Integrating Welders and Air Compressors in Agriculture
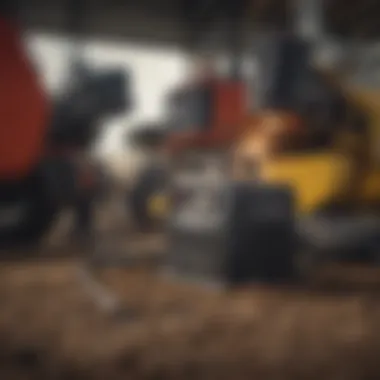
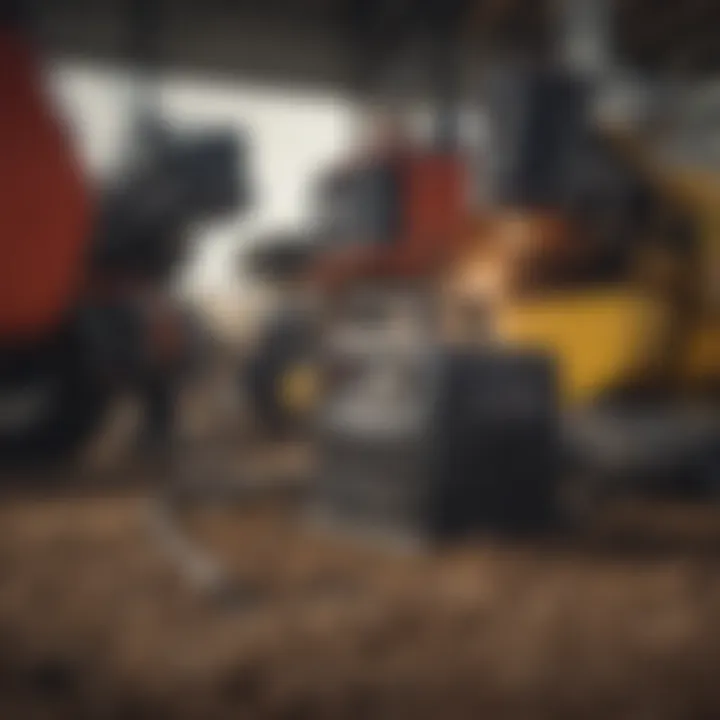
Intro
The integration of welders and air compressors is gaining momentum within agricultural applications. This trend stems from the increasing need for efficiency and versatility in farming operations. In this article, we delve into how these tools can synergize to enhance productivity in the agricultural sector. Understanding the key concepts, current trends, and practical applications will provide farmers and enthusiasts with tangible insights for optimizing their work processes.
Key Concepts and Terminology
Definition of Terms
To effectively grasp the integration of welders with air compressors, it is essential to define a few key terms.
Welder: A welder is a tool used to join metal parts together by melting the edges and allowing the molten metal to cool and solidify.
Air Compressor: An air compressor is a device that converts power into potential energy stored in pressurized air. This compressed air can then be utilized to power various tools and for various applications, including welding.
Overview of Relevant Practices
Integrating welders with air compressors involves several practices. Farmers may use MIG welding techniques coupled with compressed air to maintain and fabricate equipment. Additionally, air compressors may also power pneumatic tools that complement welding tasks. Understanding these connections can significantly impact the workflow and operational efficiency in agricultural settings.
Current Trends and Innovations
Latest Research and Developments
Recent research in agricultural technology indicates a growing trend towards automation, where both welding and compressed air systems are integrated into automated workflows. This includes the use of robotic systems for welding tasks that can be powered by air compressors, enhancing precision and reducing labor costs.
Emerging Technologies and Tools
Emerging technologies in this field include portable welders and compact air compressors. These tools are designed for ease of use in the field, allowing farmers to perform maintenance and repairs on-site without needing to transport equipment back to a workshop. This advance supports greater flexibility and immediate problem-solving in agricultural operations.
Practical Applications
Step-by-Step Guides
- Assessing Equipment Needs: Identify which tools are necessary for your specific agricultural tasks. Consider the type of welding work and the role of compressed air in your operations.
- Setting Up the Workspace: Create a dedicated area for welding that has adequate ventilation, safety gear, and a reliable power source.
- Connecting Tools: Ensure the air compressor is properly connected to the welder. Check that all connections are secure to prevent pressure loss.
- Testing the Setup: Before commencing any task, perform a test run to ensure everything operates smoothly. This step is crucial for safety and efficiency.
- Executing Welding Tasks: Follow standard welding practices while utilizing the advantages offered by compressed air for cooling and cleaning metal pieces.
Troubleshooting Common Issues
- Inconsistent Welding Quality: Check the power supply and ensure the air compressor is functioning correctly. Insufficient pressure can lead to poor weld quality.
- Overheating: Ensure that the welder has cooled down and that the air compressor is blowing adequate air to keep the area cool.
- Noise Levels: If noise becomes a concern, consider using sound insulation or choosing quieter air compressor models.
"Integrating welders with air compressors can enhance productivity in agricultural operations, allowing for faster repairs and maintenance on-site."
Utilizing both tools effectively not only saves time but also empowers agricultural professionals to carry out complex tasks more independently.
By focusing on these aspects, this article aims to equip farmers and those interested in agriculture with knowledge that can translate into practical benefits on the ground.
Understanding the Functionalities of Welders
Welders play a vital role in agricultural applications, providing the necessary ability to manipulate and repair metal structures. Knowing how welders function is crucial for farmers and agricultural professionals who rely on robust machinery. This section delves into the functionalities of welders, emphasizing their importance in agricultural settings. By understanding different types, techniques, and applications of welding, professionals can make informed decisions about when and how to use this skill effectively in their work.
Types of Welders
MIG Welders
MIG welders, or Metal Inert Gas welders, are widely used in various industries, including agriculture. Their simplicity is a key aspect, allowing users to perform welding with greater ease. One of the most beneficial characteristics of MIG welders is their ability to weld thin materials without burning through. This feature is particularly advantageous for farmers who often work with lighter metal components in their equipment.
MIG welding utilizes a continuous wire feed, which enhances efficiency. Farmers benefit from the speed of this process, as it reduces the time needed for repairs and production. However, one disadvantage includes sensitivity to wind and drafts, which can affect the quality of the welds.
TIG Welders
TIG welders, or Tungsten Inert Gas welders, provide precision that is unmatched by other welding types. Their ability to create clean and strong welds makes them a favored choice for applications requiring high-quality results. This is crucial in agriculture, where machinery must withstand harsh conditions and heavy use.
A standout characteristic of TIG welders is the versatility in welding various metals, such as aluminum and stainless steel. However, the process can be slow, requiring skill and practice. While it may be time-consuming, the end results often justify the effort, making TIG welders a valuable asset in agricultural settings.
Stick Welders
Stick welders, or Shielded Metal Arc Welders, are known for their durability and ease of use. They are particularly beneficial for outdoor applications, which is vital in agricultural work where environmental factors play a role. The fundamental feature of stick welding is its ability to handle rust and dirty materials, making it appealing for farmers dealing with aging equipment.
One advantage of using stick welders is their lower equipment cost compared to MIG and TIG options. This can be important for small to mid-sized farming operations. However, the quality of the welds may not match that of MIG or TIG, which is something to consider based on the project at hand.
Welding Techniques in Agricultural Equipment
Repairing Machinery
Repairing machinery is a fundamental technique involving welders in agricultural applications. This method ensures that tools and equipment remain operational, minimizing downtime in the field. The hassle-free nature of welding repairs allows farmers to address issues quickly and efficiently. The key characteristic of this approach lies in its practicality; it is often more economical to repair machinery than to replace it entirely.
The unique feature of repairing machinery with welders is the ability to restore functionality while maintaining integrity. This process encourages sustainability by allowing farmers to extend the life of their equipment. However, the skill level required can present challenges, particularly for those new to welding.
Fabricating Components
Fabricating components often involves creating custom parts that fit specific needs in agricultural processes. This technique is advantageous as it fosters innovation and efficiency. By fabricating components, farmers can design solutions tailored to their operational needs.
A notable characteristic of fabrication is its adaptability; welders can produce a wide range of parts, from brackets to support structures. The unique feature of customized fabrication can lead to greatly improved workflows. Yet, it demands skilled labor, as improper fabrication can hinder performance.
Custom Modifications
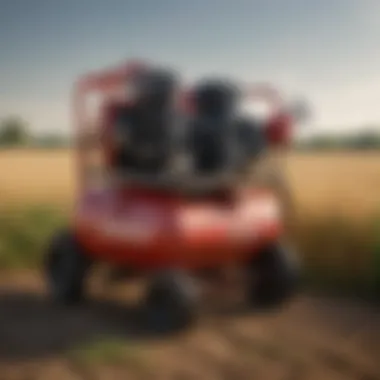
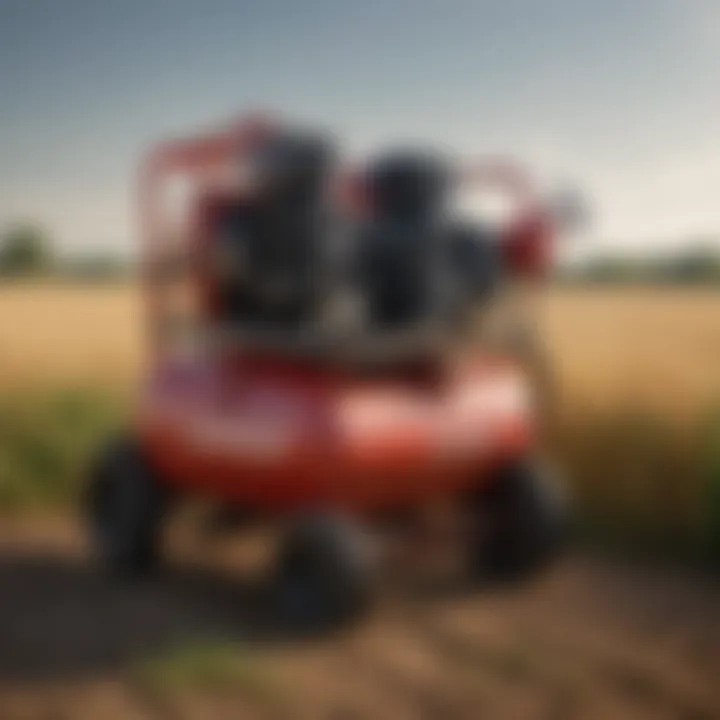
Custom modifications enhance the effectiveness of existing equipment, allowing it to perform tasks more efficiently. This technique supports the evolution of agricultural technology and practices. Its importance lies in the ability to adapt machinery to meet unique farming requirements.
The flexibility offered by custom modifications means that farmers can upgrade their equipment without purchasing new machines. However, this requires understanding specific needs and potential design constraints, which may present a challenge for some operators.
Exploring Air Compressors in Agriculture
Air compressors play a vital role in modern agricultural practices. Their ability to provide a consistent and high-pressure air supply makes them advantageous for various farming applications, ranging from maintenance tasks to enhancing the efficiency of machinery. In this section, we will discuss the types of air compressors available and their specific applications in the agricultural sector. By examining these areas, we highlight the relevance of air compressors, ensuring that agricultural professionals can maximize their benefits.
Types of Air Compressors
Different types of air compressors serve various purposes in agriculture. Understanding these options helps farmers choose the right compressor that suits their specific needs.
Portable Air Compressors
Portable air compressors are lightweight and easy to transport. Their mobility is a key characteristic, making them suitable for on-the-go tasks. Farmers often use them for inflating tires or powering smaller pneumatic tools in different locations around the farm. A unique feature of portable air compressors is their quick setup, which allows for immediate use without extensive preparation.
However, their power limitations compared to stationary models can restrict their use for high-demand tasks.
Stationary Air Compressors
Stationary air compressors are designed for more permanent setups. They are typically more powerful than portable compressors, making them a popular choice for farms with more demanding air requirements. These compressors support various applications like powering larger machinery. Their main characteristic is durability, often built to withstand heavy use over time.
The downside is their lack of mobility; once installed, relocating them can be complex and costly. This should be considered based on the specific farming operations.
Oil-Free Compressors
Oil-free compressors offer an alternative where oils and other lubricants can be a concern. They are suitable for operations requiring clean air, such as cleaning equipment or managing delicate tasks. The main advantage of oil-free compressors is the reduced maintenance needs and the elimination of oil contamination risks. However, they may lack the longevity and durability typical of their oil-lubricated counterparts. Understanding these trade-offs can help farmers decide when an oil-free compressor is most beneficial.
Applications of Air Compressors in Farming
The applications of air compressors in agriculture cover a broad spectrum. Their versatility contributes to overall efficiency and effectiveness in various tasks.
Inflating Tires
Inflating tires is a basic yet crucial application of air compressors in agriculture. Keeping tires inflated properly enhances fuel efficiency and vehicle performance on rough terrains. This is a straightforward benefit of using air compressors, as maintaining correct pressure can also prolong the lifespan of tires. Ensuring that farmers have access to portable compressors can greatly assist in this regard, making tire maintenance quick and efficient.
Powering Pneumatic Tools
Pneumatic tools, such as drills and wrenches, rely heavily on air compressors for operation. These tools offer greater efficiency compared to their manual counterparts. Thus, using air compressors to power them can significantly speed up tasks like repairs or equipment assembly on the farm. The benefit here is in the reduced labor time and increased productivity. Still, farmers must match air compressor specifications to the tools used to avoid performance issues.
Cleaning Equipment
Cleaning equipment is another essential application of air compressors. They can quickly remove dirt, debris, and dust from farming tools and machinery, helping maintain optimal operating conditions. The high-pressure air stream can reach areas that traditional cleaning methods cannot easily access. However, as with all applications, attention to equipment compatibility is necessary. Improper use might lead to damage or insufficient cleaning.
Air compressors not only enhance efficiency but also extend the lifespan of critical farm equipment through proper maintenance practices.
In summary, understanding the different types of air compressors and their applications allows farmers to make informed decisions on the equipment that best suits their agricultural needs. The integration of air compressors within farming operations leads to enhanced productivity and operational efficiency.
Benefits of Combining Welders with Air Compressors
The integration of welders and air compressors in agricultural settings brings multifaceted advantages that significantly enhance productivity and operational efficiency. Understanding these benefits is crucial for farmers and equipment operators looking to optimize their workflows. This section explores key areas where the combination of these tools can lead to tangible improvements in agricultural applications.
Increased Operational Efficiency
Streamlined Workflows
Streamlined workflows emerge as one of the main advantages of using welders in conjunction with air compressors. This is characterized by reducing the time spent switching between different pieces of equipment. By using a welder and an air compressor in tandem, tasks can be completed more quickly, as operators can use the compressor to power tools immediately following welding tasks. This efficiency means that farmers can handle more repairs and modifications in less time, directly translating into increased equipment uptime.
p>Time saved on workflows can lead to higher output during busy seasons. However, the need for proper training on how to best utilize both machines remains essential. If workflows are not adequately planned out, the anticipated efficiency may not be realized.p>
Reduced Downtime
Minimizing downtime in farming operations is critical. Reduction in downtimes occurs as the use of welders and air compressors allows for rapid repairs in the field. If a piece of agricultural machinery breaks down, having these tools at hand can facilitate quick repairs, allowing work to resume with minimal delay. This characteristic makes it beneficial for farmers who rely on continuous operation to meet production demands.
p>Despite the advantages, it is important to have protocols in place for regular maintenance of both machines to prevent unexpected failures, as this could ironically lead to increased downtime.p>
Enhanced Productivity
Enhanced productivity is a natural outcome of the seamless integration of welders and air compressors. Farmers can increase their output by engaging in custom fabrication or repairs as needed. For instance, when farmers can quickly fix broken parts or modify tools on-site, they can accomplish more tasks in a shorter time frame. This feature adds a layer of flexibility to agricultural operations that was not traditionally available.
p>However, with increased productivity comes the responsibility of ensuring that quality standards are met. Rushing tasks without proper procedures can lead to poor workmanship and ultimately affect operation longevity.p>
Cost-Effectiveness
Lower Fuel Consumption
Lower fuel consumption reflects a significant cost-saving benefit when welders and air compressors are integrated effectively. The combined use of these tools can lead to reduced energy costs, particularly when compared to using multiple machines designed for singular purposes. This efficiency results from optimizing the energy needed for welding and air compression without the need for excessive fuel use.
p>With fuel costs consistently fluctuating, this benefit is especially relevant for agricultural operators navigating tight margins.p>
Minimized Equipment Wear
Minimized equipment wear represents another vital aspect of cost-effectiveness. When air compressors and welders are used together appropriately, the strain on machinery can be reduced. Both tools can be operated in a synchronized manner, allowing for less wear and tear on the equipment, leading to extended equipment lifespan. Farmers can save on replacement costs over time.
p>However, increased operational hours could also lead to faster depreciation if the machines are not maintained regularly.p>
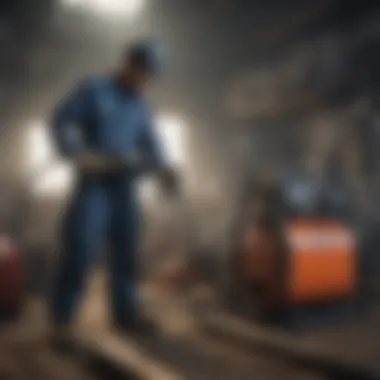
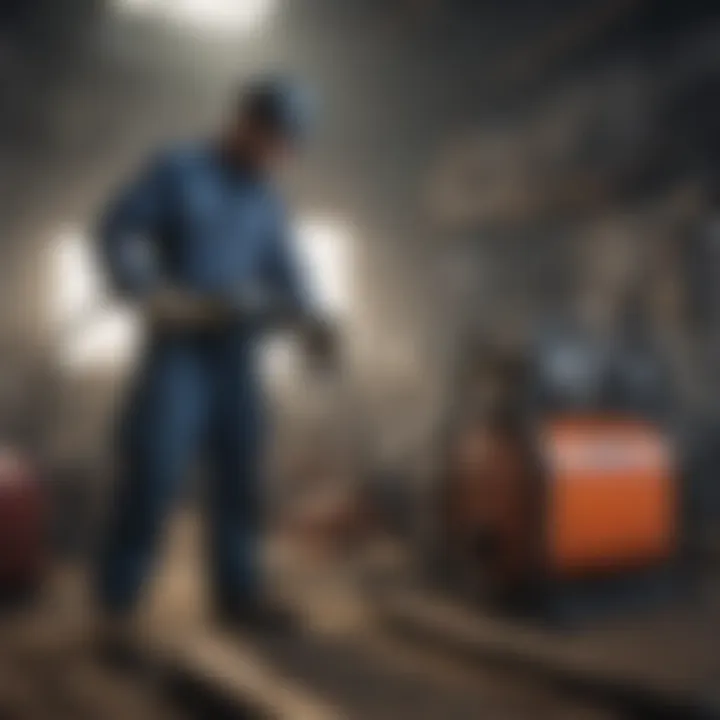
Improved Resource Management
Improved resource management through the combination of welders and air compressors leads to more efficient use of materials and labor. Having both tools on hand means better planning and execution of tasks without needing to source additional equipment. This consolidation leads to lower operational costs and allows for more focused oversight of resource consumption.
p>While it streamlines resources allocation, an emphasis must also be placed on training staff adequately, as improper use could negate these benefits.p>
In summary, combining welders and air compressors in agricultural applications isn't just advantageous but essential for optimizing efficiency and cost-effectiveness. Understanding each benefit and its implementation can significantly influence operational success.
Operational Considerations for Using Welders with Air Compressors
Integrating welders with air compressors in agricultural applications demands careful consideration of several operational factors. Specifically, choosing the right equipment and establishing safety protocols should not be overlooked. When done correctly, these considerations lead to enhanced efficiency and safer work environments for all operators.
Choosing the Right Equipment
Matching Specifications
Matching specifications involves ensuring that both the welder and air compressor are compatible in terms of output and functionality. This aspect is crucial as it directly affects the performance and longevity of both pieces of equipment. For agricultural tasks, using machines that complement each other's specifications can lead to more streamlined operations. A beneficial choice in this context is having similar power outputs, which facilitates efficient energy use.
Unique features depend on the tasks at hand. For instance, opting for machines that can handle thick materials and high-pressure tasks can enhance repair processes on heavy equipment. However, an inappropriate match can cause inefficiencies or equipment damage.
Understanding Power Requirements
Understanding power requirements is essential in the integration process. The welder's demands for electrical current must be met by the air compressor's capabilities. Selecting equipment with the correct power outputs prevents overheating and ensures reliable performance.
This understanding is beneficial because it allows for optimal resource utilization in agricultural settings. If a compressor cannot support the welder's power needs, it becomes prone to failures. Conversely, oversizing can increase costs unnecessarily.
Catering to Specific Tasks
Catering to specific tasks means identifying the unique needs of your agricultural work and selecting the correct welder and compressor for that purpose. This choice ensures that the equipment can handle the actual workloads in farming efficiently, contributing to higher productivity.
Choosing tools that address specific challenges, such as mobile repairs in the field, can also be very useful. However, limiting oneself to specific task-oriented equipment may restrict broader operational capabilities in a diverse agricultural environment.
Safety Protocols
Personal Protective Equipment
Personal protective equipment (PPE) is critical for ensuring the safety of operators when using welders and air compressors. This includes items such as gloves, helmets, and protective eyewear. Such gear significantly reduces the risk of injury from sparks, heat, and other hazards associated with welding processes.
The key characteristic of proper PPE is its ability to provide adequate protection while allowing for ease of movement. When operators wear comfortable, well-fitted PPE, they are more likely to work efficiently and focus on the task.
Safe Handling Practices
Safe handling practices involve following guidelines for the operation and maintenance of equipment. These practices should be standard in any setting involving welders and air compressors. It includes proper positioning of hoses, careful handling of tools, and regular checks for wear and tear.
This aspect is crucial because safe handling reduces the potential for accidents and equipment malfunctions. Practicing such safety measures builds a culture of safety within the farming operation, leading to overall increased productivity.
Emergency Preparedness
Having an emergency preparedness plan is vital in any agricultural setting that uses welders and air compressors. This plan should outline steps to take in case of accidents, including fire outbreaks or equipment failures. The presence of fire extinguishers and first aid kits is a necessity.
The importance of such preparedness lies in minimizing the response time during an incident, potentially reducing damage and injury. A well-prepared team is more likely to react swiftly and effectively, ensuring the safety of personnel and equipment.
Maintenance of Welders and Air Compressors
Maintaining welders and air compressors is critical in agricultural applications. It ensures that these essential tools operate efficiently, reduces the risk of breakdowns, and prolongs their lifespan. Regular maintenance minimizes downtime, which is vital in busy agricultural seasons. Proper care can also prevent costly repairs and ensure optimal performance when integrating these machines in the field.
Routine Maintenance Practices
Regular Inspections
Regular inspections involve reviewing the equipment for any signs of wear or malfunction. This practice is pivotal in catching issues before they escalate to more significant problems. It helps identify not just apparent faults but also underlying issues that may not be visible to the naked eye.
A key characteristic of regular inspections is their preventative nature. They help maintain operational integrity and ensure safety standards are followed. In this article, it is a popular choice for ensuring that both welders and compressors are functioning correctly. The unique feature of regular inspections lies in their ability to provide a routine checkup without the necessity of extensive tools or expertise. Regular inspections can significantly reduce the likelihood of unexpected breakdowns, thus maintaining productivity in agricultural operations.
Cleaning and Lubrication
Cleaning and lubrication are essential practices that contribute directly to the longevity and functionality of welding and air compressing equipment. Over time, dust and debris can accumulate, potentially hindering performance. Regular cleaning ensures that equipment remains free from contaminants, which can damage parts and affect efficiency.
One of the key characteristics of cleaning and lubrication is their role in friction reduction. Proper lubrication minimizes the wear and tear of moving parts. This choice is beneficial as it can lead to smoother operation and lower energy consumption. The unique feature of this practice is that it can easily be integrated into routine maintenance schedules. However, neglecting these aspects can lead to significant performance declines, which can be detrimental in an agricultural setting.
Parts Replacement
Parts replacement is a crucial aspect of maintenance that addresses wear over time. As equipment ages, certain components are likely to wear out faster than others. This practice is essential to maintain the overall integrity and performance of welders and air compressors.
A fundamental characteristic of parts replacement is its contribution to reliability. Replacing worn parts ensures that the equipment can perform as expected without unexpected failures. It is a popular choice for maintenance in this article because of the direct impact on equipment productivity. The unique feature of parts replacement is that it often involves scheduled updates and preventive measures. Making timely replacements can avert larger breakdowns, saving time and resources.
Troubleshooting Common Issues
Electrical Problems
Electrical problems commonly affect welders and air compressors, impacting their performance. These issues can stem from various sources, including poor connections or overloaded circuits. Understanding these problems contributes immensely to the operational effectiveness of agricultural tools.
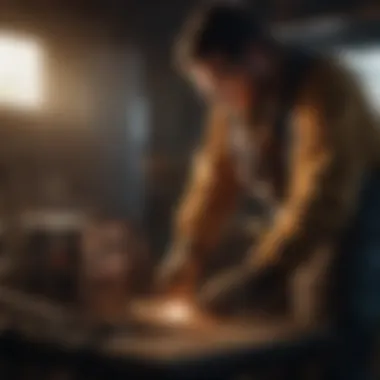
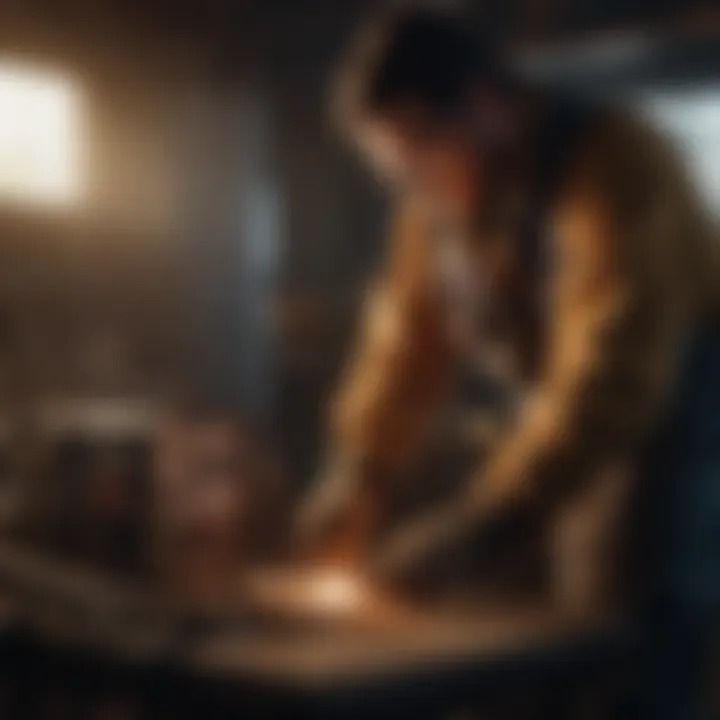
The key characteristic of electrical issues is their potential to halt work completely. Recognizing these signs early can mitigate risks and ensure that projects are completed on time. Troubleshooting for electrical problems is a beneficial choice in this article because these issues can lead to significant delays. The unique aspect of these problems is that they often require careful inspection and sometimes professional intervention to resolve fully.
Performance Issues
Performance issues can manifest in multiple forms, such as insufficient power output or inconsistent operation. These issues can severely affect productivity and the quality of work done in the agricultural sector. Recognizing and addressing these performance-related issues early is vital for maintaining effective workflow.
A key characteristic of performance issues is their immediate impact on operational results. Identifying these complications prompts timely action, preventing further complications down the line. Troubleshooting performance issues is beneficial for this article, as it encourages proactive maintenance and operational awareness. Performance issues often require a thorough analysis of both the welder and the compressor to find the right fix.
Calibrating Equipment
Calibrating equipment involves adjusting the settings to ensure optimal performance. This process is essential to guarantee that both welders and air compressors function within their designated parameters. Proper calibration makes sure that the tools meet the specific requirements of any given task.
A critical characteristic of calibration is its role in enhancing performance accuracy. Properly calibrated equipment minimizes the potential for errors during operation. It is a beneficial practice outlined in this article because it ensures that tools deliver consistent results. The unique feature of calibrating equipment is that it not only boosts productivity but also improves the quality of the output in agricultural applications.
Regular maintenance and troubleshooting are essential for maximizing the performance of welders and compressors in agriculture.
Ensuring the integrity of these tools through routine practices and addressing underlying issues extends their lifespan and utility.
Case Studies: Successful Integration in Agricultural Operations
The integration of welders with air compressors in agricultural operations provides numerous real-world benefits. This section highlights actual case studies that demonstrate the effective use of these tools together, showcasing how they can improve efficiency and productivity in the field. Studying successful implementations can help professionals understand the specific elements and considerations necessary for integrating these technologies.
Innovative Applications in Crop Farming
On-Site Repairs
On-site repairs represent a critical aspect of maintaining operational efficiency in agricultural settings. When equipment breaks down, having access to welding and compressor tools on-location allows for immediate repairs, avoiding prolonged downtime. A key characteristic of these on-site solutions is their mobility; portable welders and air compressors can be transported to various locations on the farm.
These repairs are beneficial because they enable farmers to quickly address issues without needing to haul equipment to a distant workshop. The unique feature of on-site repairs includes a combination of welding capabilities and pneumatic tools. For instance, a farmer can instantly patch a damaged irrigation line and use pneumatic equipment for additional tasks. However, there are some disadvantages, such as the need for skilled operators who can effectively use both types of equipment simultaneously.
Custom Equipment Fabrication
Custom equipment fabrication is another powerful application stemming from the combination of welders and air compressors. This process allows farmers to create equipment tailored to their specific needs. The key characteristic of this practice is its flexibility—farmers can modify or create tools that enhance their particular farming techniques.
The unique feature of custom fabrication involves using welding to construct and assemble new equipment directly on-site. This method enables tailored design, which can lead to more efficient operations. However, the process can also be time-consuming and may require significant technical knowledge to ensure safety and effectiveness.
Workshops and Training Opportunities
Skilled Labor Development
Skilled labor development is essential to maximize the benefits of integrating welders and air compressors. Training programs focus on teaching individuals how to effectively use these tools in agricultural settings. One key characteristic of such programs is their hands-on approach; participants often engage in practical exercises that mimic real-world scenarios.
By developing skilled labor, farms are better equipped to handle repairs and custom fabrication tasks. The unique feature of these training programs is their dual focus on both welding techniques and pneumatic applications, ensuring a comprehensive skill set. However, these workshops can be limited by resource availability and may not always be accessible to everyone.
Industry Partnerships
Industry partnerships play a crucial role in enhancing the integration of welders and air compressors. Collaborations between agricultural education institutions and local businesses can lead to innovative training programs and resource sharing. A notable characteristic of these partnerships is their ability to connect skilled labor with practical opportunities in the field.
These partnerships benefit farms by providing access to state-of-the-art equipment and expert guidance, helping ensure that best practices are followed. The unique feature of industry partnerships is their potential for continuous improvement and innovation through shared knowledge. On the downside, establishing effective partnerships can take time and effort, requiring ongoing communication and alignment of goals.
Future Trends and Innovations
This section explores the latest developments in the integration of welders and air compressors for agricultural applications. Understanding future trends is crucial for farmers and professionals who seek to optimize their operations. This knowledge enables them to stay competitive and embrace methods that enhance efficiency and sustainability.
Technological Advancements
Smart Welding Solutions
Smart welding solutions encompass advanced technologies that improve effectiveness and accuracy in welding tasks. These solutions often integrate automation and data analytics, allowing for real-time monitoring and adjustments. One key characteristic of smart welding solutions is their ability to connect with various devices to enable remote monitoring and control.
The ability to track performance data can lead to significant improvements in quality and consistency, which is essential in agricultural equipment maintenance. Key benefits include increased speed, reduced waste material, and minimized defects, making them a popular choice in agricultural operations.
However, while offering many advantages, smart welding solutions can also be complex to implement, requiring training and a degree of upfront investment.
Energy Efficient Compressors
Energy efficient compressors represent a significant advancement in the realm of air compressors used in agriculture. These compressors are designed to consume less power while delivering the same or improved levels of performance. Their key feature is the incorporation of innovative motor technologies and smart controls that optimize energy use.
Using energy efficient compressors can lead to substantial savings on electricity bills, reducing operational costs over time. Additionally, they help in environmental sustainability by decreasing the overall energy consumption. However, the initial cost of these compressors can be high, which may deter some farmers from investing in them.
Sustainability Considerations
Eco-Friendly Welding Techniques
Eco-friendly welding techniques focus on minimizing environmental impact while maintaining high productivity levels. These methods utilize less harmful materials and emphasize recycling and waste reduction. A significant aspect is the use of consumables that produce fewer toxic emissions.
The key characteristic of these techniques is their ability to align with growing environmental regulations and societal expectations regarding sustainability in agriculture. They are becoming a preferred choice as they help businesses to meet compliance and enhance public image.
It’s important to note that these techniques may require additional training and investment in newer technologies, which can be a challenge for some organizations.
Reducing Carbon Footprint
Reducing the carbon footprint of agricultural operations is becoming increasingly vital as climate change concerns rise. This aspect involves adopting practices and technologies that lower greenhouse gas emissions associated with welding and compressor use. Key features include energy-efficient machinery, utilization of renewable energy sources, and optimizing existing processes to minimize waste.
Companies adopting measures to reduce their carbon footprint often benefit from improved regulatory compliance and enhanced reputation in the market. However, these measures can come with challenges, such as higher initial investment and the need for ongoing assessment of practices to ensure continued improvements.
Embracing future trends in technology and sustainability can significantly impact the efficiency and environmental responsibility of agricultural operations. By integrating advanced welding solutions and energy-efficient compressors, producers can achieve a substantial competitive advantage.