Understanding Metal Twister Machines: Innovations & Applications
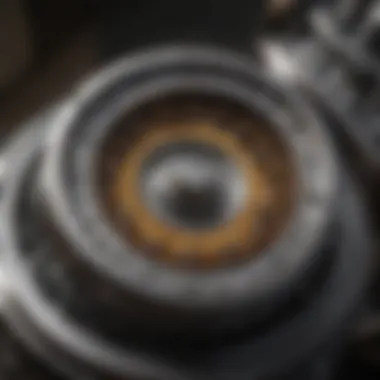
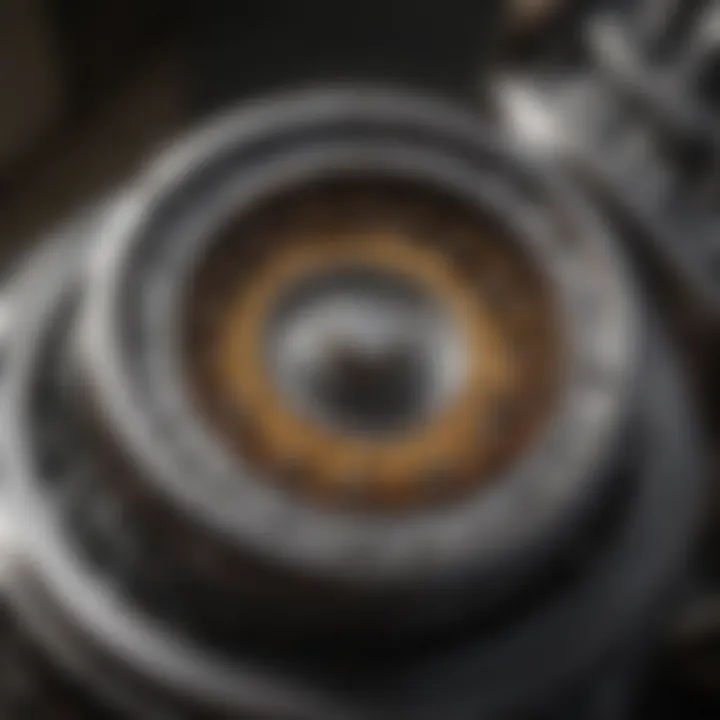
Intro
Metal twister machines are specialized devices designed for the intricate process of shaping and manipulating metal. They utilize innovative techniques to twist metal, creating various forms and structures essential in multiple industries. These machines have significant roles in agriculture, horticulture, and other manufacturing sectors, where efficiency and precision matter.
Understanding how these machines work is critical as they contribute to enhancing productivity and operational efficacy. Their design and functionality reflect advancements in technology, which enhances their utility across different applications. In the following sections, we will explore key concepts and terminology related to metal twister machines, current trends and innovations that shape their evolution, and practical applications demonstrating their effectiveness in the field.
Key Concepts and Terminology
Definition of Terms
Understanding specific terminology is vital when discussing metal twister machines. Here are some key terms:
- Metal Twister Machine: A device used to twist metal into specific shapes and forms for various applications.
- Torque: A measure of the rotational force applied in the twisting process.
- Workpiece: The metal material being manipulated by the machine.
- Die: A specialized tool used to shape the metal during the twisting process.
Overview of Relevant Practices
The process of using metal twister machines involves several steps:
- Setup: Preparing the machine requires aligning the workpiece correctly.
- Twisting: The operator applies torque, creating the desired shape.
- Finishing: After twisting, additional processes may be necessary to refine the workpiece.
These steps ensure efficiency and accuracy, which are paramount in industries that rely on precise metalwork. Understanding these practices helps users operate the machines effectively.
Current Trends and Innovations
Latest Research and Developments
Recent advancements have focused on increasing the efficiency and capabilities of metal twister machines. Research has led to the development of more robust components that can withstand higher stress levels. This improvement allows for quicker production cycles, a critical aspect of competitive manufacturing environments.
Emerging Technologies and Tools
Emerging technologies, such as computer numerical control (CNC) systems, are integrating into metal twister machines. These systems offer higher precision and automation, reducing the need for manual operation. As a result, they lower error rates and improve overall production quality.
Practical Applications
Step-by-Step Guides
To maximize the benefits of metal twister machines, users can follow practical guides, such as:
- Understanding Machine Specifications: Before operation, familiarize oneself with the machine's specifications.
- Proper Tool Selection: Choosing the right dies and tools for the job is crucial for optimal results.
- Regular Maintenance: Conducting regular maintenance prevents breakdowns and prolongs equipment life.
Troubleshooting Common Issues
Common problems may arise during operation. Here are some tips for effective troubleshooting:
- Uneven Twisting: Check for proper alignment of the workpiece.
- Excessive Wear on Tools: Regularly inspect and replace dies and other tool components.
- Machine Jams: Ensure there are no foreign objects causing obstructions.
"Understanding metal twister machines allows operators to enhance productivity significantly, providing higher-quality products with greater efficiency."
Prelude to Metal Twister Machines
Metal twister machines serve an essential function in various precision-dependent industries. Understanding these machines allows professionals to optimize their operations, enabling increased productivity and efficiency. This introduction sets the stage for grasping their mechanics and real-world applications.
Definition and Purpose
Metal twister machines are specialized tools designed to twist and shape metal materials. Their primary purpose is to provide consistent and precise bending or twisting of various metal components. This capability is crucial for creating specific shapes and forms required in metal fabrication. The machines are often utilized in sectors such as agriculture, automotive, and construction, where form and functionality are pivotal. Enhanced automation in these machines further simplifies complex tasks, allowing operators to achieve more with less manual effort.
Historical Background
The evolution of metal twister machines reflects advancements in both technology and industry needs. Initially, manual twisting techniques dominated, relying heavily on labor-intensive methods. With the Industrial Revolution, mechanization began to play a significant role. Early machines provided basic twisting functions but lacked precision. The introduction of computerized systems and programmable logic controllers in the late 20th century marked a turning point. These innovations made it possible to achieve higher accuracy and improve production rates significantly. As industries demand more sophisticated solutions, metal twister machines have adapted, integrating smart technologies and enhancing overall effectiveness in production tasks.
"The development of metal twister machines is closely linked to the growth of industrial manufacturing, representing a blend of tradition and innovation."
As we delve further into the mechanics and applications of these machines, it becomes evident how they are reshaping the landscape of various industries.
Mechanics of Metal Twister Machines
The topic of mechanics in metal twister machines is crucial for understanding their functionality and efficiency. A well-designed machine can significantly enhance productivity in various applications, notably in agriculture, manufacturing, and the automotive industry. The mechanical foundation dictates the machine's performance capabilities, impacting everything from precision to operational speed. This part will explore the core components and operating principles of these machines, emphasizing how they contribute to overall efficiency and reliability.
Core Components
Frame Construction
Frame construction serves as the skeleton of metal twister machines. A strong and durable frame is essential to support the machine's various parts and withstand significant operational stress. Generally made from high-quality steel or aluminum, the frame ensures stability during operation, which is critical for maintaining precision in twisting operations.

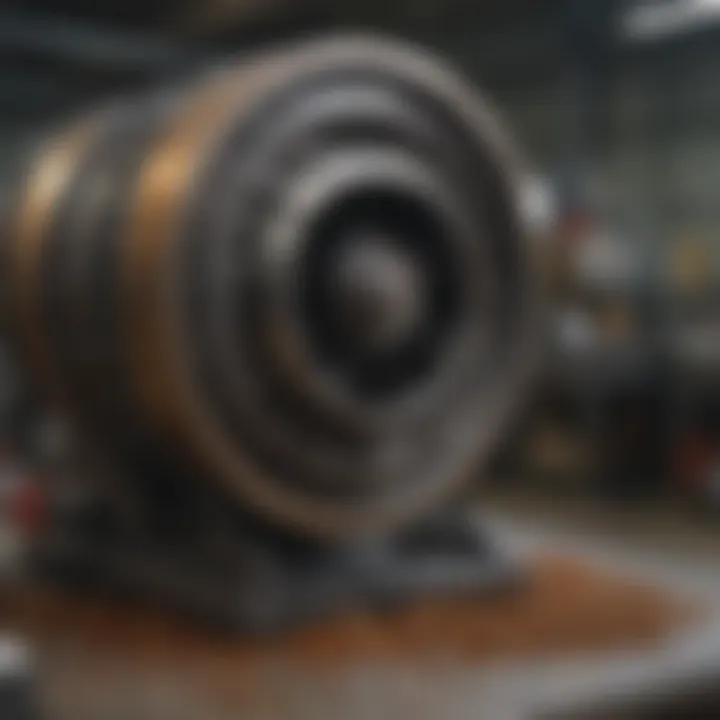
Key characteristic: The robustness of the frame allows it to handle heavy loads without warping or breaking. This characteristic makes it a favored choice in industries where safety and reliability are paramount.
One unique feature is the modular design often seen in modern frames. This design allows for easy modifications and repairs, a notable advantage for facilities that may need to adapt their machines for different tasks. While modular frames enhance flexibility, they may introduce slight complexities during assembly and require careful alignment during installation.
Twisting Mechanism
The twisting mechanism is at the heart of metal twister machines, responsible for the actual twisting motion of metal components. The effectiveness of this mechanism directly influences the quality of the finished product. It converts the rotational motion into the desired twisting action.
Key characteristic: Its precision is unmatched, providing consistent torque across various metal types. This consistency is especially beneficial for operations requiring high-quality standards.
A unique aspect is the use of advanced gearing systems that can adjust the resistance and speed according to material specifications. While these advanced systems offer advantages in performance and adaptability, they can increase maintenance needs and require skilled personnel to operate.
Control Systems
Control systems in metal twister machines play a pivotal role in managing operations effectively. They regulate the machine’s functions, such as speed, torque, and load handling, ensuring optimal performance.
Key characteristic: Sophisticated control systems enhance precision and reduce the risk of operator error, making them a vital addition in this context.
Modern systems often feature touchscreen interfaces, enabling operators to adjust settings quickly and monitor performance. A potential drawback is the learning curve associated with new technology; operators may need training to effectively utilize these advanced systems.
Operating Principles
Load Handling
Load handling is fundamental to the operations of metal twister machines. It involves managing the weight and material being processed, ensuring that the machines operate within their designed parameters. Proper load handling can prevent mechanical failure and enhance the machine's efficiency.
Key characteristic: The ability to support various load types without compromising performance is a major advantage.
A unique feature is the use of automated load sensors that adjust operations based on real-time data, enhancing safety and operational efficiency. While these sensors add a layer of complexity to the machine's design, they significantly increase reliability.
Torque Application
Torque application determines how effectively the twisting mechanism operates. It is essential for producing the desired twists in the metal. The application of precise torque ensures that materials are manipulated without damage.
Key characteristic: Consistent torque application leads to repeatable results, crucial for high-quality production.
Advanced torque management systems can dynamically alter the force applied based on material resistance. However, the complexity of these systems can pose challenges if maintenance or operator training is inadequate.
Speed Regulation
Speed regulation is vital in controlling how quickly a machine operates. It impacts efficiency and the quality of the finished product directly. Regulating speed allows for flexibility in operations, accommodating different materials and project requirements.
Key characteristic: Speed adjustments can lead to optimized production cycles, making machines more versatile.
One interesting feature is the implementation of variable frequency drives that enable smooth speed transitions. However, while these systems provide operational advantages, they can increase initial costs and require skilled technicians for setup and maintenance.
"Understanding the mechanics of metal twister machines is essential for maximizing their performance and efficiency across various industrial applications."
The End
The sections discussed illustrate that each component within metal twister machines plays a significant role. Understanding these mechanics not only enhances the efficiency of operations but also informs future innovations and improvements. As different industries push for higher standards, the mechanics of metal twister machines will likely evolve, paving the way for further advancements.
Applications in Various Industries
The application of metal twister machines spans across various industries, showcasing their role in enhancing productivity and efficiency. These machines are not limited to a single field; their versatility makes them valuable in agriculture, manufacturing, construction, and automotive sectors. Understanding these applications is fundamental to recognizing the broader impacts of metal twister machines on modern operations.
Agricultural Uses
Implementation in Farming Equipment
The implementation of metal twister machines in farming equipment is significant. These machines enable the creation of robust and intricate metal parts required for equipment such as plows, harvesters, and irrigation systems. A key characteristic of these machines is their ability to handle various metal types and sizes, which is vital in agriculture where equipment demands vary.
Unique to farming equipment, the twisting mechanism offers a precise method to reinforce metal components, ensuring durability even under harsh farm conditions. This trait can lower maintenance needs for machinery, leading to longer operational life and reduced downtime. However, the initial investment can be high, which might discourage some smaller operations from utilizing this technology.
Role in Crop Management
In crop management, metal twister machines play a crucial role in developing tools designed to enhance cultivation methods. By facilitating the production of specialized tools such as seeders and tillers, these machines contribute directly to crop yields. The advantage of utilizing twisted components lies in their improved strength and stability, making them ideal for various agricultural tasks.
Moreover, these machines support the growing trend towards precision farming. This method relies on accurate data and specialized tools for maximum efficiency. Nevertheless, the integration process may require thorough training and understanding of data management, which could pose challenges for some users.
Manufacturing and Construction
Metal Framing
In the context of manufacturing and construction, metal twister machines are integral to metal framing. The ability to twist and shape metal accurately allows for the rapid assembly of structures, such as buildings or frames for machinery. This efficiency is a distinct advantage, as it reduces overall construction time.
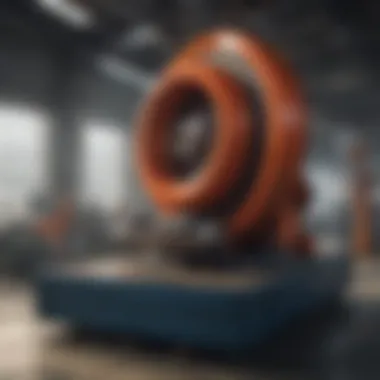
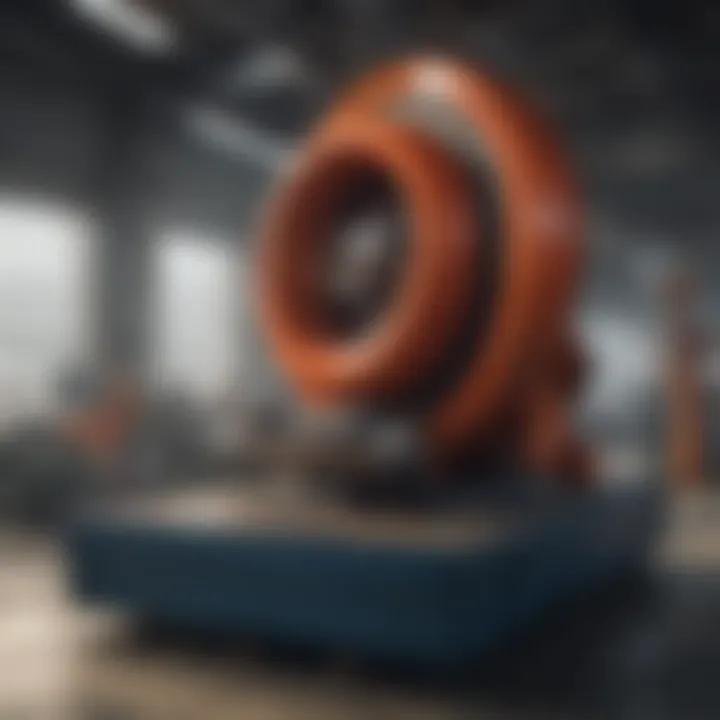
Additionally, metal framing is known for its strength-to-weight ratio. This feature makes it a favorable choice over traditional materials, highlighting the benefits of metal twister machines in promoting modern construction techniques. However, the need for skilled labor to operate these machines may limit their accessibility in certain regions.
Component Assembly
The component assembly aspect offers significant advantages as well. Metal twister machines facilitate the assembly of complex components, which is essential in creating cohesive products in manufacturing environments. The characteristic of speed and accuracy in assembly leads to increased production rates, contributing to overall profitability.
A unique feature of this process is the reduction of manual assembly errors. Automation through metal twisting reduces human error risk, streamlining the workflow significantly. On the downside, reliance on technology means that any malfunction could halt production, necessitating a reliable maintenance plan.
Automotive Industry
Parts Production
In the automotive industry, the production of parts is profoundly impacted by metal twister machines. These machines can create intricate vehicle components that meet specific safety and performance standards. A vital characteristic of parts production is the automatic precision achieved; this is crucial in a field where tolerances are minimal.
The unique advantage here is the consistency in production. Unlike traditional methods, machine-twisted components tend to offer higher uniformity, which leads to improved performance and safety. However, higher complexity of setups may require additional expertise to ensure optimal functionality.
Prototype Development
Prototype development in automotive manufacturing is another area where these machines excel. The ability to create custom parts quickly allows designers to test innovations and make necessary adjustments before mass production. One key characteristic is the rapid turnaround time from design to prototype.
This method of rapid prototyping is beneficial because it accelerates the design cycle, enabling faster adaptation to market needs. Yet, dependent on the specific designs, costs involved can be substantial, as specialized tools and settings may be required.
In summary, metal twister machines significantly enhance operational efficiencies across various industries. From agriculture to automotive, their applications prove valuable in improving existing processes and facilitating innovation.
Advantages of Using Metal Twister Machines
The use of metal twister machines brings numerous advantages to various industries. These benefits play a crucial role in enhancing production, ensuring quality, and maintaining flexibility in manufacturing processes. Below is a detailed analysis of the primary advantages, focusing on efficiency, precision, and adaptability.
Increased Efficiency
Reduced Production Time
Reduced production time is a significant advantage of using metal twister machines. These machines streamline the twisting process, allowing for higher output within a shorter timeframe. This key characteristic means that in sectors like agriculture or manufacturing, the ability to produce more in less time can lead directly to improved profitability. The unique feature of fast operation minimizes delays, making it a desirable choice for businesses looking to optimize their workflows.
However, while faster production is beneficial, it is important to consider the potential for decreased quality if not managed carefully. Optimal settings and monitoring are essential to leveraging this characteristic effectively.
Lower Labor Costs
Lower labor costs are another compelling reason for adopting metal twister machines. Automation reduces the reliance on manual labor, which can significantly cut down on wages and associated costs. This aspect helps companies maintain competitive pricing while also maximizing profits. The key characteristic here lies in the machine's ability to perform tasks that once required many workers.
Despite the advantages, businesses must consider the initial investment for these machines. The transition may require upfront costs, but the long-term savings typically justify this investment. An evaluation of overall operational expenses will aid in determining the financial viability of investing in metal twister machines.
Precision and Consistency
Quality Assurance
Quality assurance is paramount in any production environment, and metal twister machines excel in this regard. Their design ensures consistent results, which supports the overall goal of maintaining high product standards. This key characteristic is especially crucial for industries that demand precision, such as automotive manufacturing.
The unique feature of automation allows for very little variation from one piece to another. This reduces the likelihood of defects and assures customer satisfaction. However, companies must also invest in training operators to monitor the machines properly to reap the full benefits.
Minimized Waste
Minimized waste is another important advantage associated with metal twister machines. Efficient use of material reduces excess scraps, contributing to eco-friendliness and cost savings. This key characteristic is beneficial as it aligns with modern production goals towards sustainability. Using resources wisely can not only enhance the bottom line but also appeal to environmentally conscious consumers.
Nevertheless, businesses may need to find the right balance when implementing these machines. Over-automation can sometimes lead to unexpected issues in material handling that result in waste. A careful analysis of production workflows and monitoring practices will be key to maximizing this advantage.
Adaptability
Customizable Configurations
Customizable configurations of metal twister machines offer another layer of advantage. They can be tailored to fit specific production needs, which is essential for businesses that require unique solutions. This flexibility is a key characteristic as it allows for various twists and handling of different materials.
The unique feature of customization can lead to improved outcomes in specialized production scenarios. However, companies need to consider the complexity these customizations may bring. Operators must be well-trained to manage adjustments effectively, or risks of errors in production may increase.
Versatile Material Handling
Metall twister machines support versatile material handling, which is crucial for modern production lines. They can process a variety of metals, making them a beneficial choice for industries needing adaptability. This characteristic means companies can switch materials as needed without significant delays.
While the versatility is advantageous, companies must ensure they set proper parameters for each material type. Different metals may require distinct handling techniques, which adds complexity to operations. Proper planning and knowledge about material properties will help businesses to fully utilize this feature.
Challenges in Metal Twister Machine Operation
Understanding the challenges that come with metal twister machines is crucial for enhancing their efficiency and reliability in various applications. These issues, if not addressed, can hinder productivity and lead to unnecessary costs. Proper management of these challenges ensures that machines operate at their best, providing a competitive edge in the market. Professionals in agriculture and manufacturing will benefit from understanding these operational hurdles.
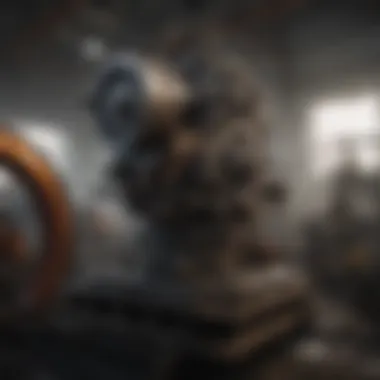
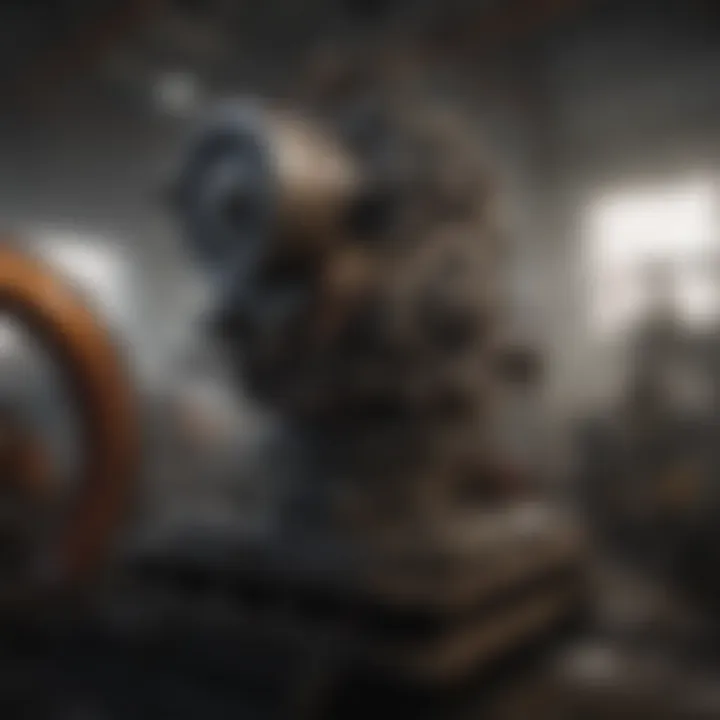
Maintenance Requirements
Scheduled Inspections
Scheduled inspections are a fundamental aspect of maintaining metal twister machines. Regular evaluation of the equipment contributes to detecting any issues before they escalate. This proactive approach helps in preserving the integrity of the machinery over time. The key characteristic of these inspections is their systematic nature, which ensures that no component is overlooked. They are beneficial because they enhance machine longevity. Without these inspections, unforeseen breakdowns may occur, leading to costly downtimes and repairs.
Scheduled inspections possess a unique feature, which is their ability to be tailored to specific models of machines. This customization allows operators to focus on the components that are most prone to wear and tear, therefore optimizing maintenance efforts. The upside is clear: reduced operational risks. However, one disadvantage could be the initial cost of establishing an inspection schedule. The investment in time and resources can be significant in the short term but pays off with efficiency gains.
Part Replacements
Part replacements are likewise a critical component in the ongoing operation of metal twister machines. This ensures that all machine parts function optimally, which is important for their overall performance. The key characteristic of part replacements is their direct impact on machine reliability. Using high-quality replacement parts is a popular choice because it directly correlates with performance. A machine with worn or damaged parts may underperform or become unsafe, which could lead to accidents.
One unique feature of part replacements is the possibility to upgrade components to newer technologies that enhance performance. This means that not only is the machine kept running, but it can also be improved. The advantages of this are significant, as it can lead to increased productivity. On the downside, the process requires careful planning and may incur additional costs.
Technical Complexity
Operator Training
Operator training is necessary for the effective operation of metal twister machines. A well-trained operator maximizes the potential of these machines and reduces the likelihood of errors during operation. The key characteristic of operator training is its focus on specific technical skills that are essential for safe and efficient machine handling. This makes operator training a beneficial choice for organizations seeking to maintain high productivity levels.
The unique feature of operator training lies in its adaptability to new technologies. As machines become smarter and more automated, ongoing training helps keep workers updated on relevant skills. This can greatly benefit the overall workplace environment. However, a disadvantage might be the time and cost invested in training programs, which can strain resources in the short run.
System Integration
Efficient system integration plays a vital role in the functionality of metal twister machines. As different systems come together, they enhance the machine’s overall performance. The key characteristic of this integration is that it enables seamless communication between components. This cohesiveness improves operational efficiency and minimizes the risk of failures or delays. System integration is a beneficial choice for any operation seeking to optimize machine performance by ensuring all parts are in sync.
A unique aspect of system integration is its ability to incorporate real-time data monitoring, allowing operators to make informed decisions instantly. The advantages of this setup include enhanced operational flexibility and quicker responses to machine performance issues. However, the complexity of integrating various systems can be challenging, requiring significant planning and resources to execute properly.
Understanding these challenges is essential for optimizing efficiency and enhancing reliability in metal twister machine operations. By addressing maintenance and technical complexities, industries can leverage the full potential of these machines.
Future Trends in Metal Twister Machines
As industries evolve, the demand for efficient, precise, and adaptable machinery increases. Metal twister machines are no exception to this trend. Understanding the future of these machines involves examining developments in technological advances and sustainability practices. These elements not only shape the machines themselves but also their applications across various sectors. Continuous innovations aim at increasing productivity while addressing environmental concerns which make this subject crucial for professionals in metalworking fields.
Technological Advancements
Technological advancements play a vital role in the evolution of metal twister machines.
Automation Integration
Automation integration in metal twister machines represents a significant leap in manufacturing capabilities. The main characteristic of automation is its ability to streamline processes, reducing the reliance on manual labor. This is a popular choice as it cuts down on time required for tasks and minimizes human error. A unique feature of automation integration includes the capability to operate machines remotely, allowing for increased flexibility in monitoring and adjustments. While the advantages are substantial, such as enhanced precision and reduced operational costs, a potential disadvantage is the high initial investment and the need for skilled personnel to manage automated systems.
Smart Machinery
Smart machinery injects intelligence into the operation of metal twister machines. This characteristic focuses on interconnected systems that enable real-time data processing and feedback. The benefit of smart machinery is its ability to adapt to varying conditions during operation. For instance, the machine can automatically adjust its twisting parameters based on the material type or thickness. This adaptability results in improved consistency and quality in production. However, smart machinery can come with complexities in setup and integration, which may require protuning to ensure effective operation in existing workflows.
Sustainability Practices
Sustainability is becoming essential across all industries, and metalworking is no exception.
Energy Efficiency
Energy efficiency in metal twister machines refers largely to how effectively equipment uses energy without compromising output. This aspect is important due to rising energy costs and environmental regulations. An energly efficient machine helps in lowering operational costs while minimizing the carbon footprint. A unique feature here is the use of variable frequency drives, which adjust motor speeds based on demand. The primary disadvantage can be the upfront costs associated with acquiring modern, energy-efficient machines.
Recyclable Materials
The use of recyclable materials in manufacturing metal twister machines is gaining traction. This trend emphasizes the importance of using materials that can be repurposed or recycled after their lifecycle is completed. Recyclable materials are favorable because they contribute to sustainability goals and can often reduce overall costs in the long run. For instance, certain metal alloys can be reused in the production process, reducing waste. A challenge can be the sourcing of quality recyclable materials that meet the stringent requirements of performance and durability required in machine production.
As the metalworking sector advances, the incorporation of both technological and sustainable practices will redefine the capabilities and roles of metal twister machines.
Epilogue
The topic of metal twister machines presents significant relevance in today’s rapidly evolving industrial landscape. These machines stand at the forefront of modern metalworking, embodying not merely a means of twisting metal but a synthesis of innovation and practicality. As industries strive for efficiency and precision, understanding the implications of metal twister machines becomes critical.
Summary of Key Insights
In this article, we have examined the intricate workings and applications of metal twister machines across various fields. Key highlights include:
- Core Mechanical Components: Essential parts such as the frame, twisting mechanism, and control systems define the functionality and performance of these machines.
- Industry Applications: Their use in agriculture, manufacturing, and automotive sectors illustrates their versatile role in enhancing productivity.
- Benefits Realized: Increased efficiency, precision, and adaptability are among the many advantages, resulting in cost savings and reduced waste.
Through these insights, it is clear that metal twister machines are not just tools; they are integral components that can transform operations and drive growth.
The Importance of Continuous Development
In a world where technology evolves consistently, the importance of continuous development in metal twister machines cannot be overstated. Staying ahead involves:
- Adapting to Innovations: Incorporating automation and smart features enhances functionality and user experience.
- Sustainability Focus: With a growing emphasis on energy efficiency and use of recyclable materials, future developments must align with these values.
Therefore, focusing on these continuous advancements ensures that industries utilizing metal twister machines can maintain their competitive edge, while also contributing to sustainable practices within the broader metalworking ecosystem.
The journey of understanding and evolving metal twister machines is far from complete. It is an ever-changing landscape that invites continuous exploration and improvement.