Efficiently Sourcing Case Construction Equipment Parts Online
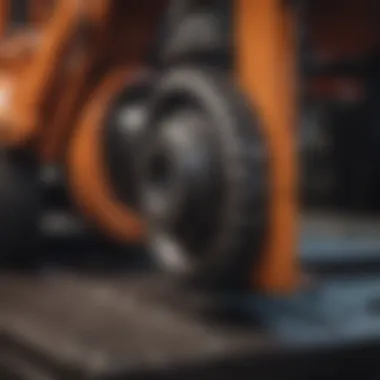
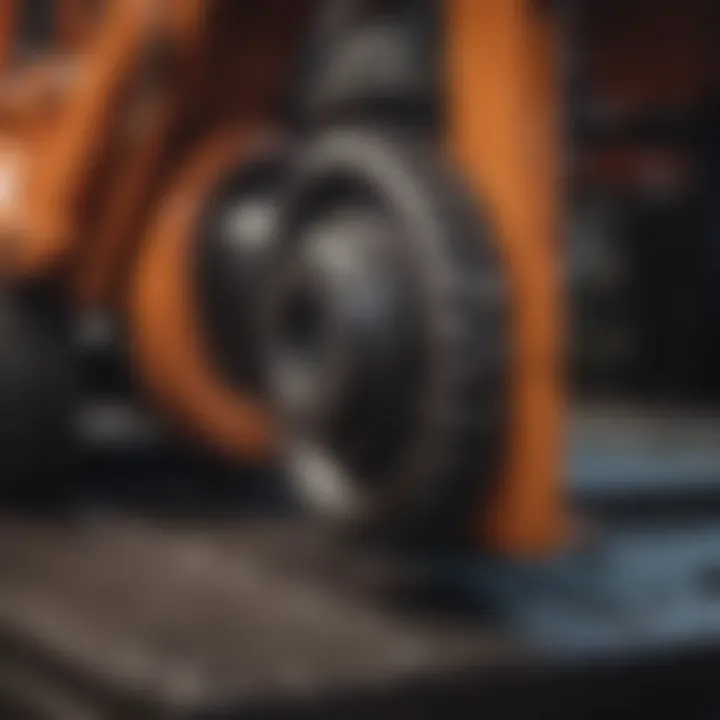
Intro
The world of construction and agriculture relies heavily on equipment performance. Case construction equipment plays a critical role in ensuring job efficiency. Understanding how to procure and maintain parts for this equipment is imperative for long-term success. This article will provide insights into effective strategies for sourcing Case construction equipment parts online, emphasizing supplier reliability and optimal maintenance.
In an era where technology influences all aspects of our lives, buying equipment parts online is becoming increasingly popular. The digital marketplace is vast, presenting both opportunities and challenges. As professionals in the construction and agricultural sectors engage with these online platforms, it is crucial to navigate them wisely. We will look at terminology, current trends, and practical applications related to procurement and maintenance of parts for Case construction equipment.
Key Concepts and Terminology
Definition of Terms
Before delving into procurement strategies, it is necessary to establish some key terms.
- Procurement refers to the process of acquiring goods or services, in this case, equipment parts.
- Maintenance involves routine checks and repairs to ensure equipment operates efficiently.
- Parts denote the individual components necessary for the functionality of the machinery.
Overview of Relevant Practices
When procuring equipment parts online, several practices can enhance decision-making. Professionals must understand their specific requirements regarding the equipment type. Knowing the model number and part specifications streamlines the purchasing process. Additionally, contact with suppliers through platforms like Reddit or Facebook can provide further insights into product availability and performance.
Current Trends and Innovations
Latest Research and Developments
The field of construction equipment is experiencing significant innovations. Current research emphasizes the shift towards online marketplaces for procurement. Online platforms enable users to access a variety of suppliers simultaneously, often leading to cost savings. Moreover, studies indicate that online sourcing can reduce lead times for critical parts, thereby decreasing downtime on job sites.
Emerging Technologies and Tools
The rise of mobile applications for tracking parts and inventory is transforming the landscape. Tools like Case's official app provide users with inventory checks, part ordering, and service scheduling. These technological advances simplify maintenance. Moreover, utilizing chatbots on supplier websites can enhance customer service, offering instant answers to common questions.
Practical Applications
Step-by-Step Guides
To ensure smooth procurement and maintenance, consider the following steps:
- Identify the specific parts needed, consulting equipment manuals for accuracy:
- Research and compare multiple online suppliers. Focus on their reputation and customer reviews.
- Make sure the suppliers offer a return policy in case of incorrect parts.
- Follow up with suppliers for shipping updates.
- Ensure that the necessary maintenance procedures are in place, including the schedule for inspections.
Troubleshooting Common Issues
When sourcing parts online, one can face various challenges. Here are some common issues and how to overcome them:
- Incorrect Parts: Always double-check part numbers and descriptions before placing an order.
- Delays in Shipping: Communicate directly with the supplier to inquire about shipping timelines, especially for urgent parts.
- Quality Concerns: Look for detailed product descriptions and customer reviews to verify the quality of parts.
"Having reliable suppliers can dramatically improve procurement efficiency and equipment functionality."
Foreword to Case Construction Equipment
In the construction and agricultural sectors, Case construction equipment plays a crucial role. This equipment includes various machines and tools essential for completing tasks effectively and efficiently. Understanding the functionality and requirements of these machines is important for anyone involved in the industries. Having reliable equipment ensures that projects are done on time and within budget, which is often paramount in these fields.
The procurement of parts for Case equipment is a vital factor in maintaining and optimizing performance. Without the right parts, the equipment cannot operate as intended, leading to potential delays and increased overhead costs. By exploring the avenues for sourcing parts online, businesses can gain access to a broader range of options and suppliers, enhancing their ability to keep operational downtime to a minimum.
Additionally, this section lays the foundation for comprehending how procurement processes impact overall equipment maintenance. Knowledge of the equipment's needs, as well as the market landscape for parts, is essential in cultivating longevity and reliability for machines that serve critical functions in construction and agriculture.
Overview of Case Construction Equipment
Case construction equipment comprises various machinery types like excavators, bulldozers, backhoe loaders, and forklifts. Each machine serves a unique role in the field, from performing heavy lifting to site preparation. Case has established a reputation for producing durable and efficient machinery designed to meet the demanding requirements of construction sites and farms.
For operations to run smoothly, equipment must be properly maintained and supplied with quality parts. Understanding the function and specific parts that make up each equipment type aids in crafting a well-rounded maintenance strategy. This knowledge allows users to identify when specific parts may need replacement, ensuring machinery performance remains at optimal levels throughout its lifecycle.
Importance in Agriculture and Construction
The significance of Case construction equipment within agriculture and construction cannot be overstated. In agriculture, these machines assist in tasks like land preparation, planting, and harvest, thus enhancing productivity and yield. Farmers relying on equipment like the Case IH tractor can perform operations more efficiently while saving time and labor costs.
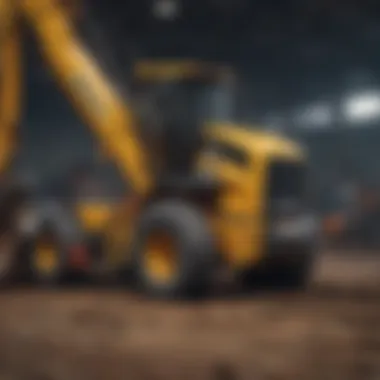
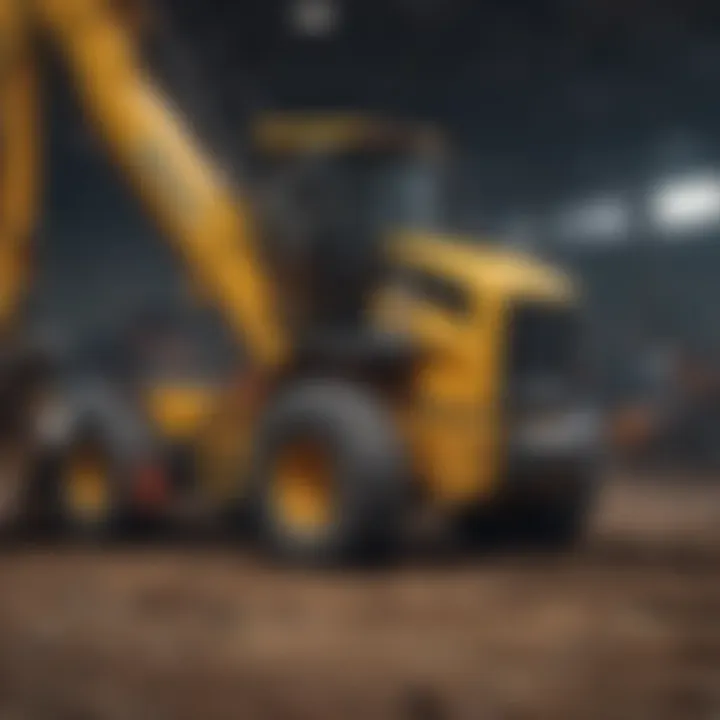
In construction, the ability to quickly complete tasks significantly impacts project timelines and budgets. Equipment from Case, such as its dozers or excavators, can handle heavy loads, making it indispensable for site development and material management. The productivity of crews is often linked to the equipment at their disposal; thus, using reliable and effective Case machinery becomes a sound investment. Overall, procurement and maintenance strategies for these machines play an integral role in both sectors' operational success.
Understanding Equipment Parts
Understanding equipment parts is fundamental to both the efficient operation of Case construction machinery and informed procurement practices. An in-depth knowledge of these components allows professionals in agriculture and construction to make strategic decisions when sourcing replacements or upgrades online. Knowing the different types of parts, their functions, and potential issues ensures that equipment operates at optimal performance, which directly correlates with productivity and cost-efficiency.
Types of Parts for Case Equipment
Case construction equipment includes a wide range of machines like excavators, backhoes, and skid steers. Each machine consists of various parts that can be categorized into several types. Here are some of the main categories:
- Engine Components: Vital for the power and performance of the equipment, including pistons, valves, and fuel injectors.
- Hydraulic Parts: Including pumps, cylinders, and hoses, these parts are crucial for the functionality of equipment capable of lifting and moving heavy loads.
- Transmission Parts: These components ensure the effective transfer of power from the engine to the wheels or tracks. They include gears, clutches, and drive shafts.
- Electrical Systems: Essential for modern equipment, these parts include batteries, starters, and wiring harnesses.
- Structural Components: Frames, chassis, and bodies provide the physical foundation for all machinery. They must be durable to withstand rigorous work conditions.
Understanding these different types aids in identifying the exact part needed during online procurement, reducing the chances of mismatches.
Common Issues with Construction Equipment Parts
Common issues with construction equipment parts often arise from both usage and environmental factors. Awareness of these issues can significantly enhance maintenance efforts and extend the life of the machinery. Some challenges include:
- Wear and Tear: Regular usage leads to inevitable degradation, particularly in high-friction parts like hydraulic cylinders and bearings.
- Corrosion: Exposure to harsh environmental conditions can cause electrical components to rust, leading to electrical failures.
- Improper Installation: If a part is not installed correctly, it can cause a cascade of issues, including machinery failure or safety hazards.
- Counterfeit Parts: The prevalence of counterfeit components can erode machine performance and pose safety risks. It is vital to purchase equipment parts from reputable suppliers.
"Identifying common problems and knowing which parts to prioritize can help ensure robust performance and potentially save significant costs in repairs."
Being cognizant of these issues allows agricultural farmers and construction professionals to adapt their maintenance strategies, reducing downtime and ensuring that machines operate at peak performance. This understanding also informs smarter choices when sourcing online, as it highlights the importance of quality and reliability in parts procurement.
The Rise of Online Procurement
The shift towards online procurement in the construction equipment industry is significant. For Case construction equipment, accessing parts online has transformed how businesses operate. This change reflects broader trends impacting many sectors, including agriculture. As services become more digital, suppliers and customers must adapt.
Trends in Online Parts Sourcing
Various trends define online parts sourcing. One notable trend is the increased use of digital platforms for purchasing. Sites like eBay and Amazon have expanded their offerings, focusing on construction equipment. Another trend involves specialized marketplaces dedicated solely to Case equipment parts. These platforms allow for detailed searches, enabling buyers to find specific components.
Additionally, social media plays a role in sourcing parts. Groups on Facebook or forums on Reddit facilitate discussions among professionals. They share experiences about quality suppliers and potential pitfalls in purchasing. This community aspect strengthens the network for sourcing parts.
Benefits of Online Purchasing
The benefits of online purchasing for Case construction equipment parts are clear. Firstly, convenience is a major factor. Buyers can browse inventory from various suppliers without leaving their location. This accessibility saves time, which is critical in the fast-paced construction environment.
Secondly, the range of options is broader. Online marketplaces offer diverse parts, including hard-to-find ones. This selection proves beneficial, especially when sourcing for older equipment models.
Lastly, pricing transparency is another advantage. Online procurement often allows for easier comparisons of prices across different platforms. Customers can quickly identify competitive offers, ensuring they get the best value.
Online procurement is not just a trend; it is becoming the standard in sourcing parts for Case construction equipment.
In summary, the rise of online procurement offers numerous advantages for the construction and agricultural sectors. With ongoing technological advancements, these benefits are likely to expand. Being aware of current trends and leveraging online resources can enhance operational efficiency in sourcing spare parts.
Navigating Online Marketplaces
Navigating the vast online marketplaces for Case construction equipment parts is essential for effective procurement. The digital landscape offers numerous platforms, ranging from established e-commerce sites to specialized suppliers. Understanding the features and offerings of these marketplaces can enhance the procurement process and ensure that equipment maintains optimal performance.
With the increase in online purchasing, awareness of reliable sources is critical. This includes recognizing solid vendors with proven track records. A supplier’s reputation often reflects their reliability. Consequently, it's wise to seek out businesses that focus specifically on Case equipment to find the best products and services.
The convenience of online marketplaces means buyers can compare prices and reviews quickly. However, the sheer volume of options can lead to indecision. It's imperative to remain focused on specific needs and objectives when researching. Establish and maintain a clear criteria for suppliers and parts, making the evaluation process systematic.
"Efficiency in sourcing can yield considerable time and cost savings, provided that one navigates the market with knowledge and discernment."
Identifying Reliable Suppliers
Selecting trustworthy suppliers requires careful analysis. Factors such as industry certifications, customer reviews, and return policies are important. Here’s a brief overview of how to identify the right suppliers:
- Research and Background Check: Look into the supplier's history and their experience with Case products. Supplier longevity in the market can be an indicator of their reliability.
- Customer Testimonials: Investigating what previous customers say can provide insights into the supplier's service and product quality.
- Contact Information: Verify that the supplier provides clear contact information. A professional approach often reflects their commitment to customer support.
Evaluating Quality and Authenticity of Parts
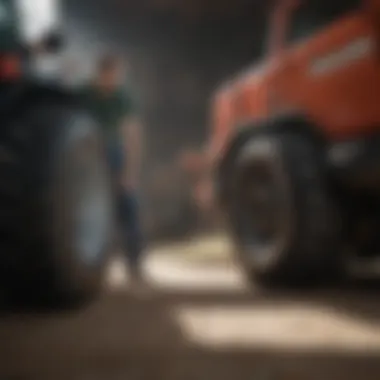
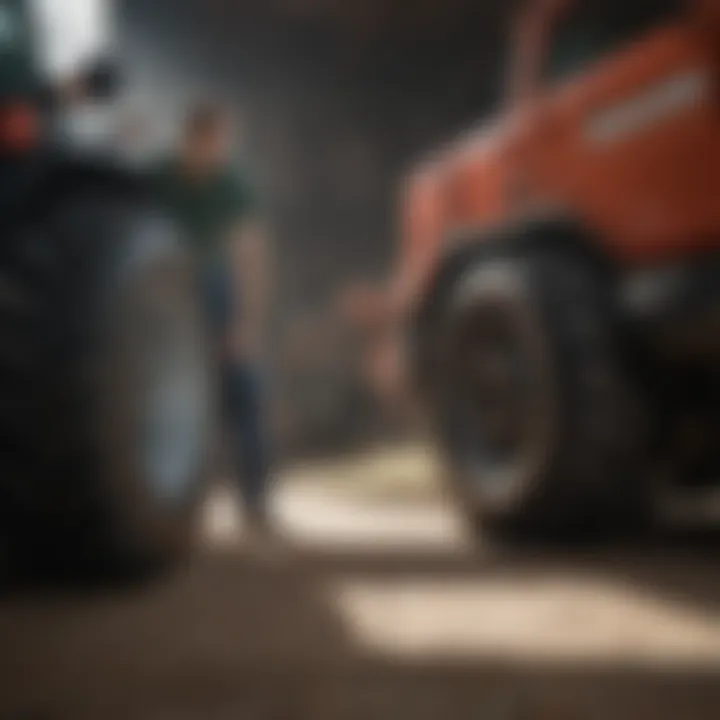
Ensuring that parts are both high-quality and authentic is crucial. Counterfeit products can jeopardize the functionality of Case equipment. The following steps should be considered:
- OEM vs Aftermarket Parts: Understand the difference between Original Equipment Manufacturer (OEM) parts and aftermarket parts. OEM parts are designed specifically for Case equipment, ensuring compatibility and performance.
- Visual Inspections: Reputable suppliers usually provide clear images and descriptions. Examine these closely for details that ensure authenticity.
- Request Documentation: Ask sellers for proof of authenticity, such as certifications or warranties, before making a purchase.
Understanding Pricing Structures
Pricing is a vital factor in procurement decisions. Familiarity with pricing structures helps make informed decisions. Consider the following:
- Comparative Shopping: Utilize various platforms to compare prices of the same parts. Tools that highlight price discrepancies can save considerable costs.
- Additional Costs: Be aware of shipping and handling fees. These can significantly alter the final cost of parts, so always factor them into the budget.
- Bulk Discounts: Some suppliers offer discounts for bulk purchases. If managing multiple pieces of equipment, this can be a strong cost-saving strategy.
Best Practices for Online Procurement
Procurement of Case construction equipment parts online has become essential due to the increasing digitization of the marketplace. Understanding best practices in this area can save time and reduce costs.
Effective online procurement involves conscious decisions throughout the purchasing process, which enhances efficiency and minimizes potential setbacks. Here are several key elements for achieving optimal results:
- Thorough Research: Understand the specific needs of your equipment. Knowing the exact parts required for maintenance can help avoid unnecessary purchases.
- Supplier Verification: Not all online suppliers are reliable. Look for suppliers with clear credentials, positive reviews, and comprehensive return policies.
- Comparison Shopping: Utilize multiple platforms to compare prices and availability. This ensures that you are getting the best deal for the parts you need.
Creating a Parts Inventory List
A parts inventory list is crucial for managing your equipment needs efficiently. A comprehensive list helps track what items are in stock, what needs replacing, and what can be ordered in bulk. Here’s how to create one:
- Identify Equipment: List all your Case construction equipment.
- Catalog Required Parts: For each piece of equipment, write down all necessary parts. Be specific about part numbers to avoid confusion.
- Update Regularly: Keep the inventory updated after each use or replacement. This will help you know when to reorder supplies.
"Regular audits of your parts inventory can prevent downtime and costly delays in operations."
Leveraging Reviews and Testimonials
Feedback from other users offers invaluable insight into online suppliers. Reviews can reveal the quality of parts and the reliability of the supplier. When assessing reviews, consider the following:
- Volume of Feedback: A supplier with numerous reviews is generally more trustworthy.
- Content of Reviews: Look for details about delivery times, product durability, and customer service experiences.
- Social Media Insights: Platforms like Facebook can provide a view into customer satisfaction that may not be present on traditional review sites.
Securing Payment and Transaction Safety
The safety of your financial transactions is paramount when purchasing equipment parts online. Here are important steps to ensure secure payments:
- Use Secure Payment Methods: Opt for credit cards or recognized payment platforms like PayPal, which often provide added protection against fraud.
- Check for HTTPS: Always ensure that the website URL begins with "https://" to confirm a secure connection.
- Review Privacy Policies: Understand how your data will be used by reviewing the supplier's privacy policy.
Maintaining strict online procurement practices can significantly improve your experience, ensuring you acquire the right parts while safeguarding your financial transactions.
Implementing Maintenance Strategies
Efficient procurement of Case construction equipment parts is only part of the equation. Implementing robust maintenance strategies is critical for maximizing the longevity and performance of your equipment. Maintenance ensures that your machinery operates at peak efficiency, reduces downtime, and ultimately saves costs. It also addresses safety concerns, making it essential for those in the agriculture and construction sectors.
Routine Maintenance for Equipment Longevity
Routine maintenance is the foundation that supports equipment longevity. Scheduled inspections and interventions help catch small issues before they escalate. This can include regular checks on hydraulic systems, engine oil levels, and tire conditions. The frequency of maintenance will often depend on how often the equipment is used, but a good rule of thumb is to schedule checks based on operating hours.
- Benefits of Routine Maintenance:
- Prevents unexpected breakdowns, which can be costly.
- Enhances equipment efficiency, leading to better fuel economy.
- Reduces the need for expensive repairs over time.
A simple checklist can go a long way. For instance, before each job, check that all fluids are topped up and that there are no visible leaks. Additionally, listen for unusual noises when machinery is running. Addressing minor concerns proactively can preserve the integrity of the machinery and extend its lifespan.
Utilization of OEM Parts vs Aftermarket Parts
When it comes to replacement parts, you face the choice between Original Equipment Manufacturer (OEM) parts and aftermarket alternatives. OEM parts are made by the manufacturer and designed specifically for your machinery. They usually come with a warranty and guarantee the same quality as the original parts that came with your equipment.
Aftermarket parts, on the other hand, can be less expensive and more readily available. However, they vary significantly in quality. Some aftermarket parts can match OEM standards, while others may not function as effectively or could even void warranties.
- Considerations for Choosing Parts:
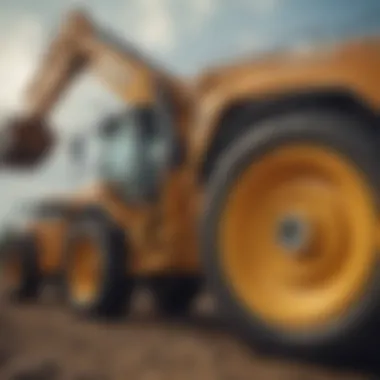
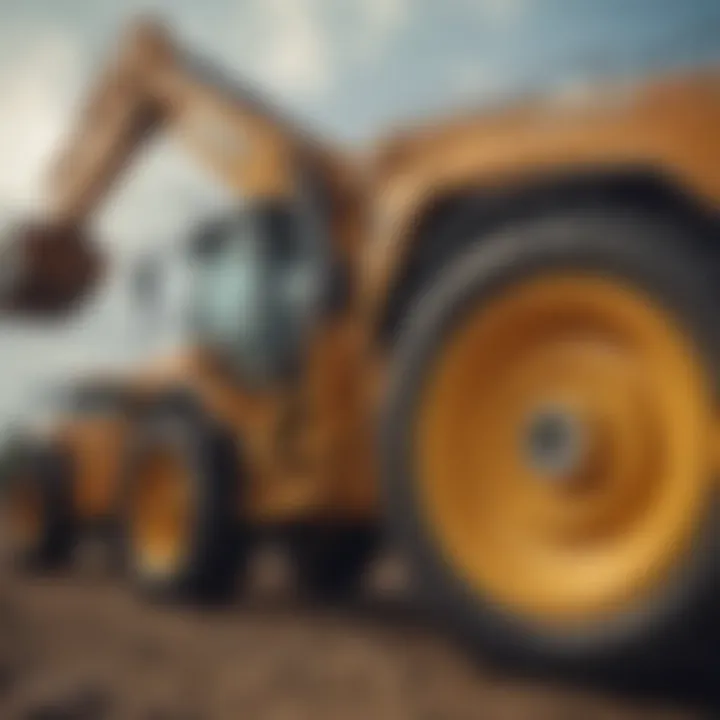
- Quality Assurance: Always verify the reputation of the supplier or manufacturer.
- Cost Efficiency: While aftermarket parts may save you money upfront, consider the potential costs due to reduced performance or extra maintenance down line.
- Warranty and Support: OEM parts often come with better support and guarantees than most aftermarket options.
In summary, selecting between OEM and aftermarket parts involves weighing immediate costs against the long-term advantages. It’s often a good strategy to use OEM parts for critical components to ensure safety and reliability while reserving aftermarket options for non-essential items.
"Investing time and resources in maintaining your equipment will pay dividends in the form of reliability and efficiency."
By adopting thoughtful maintenance strategies and making informed choices about parts, you can significantly enhance the life and performance of your Case construction equipment, ultimately leading to enhanced productivity and reduced operational costs.
Case Studies in Online Sourcing
Exploring real-world case studies is vital when discussing online sourcing of Case construction equipment parts. These narratives provide insights into how businesses navigate the complexities of online procurement. Understanding both successful examples and the pitfalls encountered can help inform best practices for others in the field.
Successful Online Procurement Experiences
In various instances, businesses have successfully utilized online platforms to procure Case equipment parts. For example, a contractor based in Iowa reported a substantial decrease in lead times by sourcing parts through specialized online marketplaces rather than traditional suppliers. This shift allowed them access to a wider range of parts, all while guaranteeing quicker deliveries.
Some key takeaways from their experience include:
- Efficiency Gains: The contractor noted that their previous reliance on local suppliers often delayed operations. Online sourcing allowed them to receive parts faster and maintain productivity on projects.
- Diverse Options: Online platforms often have multiple suppliers, expanding choices for parts which can lead to competitive pricing. This contractor leveraged those options effectively.
- Simplified Ordering Process: User-friendly interfaces on online marketplaces streamlined the ordering process, reducing administrative burdens.
Common Pitfalls and Lessons Learned
Despite the successes, there are also cautionary tales. One firm that ventured into online procurement faced challenges due to inadequate research on suppliers. They experienced subpar product quality and unanticipated delivery delays.
From this experience, several important lessons emerged:
- Supplier Vetting is Crucial: Many suppliers offer similar products, but not all meet quality standards. Take time to read reviews and check the authenticity of parts.
- Comprehensive Inventories: Without a clear inventory, companies can overlook specific part needs, leading to incomplete orders. Hence, an organized parts inventory is fundamental.
- Price vs. Quality: The allure of lower prices can be misleading. Always prioritize quality over cost to avoid future issues.
"Learning from others' experiences can prevent costly mistakes in procurement."
By analyzing these case studies, it becomes evident that a mix of strategic planning, diligent research, and an understanding of the online environment can make the sourcing of Case construction equipment parts more successful and effective.
Future Trends in Equipment Parts Procurement
Understanding the future trends in equipment parts procurement is crucial for professionals in the construction and agricultural sectors. As industries evolve, new methods and technologies emerge, shaping how parts are procured, maintained, and utilized. This section delves into significant developments, with a focus on emerging technologies and sustainability considerations, which are essential in enhancing efficiency and reducing costs in the procurement process.
Emerging Technologies in Parts Sourcing
Technological advancements are reshaping procurement practices in remarkable ways. With the advent of artificial intelligence and machine learning, businesses can now analyze vast amounts of data to predict needs and streamline purchasing processes.
- Automated Ordering Systems: These systems can predict when parts are needed based on usage patterns. This minimizes downtime and ensures equipment is operational when necessary.
- Blockchain Technology: By providing transparent transaction records, blockchain enhances trust between suppliers and buyers. It allows for better tracking of parts, ensuring authenticity and quality.
- Augmented Reality (AR): AR is making training and parts identification more accessible. Workers can use AR devices to visualize equipment internals and locate parts quickly, reducing miscommunication and errors.
The integration of these technologies ensures faster procurement and delivery processes, leading to improved operational performance and cost savings.
Sustainability Considerations
Sustainability is becoming increasingly relevant in parts procurement. As companies become more conscious of their environmental impact, they are implementing strategies to source parts sustainably. This not only benefits the environment but can also enhance company reputation and customer loyalty.
- Recycling and Upcycling: Many businesses are exploring ways to recycle parts or repurpose them for other equipment. This not only reduces waste but can also lower costs of procurement.
- Eco-friendly Materials: Sourcing parts made from sustainable materials can help companies reduce their carbon footprints. It aligns with consumer expectations for responsible business practices.
- Energy-efficient Equipment: Investing in energy-efficient machines can lead to long-term savings. Using less fuel not only cuts costs but also lessens pollution.
"Companies that integrate sustainability into their operations can benefit from improved public perception and customer loyalty."
Understanding these trends allows professionals to make informed decisions that align with both operational goals and environmental responsibility.
Epilogue
Recap of Key Insights
Several insights come to the forefront when considering online procurement. Key points include:
- The identification of reliable suppliers is crucial; not all online sellers provide high-quality parts.
- Regular maintenance using appropriate parts prolongs the life of your equipment. Choices between OEM and aftermarket parts need careful evaluation.
- Awareness of the pricing structures helps in making informed decisions that can lead to significant savings.
- Incorporating sustainability into procurement strategies is increasingly becoming essential in modern practices.
"Effective procurement of construction equipment parts online is not just a trend; it is a necessary component of operational efficiency in the field."
Final Thoughts on Online Parts Procurement
The future of parts procurement for Case construction equipment lies increasingly in the online marketplace. The ongoing evolution of technology ensures that the tools and resources for sourcing parts are expanding. As online platforms improve, professionals must stay vigilant and adaptable. They must consider quality, price, and supplier reliability when making purchasing decisions.
Ultimately, maintaining Case equipment properly with the right parts is vital for operational success. Optimizing procurement processes through a keen understanding of online resources will not only enhance equipment performance but also ensure the sustainability of operations in both agriculture and construction. Taking calculated steps today will ensure better outcomes tomorrow.