.
Upskilling and Lifelong Learning
In todayโs fast-paced world, the concept of lifelong learning takes on a new significance, especially for welding technicians. The introduction of advanced technologies, such as automation and robotics, demands that welders enhance their skills continuously. Continuing education is essential not only for mastering new tools but also for improving safety standards and efficiency in the workplace.
Welders who engage in ongoing training programs can gain certifications in specialized techniques, which makes them more attractive to employers. Workshops, online courses, and community college classes provide valuable learning opportunities. Additionally, mentorship programs can foster growth, allowing less experienced technicians to learn from seasoned professionals.
Staying updated with welding trends is crucial. For example, familiarizing oneself with digital welding equipment and artificial intelligence applications can provide a competitive edge.
- Advantages of a commitment to lifelong learning:
- Better job opportunities
- Increased earning potential
- Improved job satisfaction
Environmentally Sustainable Practices in Welding
As industries face increasing scrutiny over their environmental impact, welding technicians must adapt to sustainable practices. The welding field is no exception, as eco-friendly methods and materials gain traction. Understanding environmental laws and regulations becomes essential for technicians aiming to work in green industries.
Techniques such as laser welding, which minimizes waste, and using less harmful welding rods contribute to sustainability. Moreover, optimizing processes can reduce energy consumption, thus lowering the carbon footprint.
Welders will benefit by incorporating environmentally responsible practices into their work. Not only does this appeal to environmentally conscious employers, but it also prepares them to work in sectors focusing on green innovations, such as renewable energy and sustainable construction.
"Adopting environmentally sustainable practices is not just a trend; it is a necessity for the future success of welding professionals."