Screens for Rotary Grain Cleaners: A Detailed Guide
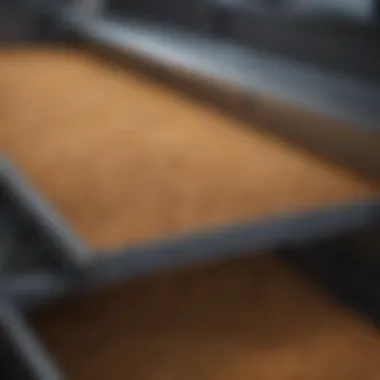
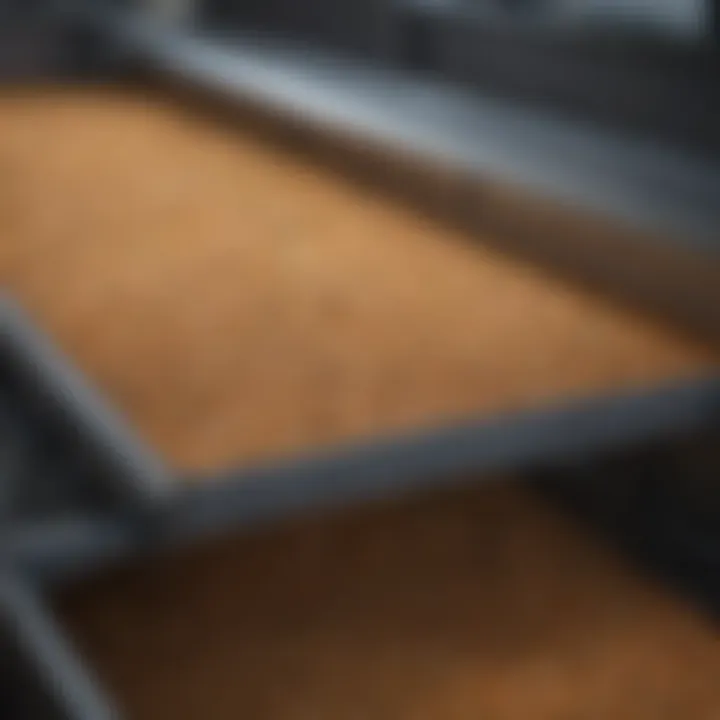
Intro
When it comes to grain processing, screens for rotary grain cleaners play a vital role in ensuring quality and efficiency. These screens serve as the first line of defense against impurities and contaminants that can impair the final product. Understanding how these screens work, their various types, and the materials used can be a game changer for farmers and agriculture enthusiasts alike.
Effectively, the choice of screen can influence not just the cleanliness of the grain but also its market value. The right screen makes sure that valuable seeds get through while unwanted debris gets stuck. In this article, we’ll explore the ins and outs of rotary grain cleaner screens, focusing on the essentials that every agricultural professional should consider.
Key Concepts and Terminology
Before diving into specifics, it’s crucial to grasp some key terminology associated with rotary grain cleaners and their screens. Here’s a concise breakdown:
Definition of Terms
- Screening: The process of separating grain based on size and weight using screens.
- Mesh Size: The size of openings in the screen, which determines what can pass through and what can’t. Typical mesh sizes vary greatly depending on the grain and debris types.
- Contaminants: Unwanted particles that aren’t part of the grain. They could be dirt, unknown seeds, or even chemical residues.
Overview of Relevant Practices
In the world of rotary grain cleaning, a few practices stand out:
- Routine Inspection: Regular checks on screens to ensure they’re functioning optimally prevents costly downtimes.
- Material Selection: Different screen materials offer varied life spans and efficiencies. For example, stainless steel might be chosen for its robustness.
- Sizing Adjustments: Adjusting the mesh size based on the type of grain enables better separation, enhancing final quality.
Current Trends and Innovations
With technology advancing at a breakneck pace, it's worth noting what’s hot in the area of rotary grain cleaning.
Latest Research and Developments
Recent studies emphasize the use of composite materials in screen construction, which can lead to improvements in durability while maintaining light weight. These findings indicate longer replacement cycles and reduced costs for farmers.
Emerging Technologies and Tools
- Smart Sensors: Some new systems incorporate sensors that monitor debris removal in real-time, allowing farmers to adjust settings on the fly.
- Automated Cleaning Systems: Featuring screens that can self-clean, these innovations promise to reduce labor and maintenance.
Practical Applications
Understanding screens is one thing, but knowing how to apply this knowledge in real-world scenarios is where it gets interesting.
Step-by-Step Guides
To maximize the effectiveness of rotary grain cleaners, consider this general procedure:
- Select the appropriate screen for the grain type being processed.
- Install the screen using proper tools to avoid mishandling.
- Run a test batch to ensure the screen is properly adjusting to the product.
- Conduct regular maintenance—check for tears or wear, and replace screens as needed.
Troubleshooting Common Issues
- Screen Blockage: This can happen if the mesh size is too small for the debris size.
- Wear and Tear: If screens are frequently damaged, it may be worth evaluating the material used.
Effective screen selection and maintenance can significantly improve overall grain quality and profitability in the long run.
By taking these insights on board, agricultural professionals can navigate their challenges more smoothly and focus on their core work—producing high-quality grain. Understanding the performance metrics and adapting to technological changes enables farmers to stay ahead in a competitive market.
Prolusion to Rotary Grain Cleaning
Grain cleaning is more than just a routine task in the agricultural field; it's a vital process that can significantly impact the quality and marketability of the end product. The backdrop of grain cleaning is steeped in tradition, where farmers persistently seek ways to enhance their harvest. At the heart of these efforts lie rotary grain cleaners, devices designed to ensure that grain is free from dust, chaff, and other impurities. The necessity of grain cleaning cannot be overstated, as even a minute level of contamination can lead to substantial economic repercussions and customer dissatisfaction.
The Importance of Grain Cleaning
Clean grain is paramount for various reasons. First and foremost, improving grain quality is a key concern for anyone involved in the agricultural sector. Unclean grain often contains foreign materials, which can result in lower sales prices or even rejection from buyers. The market often favors premium quality, and anything less can tarnish a farmer’s reputation. Furthermore, grain cleaning helps in maintaining the nutritional value, prolonging shelf life, and minimizing spoilage during storage. This is particularly vital for regions that face storage challenges due to climate conditions.
When you take a step back and consider the consequences of neglecting grain cleaning, the picture becomes even clearer. It might seem like a minor issue, but clogs in grain handling systems can lead to larger operational headaches and costly delays. Therefore, investing in effective grain cleaning systems not only improves product quality but safeguards operational efficiency.
Overview of Rotary Grain Cleaners
Rotary grain cleaners are robust machines that embrace innovation in the quest for clean grain. They operate on simple principles but utilize advanced technologies to achieve high efficiency. The mechanism is built around rotating screens that sort and separate grain from debris. Such a system ensures that different grain sizes are treated appropriately, allowing for a tailored cleaning process that can adapt to varied grain types.
The versatility of rotary grain cleaners is another feather in their cap. These machines can handle not just grains like wheat, corn, or rice but also various other seeds, making them indispensable for farmers dealing with mixed crops. Moreover, the design of rotary cleaners typically allows for easy adjustments to accommodate different products, which enables farmers to switch from one grain type to another without needing extensive reconfiguration.
"Quality is never an accident. It is always the result of intelligent effort."
With this foundational understanding, the upcoming sections will explore the specific elements of screens used in rotary grain cleaners, dissecting their functionality and significance in preserving grain quality.
Understanding Screens in Grain Cleaners
Understanding screens in rotary grain cleaners is pivotal for achieving optimal grain quality. Screens play an instrumental role in the cleaning process by separating unwanted materials from the desired grain. A well-chosen screen not only enhances cleaning efficiency but also reduces operational costs. With the diverse types of screens available, being aware of their functionality and the unique characteristics can significantly influence how a grain cleaning operation performs.
Functionality of Screening
Screens in rotary grain cleaners work on the principle of size and shape separation. As grain passes through the screen, unwanted substances, like chaff, dust, and broken kernels, are filtered out. The fundamental benefit here is achieving higher purity in the grain. This filtration process is not only about removing debris but also about preserving the quality and value of the final product.
Well-functioning screens contribute directly to the operation's overall throughput and productivity as they ensure the smooth flow of clean grain.
Types of Screens Available
Choosing the right type of screen can make a world of difference in grain cleaning efficiency. There are various screens available, each with distinct characteristics tailored for specific uses:
Perforated Screens
Perforated screens are sheets of material, usually metal, with holes drilled into them. These holes can be custom-sized to target specific contaminants while allowing larger grains to pass through.
One key characteristic of perforated screens is their adaptability; they can be crafted to fit nearly any rotary cleaner. Their popularity comes from their ability to achieve deep cleansing without excessive interference in the grain’s flow. However, one downside is that over time, wear and tear can diminish their efficacy, requiring regular monitoring.
Woven Wire Screens
When it comes to strength and durability, woven wire screens shine. Made from interwoven metal wires, these screens offer a robust option for heavy-duty applications. The primary advantage of woven wire screens lies in their ability to withstand higher temperatures and abrasive materials.
A unique feature of these screens is their precise mesh openings, which can be modified to fit specific cleaning objectives. However, they are often less flexible in terms of sizing compared to their perforated counterparts; choosing the wrong mesh size can lead to subpar performance or clogging issues.
Synthetic Screens
These screens are often made from polymer materials, offering lightweight yet effective options for grain cleaning. A major benefit of synthetic screens is their resistance to corrosion and chemical degradation, which can be a serious concern in agricultural settings.
Their unique feature is that many synthetic screens are designed to minimize friction, promoting smoother grain flow and reducing wear on machinery. On the flip side, synthetic screens may not always have the same level of durability as metal options, leading some to ponder their longevity in harsh operating conditions.
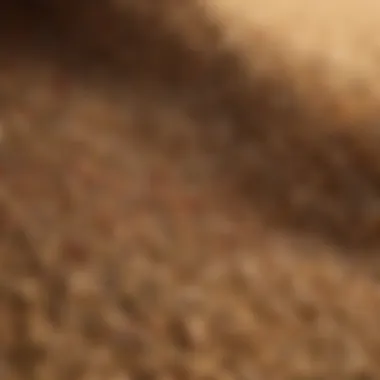
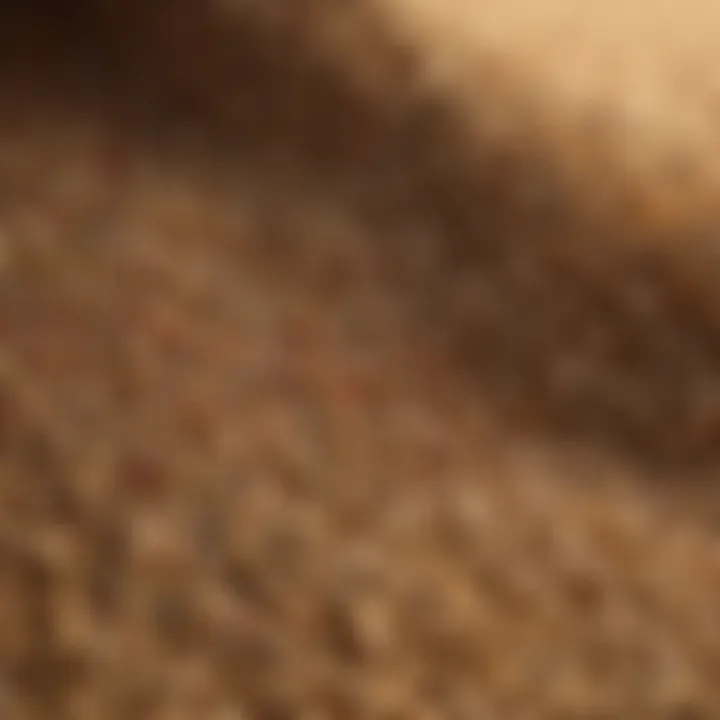
"A good screen isn't just a tool; it unlocks the true potential of your grain cleaning strategy."
In summary, understanding the functionality and types of screens available is essential for implementing an efficient grain cleaning process. When chosen thoughtfully, screens can greatly improve operational success, ensuring that farmers and grain handlers meet their quality and efficiency goals.
Materials Used for Screens
The choice of materials for screens in rotary grain cleaners plays a crucial role in defining their performance, longevity, and overall effectiveness in improving grain quality. Each material has its own unique set of characteristics, benefits, and considerations that significantly impact the screening process. Understanding these materials is vital for agricultural professionals aiming to maximize efficiency and minimize downtime in their operations.
Metal Screens
Metal screens are a staple in many rotary grain cleaners, and their popularity is not without good reason. Generally made from stainless steel or carbon steel, these screens offer great durability and strength. Metal screens can withstand harsh environments and heavy loads while resisting damage from foreign materials often found in grains.
Benefits of Metal Screens:
- Durability: Their robust construction allows them to last longer than softer materials. They can endure the abrasive nature of certain grains, thus reducing the frequency of replacements.
- Accurate Sizing: Metal screens can feature precise hole sizes, which help ensure that the grains are sorted effectively, leading to higher cleaning efficiency.
- Heat Resistance: They tend to handle temperature fluctuations better than many other materials, making them suitable for varying operational conditions.
However, it’s essential to remember that metal screens are not without drawbacks. They can be heavy, making installation and handling a bit challenging. Additionally, over time, depending on the grain type, they can corrode, especially if not properly maintained. This aspect necessitates regular monitoring and occasional replacements to ensure functionality, thereby adding to the operational costs.
Polymer Screens
On the other end of the spectrum, polymer screens have gained traction in the agricultural sector due to their lighter weight and flexibility. Made from materials like polyethylene and nylon, these screens offer a host of advantages that can prove beneficial in specific applications.
Benefits of Polymer Screens:
- Weight Advantage: Their lighter nature makes them easier to install and handle, reducing labor costs and time.
- Corrosion Resistance: Unlike metals, polymer screens do not rust, greatly extending their usable life in moist environments where grain is typically stored.
- Customization: Polymer screens can be manufactured in various sizes and shapes, allowing for better adaptability to different rotary grain cleaner models.
One drawback to consider, though, is that polymer screens may not provide the same level of durability in extreme conditions as metal screens. They can suffer wear and tear more quickly when exposed to hard abrasive materials, which may lead to the need for more frequent replacements in certain environments.
In summary, the choice between metal and polymer screens boils down to the specific needs of the cleaning process, the types of grains being handled, and the overall operational conditions. Each material has pros and cons that should be carefully weighed to enhance efficiency and minimize costs in grain handling operations.
Screen Design Specifications
Screen design specifications play a crucial role in optimizing the performance of rotary grain cleaners. A well-designed screen not only facilitates efficient grain cleaning but also enhances the overall quality of the grain itself. The right specifications can lead to better removal of foreign materials, such as dust, chaff, and small seeds, resulting in purer and higher-quality grain. Furthermore, understanding the nuances of screen specifications empowers agricultural professionals to make informed decisions, ultimately influencing operational efficiency and profitability.
Mesh Size and Open Area
The mesh size of a screen determines its ability to filter out unwanted materials while allowing desirable grain to pass through. A larger mesh size, for instance, tends to let more grain through but can also allow small particles to sneak in. Conversely, a smaller mesh may effectively remove contaminants but risks restricting the flow of larger grains, leading to potential clogging.
When considering open area, it is essentially the percentage of the screen's surface that is “open” and available for grain passage. An optimal balance between mesh size and open area is paramount.
- Benefits of Optimal Mesh Size and Open Area:
- Improved grain flow reduces the chances of bottlenecking.
- Enhanced cleaning efficiency ensures more foreign material is removed from the grain, leading to higher quality output.
From a practical perspective, farmers must assess their specific grain types and contamination levels when selecting screen specifications. For example, a farmer dealing with a substantial amount of dust in corn harvest might opt for a finer mesh to achieve better cleaning results.
Screen Thickness and Durability
Screen thickness influences both the durability and functionality of grain cleaners. Thicker screens might offer increased longevity and resistance to wear and tear, but they can also add unnecessary weight to the cleaner. Ideally, the thickness should be chosen based on expected operational demands, grain volume, and type of contaminants likely to be encountered.
Durability is not just a matter of dimension — the materials used in screens significantly affect their lifespan and performance. High-quality metal screens might withstand more rigorous cleaning processes compared to their polymer counterparts, but they can also be heavier and more expensive.
- Key Considerations for Screen Thickness and Durability:
- Select a thickness that balances weight and strength to ensure ease of installation and operation.
- Understand the cleaning processes involved; heavier-duty applications will necessitate thicker screens.
In practice, you might find that the right screen thickness results in less frequent replacements, which can be a financial boon over time. An investment in durable screens essentially pays for itself through reduced maintenance efforts and lower operational downtime.
Ultimately, making well-informed decisions on screen design specifications helps optimize rotary grain cleaning processes, which translates into better grain quality and increased operational efficiency.
Installation of Screens in Rotary Grain Cleaners
The process of installing screens in rotary grain cleaners is crucial, as it directly influences the effectiveness and efficiency of the cleaning process. Proper installation ensures that screens function optimally, maintaining the integrity of the grain while removing unwanted material. Understanding the specific elements, benefits, and considerations involved in the installation process makes it less daunting for operators, resulting in better long-term outcomes.
Measuring for Fit
One of the first steps in the installation of screens is accurate measurement. Operators need to assess the dimensions of the rotary cleaner and the existing screen setup, if applicable. Here are some important points to consider:
- Exact Measurements: Measure the height, width, and depth of the screen housing to ensure a snug fit. Even a small discrepancy can lead to inefficiencies, such as grain leakage or improper flow.
- Understanding Tolerance Levels: Familiarize yourself with the tolerance levels needed for the specific type of screen being installed. Some screens are designed to be slightly flexible, while others must fit precisely.
- Assessment of Existing Equipment: If you are replacing an old screen, it’s wise to take note of how the previous screen fit. Check for any wear or alterations that might affect the fit of the new screen.
In some cases, operators might even use templates or guides to assist in achieving the perfect fit. This effort might seem trivial at first, but—like the old adage goes—"measure twice, cut once" rings particularly true in this context.
Securing Screens Properly
Once screens are accurately measured, securing them becomes the next pivotal task. A well-secured screen will not only enhance performance but also prolong its life. Here are some key practices to follow:
- Using the Right Fasteners: Choose fasteners that match the material of both the screen and the rotary cleaner. Steel fasteners are common for metal screens, while high-strength plastics might suit polymer screens.
- Checking Alignment and Tension: As you install, ensure that the screen is properly aligned with the housing. Maintaining the correct tension prevents sagging, which can lead to misalignment and operational issues.
- Final Tightening and Inspection: After everything is in place, perform a final tighten of fasteners. Don’t just walk away afterwards; visually inspect to ensure that nothing is amiss. A thorough check can save you headaches later.
"Installing screens accurately not only improves performance; it can be the difference between a good harvest and a poor one."
Understanding the installation process makes a world of difference to operators. When done correctly, the installation of screens leads to a more effective grain cleaning operation, ultimately maximizing both quality and efficiency in the handling of grain.
Maintenance of Screens
Regular maintenance of screens in rotary grain cleaners is essential for several reasons. First, proper upkeep not only prolongs the life of the screens themselves but also ensures that the cleaning processes continue to operate at peak efficiency. Neglected screens can accumulate debris and damage over time, affecting their effectiveness and potentially leading to more expensive repairs or replacements.
Additionally, routine maintenance can prevent unexpected shutdowns, which can cause significant disruptions in grain cleaning operations. A well-maintained screen system contributes to consistent grain quality, ultimately benefitting the end consumer.
Regular Inspection Practices
Routine inspections form the backbone of good maintenance strategy. By frequently checking the condition of screens, operators can identify wear and tear before they escalate into larger issues. Here’s how you can ensure your screens are in top notch shape:
- Create a Schedule: Set a regular inspection timeline, whether it’s weekly, bi-weekly, or monthly. Consistency is key.
- Visual Checks: Look for physical signs of damage, such as holes or cracks. Even small imperfections can lead to larger problems down the line.
- Performance Monitoring: Pay attention to changes in cleaning efficiency. If performance starts to dip, it may be time to investigate the screens more closely.
"Maintaining screens is like keeping your car in tune; neglect can lead to a breakdown at the worst possible moment."
During inspections, it’s important to check connections and fittings as well. A loose connection can change the tension of the screen, leading to more wear and tear.
Cleaning Techniques
Effective cleaning techniques for screens play a pivotal role in maintaining optimal functionality. Dust and grain residue can build up on screens, hindering airflow and reducing the cleaning effectiveness. Here are some recommended cleaning methods:
- Air Blowing: Use compressed air to blow off the dust and debris. This is an effective method that can often clear out clogs that may be forming.
- Water Washing: If screens are heavily soiled, a gentle water wash may be necessary. Ideally, this should be done using a sprayer to avoid damaging the screen material.
- Brush Cleaning: For stubborn residues, soft brushes or scrapers can be used carefully. Be sure not to apply too much pressure, as this can lead to further damage.
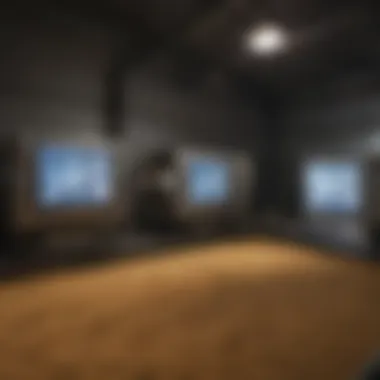

By incorporating these cleaning techniques regularly, operators ensure their screens remain effective, extending their lifespan. It's prudent to schedule these cleaning sessions in alignment with the inspection routine, as they complement each other.
Maintaining screens in rotary grain cleaners isn't merely a task—it's a crucial component of keeping grain processing efficient and effective.
Performance Metrics in Grain Cleaning
Performance metrics are absolutely crucial in the realm of rotary grain cleaning. They serve as the benchmarks that help operators understand how well their systems function. At the heart of it all, these metrics provide a transparent view into the cleaning process, revealing insights that can guide decisions for improvement and optimization.
Evaluating these performance metrics brings several benefits. Firstly, it allows for the identification of inefficiencies within the cleaning operation. If a particular screen type fails to deliver optimal results, it might be time to reassess the selection or consider adjustments in cleaning speed. Ultimately, employing proper metrics can greatly enhance both productivity and grain quality., fostering higher satisfaction in end products.
Beyond that, understanding these metrics is intertwined with larger operational goals. For example, targeting higher cleaning efficiency not only minimizes waste but can also lead to significant cost savings in the long run. With the right data in hand, farmers can adjust their practices to be more sustainable and less labor-intensive, which presents its own set of advantages.
Measuring Cleaning Efficiency
To gauge cleaning efficiency accurately, operators often rely on several key indicators. One prominent metric is the cleaning rate, which assesses how many tons of grain can be processed within a specific timeframe. High cleaning rates typically correlate with effective screen performance, which is essential when dealing with varying grain qualities.
Alongside this, the screen throughput is another critical measure. This reflects how well the screens manage to separate unwanted materials from the grain. If throughput is less than expected, it could signal issues such as improper screen tension or an incorrect mesh size that requires adjustment.
Operators often implement quality control checks throughout processing as well. For instance, taking periodic sample tests of both cleaned and uncleaned grain provides data that helps keep the cleaning process on the right track. These checks ensure that the grain meets the expected quality standards, validating the efficacy of the screen in use.
Impact on Grain Quality
When it comes to the quality of grain, the role of effective screens cannot be overstated. The ultimate goal of any grain cleaning operation is to produce high-quality output that meets market demands and consumer expectations. Clean grain boasts enhanced marketability and shelf life, which is essential for profitability in agriculture.
The impact on grain quality can be measured in various ways. A more thorough cleaning process can remove dirt, stones, and other impurities. This leads not only to a cleaner product but, more importantly, to a reduced risk of contamination which is pivotal for food safety.
In fact, grain quality metrics often extend to the nutritional value as well. High-quality grain generally retains more nutrients, supporting healthier returns for consumers and encouraging sustainable farming practices. Good grain, clean and pure, feels like a badge of honor for the farmer, showcasing both diligence and commitment to excellence.
"In agriculture, quality grain doesn't just happen; it requires commitment to processes that ensure cleanliness at each stage."
To sum up, the meticulous measurement of performance metrics, including cleaning efficiency and its subsequent impact on grain quality, play a vital role in optimizing rotary grain cleaning. Through careful monitoring and adjustments, operators can significantly elevate their output, ultimately leading to long-term benefits in both product quality and economic viability.
Technological Advances in Screen Design
The rapid evolution of screen technology has been a game-changer for rotary grain cleaners. Not only has it improved the efficiency of grain cleaning processes, but it has also enhanced the quality of the final product. Investing in newer technologies that inform screen design is critical for anyone in the agricultural sector aiming to achieve higher standards.
Innovative Materials
The choice of materials for screens has undergone significant transformation over the years. Traditional metal screens are increasingly being replaced or supplemented with modern materials like high-strength polymers. These innovative materials bring multiple benefits:
- Weight Reduction: Polymer screens are often lighter, which reduces overall equipment load and can improve energy efficiency.
- Corrosion Resistance: Unlike some metals, polymers do not rust, prolonging the life of the screen and requiring less maintenance over time.
- Flexibility: Advanced polymer screens can be engineered to have varying levels of flexibility, which assists in preventing clogging by adapting to the grain flow.
Such materials also allow for greater versatility in screen design, aiding in creating custom solutions tailored to specific grain types and cleaning objectives.
Smart Screening Systems
The integration of smart technologies in screen design marks a substantial leap forward. Smart screening systems capitalize on automation and real-time data analytics to optimize performance. Operators can leverage technology including:
- Sensors: These track grain flow and screen performance, enabling adjustments on the fly to avoid overcrowding or underutilization.
- Data Analytics: By monitoring metrics such as cleaning efficiency, these systems provide actionable insights that help operators fine-tune their processes for maximal effectiveness.
- Remote Operation: The capability to manage screens from a distance adds an element of convenience, allowing farmers to multitask while ensuring optimal cleaning.
Investing in smart screening technologies can ultimately result in improved grain quality, better operational efficiency, and enhanced profitability.
Best Practices for Screen Selection
Selecting the right screens for rotary grain cleaners is essential for maximizing efficiency and enhancing grain quality. This section will explore key practices that agricultural professionals should consider when making screen selections.
Choosing the appropriate screens isn't just about picking the first option off the shelf. It's about aligning screen characteristics with specific operational needs. When you get this right, benefits range from decreased material loss to improved throughput. Moreover, well-chosen screens help minimize wear and tear, extending the life of both the screens and the machinery.
Here are several factors to keep in mind when sorting through screen options:
- Compatibility with Grain Types: Different grains have unique attributes that affect how they interact with screening materials. The size, shape, and density of grains can influence their ability to pass through screens. For instance, handling small seeds like canola requires screens with tighter openings compared to larger grains like corn. Knowing the grain type is pivotal.
- Screen Design and Functionality: Not all screens are created equal. Consider the design features, such as mesh patterns and surface textures. Perforated screens, for example, might be preferred for seed cleaning due to their efficient particle separation, while woven wire screens can provide durability for coarse grains.
- Operational Conditions: Screens need to operate under various conditions. Take note of how the rotary grain cleaner is used; whether it processes dry or wet materials, this helps determine the suitable screen material. Polymer screens may perform better in wet environments where metal might corrode.
- Maintenance Requirements: After screen selection, think about the maintenance involved. Choose screens that make cleaning simple, as buildup and clogging are the enemies of efficiency. Regular maintenance routines will help preserve screening effectiveness.
"The right screen can be the difference between good grain and great grain. It's worth the time to choose wisely."
- Testing and Warranties: Before finalizing a screen choice, consider conducting trials. Reach out to the manufacturer for recommendations based on your specific application. Warranties can also be a deciding factor; a product backed by a solid warranty can offer peace of mind.
Following these best practices helps ensure that you have the right tools at hand to achieve your grain cleaning goals. Getting the screen selection right can mean the difference between a successful operation and one burdened with loss and inefficiency.
Evaluating Grain Types
When trying to select the best screens, understanding the specific grain types you work with is fundamental. Different types of grains present different challenges, and selecting screens tailored to these characteristics can streamline the cleaning process.
For example:
- Wheat tends to be light and fluffy, needing screens that offer an optimal balance between letting the grain through while trapping chaff and debris.
- Barley may have larger kernels that require screens with wider openings to maintain flow while still catching straw.
- Oats have varied shapes, which means screens must be selective enough to separate them from lighter materials but wide enough to not hinder the processing speed.
The goal is to understand how grain flows through screens and what needs to be removed. This means analyzing not only the physical characteristics of the grain but also how these aspects affect cleaning efficiency.
Defining Cleaning Objectives
Establishing clear cleaning objectives is critical in guiding screen selection. Consider whether the priority lies in cleaning for purity or maximizing throughput. Different grain operations may require different strategies:
- If you’re cleaning for seed production, tight specifications for purity may necessitate more sophisticated screens with finer mesh.
- Conversely, if your focus is on bulk grain processing for feed, the emphasis may shift to efficiency and speed, allowing for slightly looser screen specifications.
In defining these objectives, also consider the end-use of the grain. For instance, grains destined for food production require stricter cleaning standards than those meant as livestock feed. Therefore, understanding the final stage of the grain's journey can significantly impact your screen selection process.
By carefully evaluating grain characteristics and clearly defining cleaning aims, operators can navigate screen options more effectively, ultimately improving performance and ensuring high quality throughout the operation.
Challenges in Using Screens
In the realm of rotary grain cleaning, while the focus is often on the effectiveness of screens, it’s equally vital to recognize the challenges that arise in their use. Understanding these challenges not only helps in maximizing cleaning efficiency but also ensures operators can safeguard their investment and ultimately protect grain quality. Addressing issues related to screens can prevent complications that could lead to operational downtime, spoilage of quality product, or even excess costs in maintenance. The dual nature of these screens—as both facilitators of cleanliness and the points of potential failure—requires a nuanced approach to their management in grain cleaning systems.
Clogging and Maintenance Issues
One of the most prominent challenges encountered with rotary grain screens is clogging. Over time, screens can accumulate grain husks, chaff, and other debris which inevitably reduces their effectiveness. The extent of this accumulation depends on several factors such as the type of grain being processed, the moisture content, and the overall maintenance routine.
To combat this issue, a routine inspection schedule becomes essential. Here are some key points to consider:
- Regular Check-Ups: Make it a habit to inspect the screens at routine intervals. This includes checking for any visible obstructions and ensuring that the open areas of the screens remain effective.
- Optimal Cleaning Procedure: Establish a standard cleaning procedure that can be implemented before and after processing to minimize the buildup of grain residue.
- Use of Air Blowers: In situations where mechanical cleanings alone aren’t enough, employing air blowers can significantly enhance the efficiency of the cleaning process by dislodging stubborn clogs without damaging the screens.
Efficient handling of clogging issues translates not only into better performance but also prolongs the lifespan of the screens while maintaining cleaner grain.
Wear and Tear of Screens
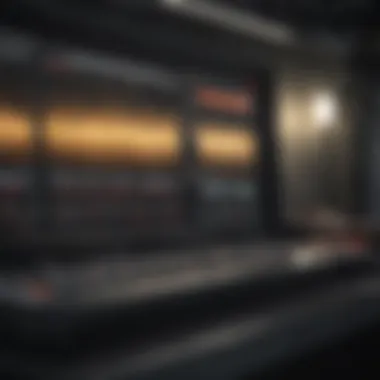
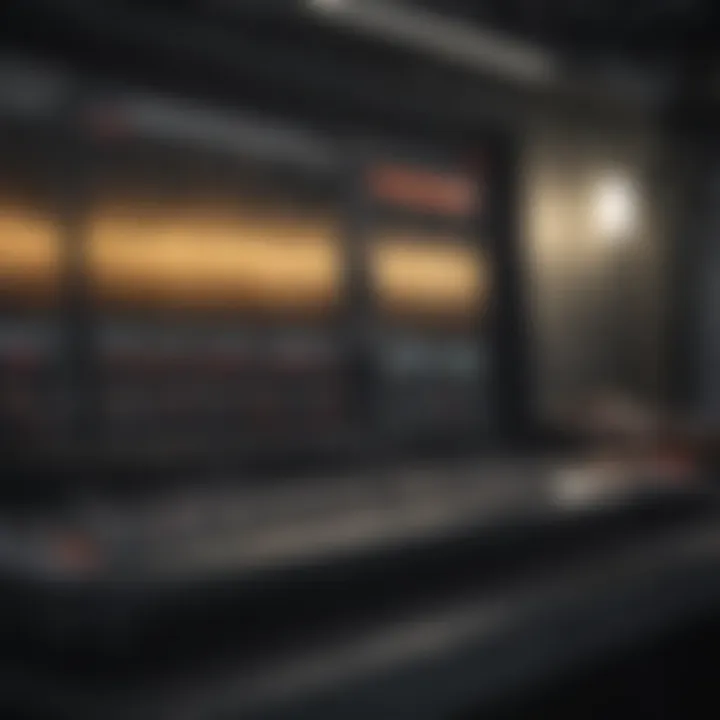
Wear and tear is an inevitable aspect associated with the use of screens in rotary grain cleaners. Depending on the material and design of the screen, different signs of wear can manifest over time, manifesting ideally in both minor and significant ways. If left unchecked, the deterioration of screens can severely hinder grain cleaning effectiveness.
Factors to consider regarding wear and tear include:
- Material Sensitivity: Different screen materials respond variably to wear. For instance, a woven wire screen may deform differently than a synthetic screen, leading to varying lifespans. Keeping an eye on material specifications helps in anticipating wear patterns.
- Frequency of Processing: Screens subjected to heavy daily loads will experience more rapid wear compared to those used intermittently.
- Usage Conditions: Operating conditions such as humidity, temperature, and grain type can exacerbate wear. It’s crucial to match screen materials and design with the specific grain handling environment.
"Conservative use of screens leads to more sustainable operations, ensuring your grain remains as pristine as when it entered the system."
To mitigate wear and tear, consider integrating a proactive replacement plan. This encompasses:
- Replacement Scheduling: Develop a timeline for regular screen replacements based on usage intensity and material characteristics.
- Monitoring Equipment: Utilize devices that alert operators to abnormal vibrations or noise that might indicate a failing screen.
- Training Operators: Equip your team with training around recognizing early signs of screen deterioration.
Engaging with these aspects of screen challenges equips agricultural professionals with the knowledge necessary to maintain not only their equipment but also the grain quality produced through rotary cleaning systems.
Optimizing Screening Efficiency
In today’s agricultural landscape, the quest for excellence in grain quality is an ever-pressing challenge. One pivotal aspect that can dramatically influence this quality is the efficiency of screening in rotary grain cleaners. Efficient screening not only enhances the cleanliness of the grain but also ensures the longevity of the machinery and reduces operational costs. When screening is optimized, it leads to higher throughput without compromising the quality of the final product.
Adjusting Screen Tension
Screen tension plays a major role in the performance of rotary grain cleaners. When screens are too loose, they may sag and lead to inefficient cleaning, allowing undesirable materials to pass through with the grain. On the other hand, screens that are too tight can cause excessive wear and tear, resulting in failures and malfunctions.
Key elements to consider when adjusting screen tension include:
- Material Type: Different grain types require distinct tension settings. Fine grains like seeds may do better with lower tension, while bulkier grains might necessitate higher tension for effective cleaning.
- Screen Wear: Regular inspection of screens allows for adjustments according to the level of wear. As screens age and develop wear patterns, recalibrating tension can help maintain performance.
- Operating Conditions: Environmental factors such as humidity and dust levels can affect the tightness necessary for effective operation. During wetter conditions, for instance, a looser screen may prevent clogging.
Practitioners often rely on visual checks or specific tension gauges to establish optimal tension levels. A final point to remember is engaging with manufacturers’ guidelines, as they often provide valuable insights on the specific requirements for different models.
Modifying Cleaning Speed
The cleaning speed of rotary grain cleaners is another crucial factor that impacts overall efficiency. Too fast of a speed can result in inadequate cleaning, allowing impurities to remain in the grain, while too slow can lead to operational bottlenecks and potential losses.
To optimize cleaning speed, consider the following aspects:
- Grain Condition: Freshly harvested grain may have more debris or moisture than stored grain. Adjusting the speed based on grain condition ensures that the cleaner can handle the load effectively.
- Screen Type: Certain screens are designed for different flow rates. For example, a woven wire screen may perform better at a specific speed compared to a perforated screen. Understanding the characteristics of the screen can help tailor the cleaning speed appropriately.
- System Configuration: The overall system—such as airflow and feeder mechanics—also influences how speed should be modulated. Ensuring harmony between these elements maximizes efficiency.
It’s important for operators to apply a systematic approach when modifying cleaning speed. Starting with gradual changes and closely monitoring the screening results will ensure that the adjustments made yield desired improvements without adverse effects on grain quality.
Investing time in optimizing screening efficiency ultimately pays dividends, leading not only to higher yield quality but also to more effective use of resources—resulting in a win-win for any agricultural operation.
Economic Considerations
Economic considerations play a vital role in the decision-making process when it comes to selecting screens for rotary grain cleaners. This aspect encompasses various elements that can heavily influence operational costs, ultimately affecting the bottom line of agricultural businesses. Understanding these economic factors enables farm operators to make informed choices that not only enhance their grain cleaning efficiency but also bolster their overall financial health. Below, we discuss two key components of economic considerations: the cost of screens and maintenance, and a return on investment analysis.
Cost of Screens and Maintenance
The cost of screens is a foundational element in the economic equation of rotary grain cleaning. Different types of screens—such as metal or synthetic—come with varying price tags. For instance, while perforated metal screens might be more durable, they could also demand a heftier investment upfront compared to simpler woven wire options. This initial cost can vary widely, making it crucial to evaluate the long-term implications of these choices.
Moreover, maintenance costs are another crucial aspect to consider. Regular upkeep of these screens not only prolongs their life but also ensures that they function efficiently. Neglecting maintenance can lead to significant problems like clogging or wear, which, in turn, incurs higher costs due to diminished effectiveness. Here are a few considerations regarding screen costs:
- Initial Purchase Costs: Factors include the type material, design, and brand reputation.
- Routine Maintenance Expenses: Consider cleaning, repairs, and replacements that may arise over time.
- Labor Costs: Allocating sufficient labor for maintaining the screens can add to the total operational budget.
By strategically evaluating these costs, operators can find a balance between upfront investments and ongoing expenses.
Return on Investment Analysis
Conducting a return on investment (ROI) analysis is essential for understanding the financial benefits of various screen choices. ROI is an analytical tool that helps farmers assess the net return they can expect from their investment in screens and related maintenance. A positive ROI reflects not just a profitable investment but also sustainable practices in grain cleaning that can enhance overall business viability.
When performing an ROI analysis, a few elements should be at the forefront:
- Cost Savings on Labor and Time: Efficient screens minimize the need for frequent interventions, freeing up labor for other tasks.
- Improved Grain Quality: High-quality cleaning translates into better market prices for the grain, which can significantly boost revenue.
- Longevity of Equipment: Investing in durable screens might mean spending more initially, but it can reduce replacement frequency, recovering costs over time.
- Market Demand Fluctuations: Understanding how fluctuations in market prices can affect the ROI is critical; well-cleaned grain tends to demand higher prices, making this a worthwhile consideration.
"Investing in high-quality screens ensures that farmers not only save on operational costs but also reap the benefits of superior grain quality in an ever-competitive market."
In summary, economic considerations are crucial in evaluating the cost implications of screens and maintenance as well as assessing potential returns. For agriculture professionals, taking these factors into account can lead to smarter investments that support both profitability and sustainability.
Case Studies on Screen Performance
When diving into the nitty-gritty of how screens function within rotary grain cleaners, case studies can provide invaluable real-world insights. They serve not only to underscore the theoretical aspects previously discussed but also to illustrate practical applications and outcomes. These case studies are essential for understanding how different screens perform under various operational conditions and grain types, thus helping operators make informed choices that benefit their productivity and improve grain quality.
Comparative Analysis of Screen Types
The comparison of screen types in rotary grain cleaners can shed light on their varying efficiencies and effectiveness. For instance, perforated screens may excel in certain scenarios while woven wire screens could be better suited for others, depending on grain characteristics and cleaning goals. In one agricultural operation in the Central Valley of California, a switch from woven wire to synthetic screens yielded a 15% increase in cleaning efficiency. This change not only reduced downtime due to clogging but also resulted in a higher quality end product.
Consider the distinct performances of different screen types, like:
- Perforated Screens: Known for durability, they handle high volumes well and often deal with seed cleaning.
- Woven Wire Screens: Excellent at removing fines and providing precise cleaning, ideal for specialty crops.
- Synthetic Screens: Lightweight and flexible, they adapt to various grain types and can reduce wear-and-tear costs in the long run.
Insights from these comparative analyses are critical. They inform farmers and agronomists about which screen types are best for their specific situations based on historical performance metrics.
Success Stories from the Field
Many success stories underscore the positive transformations that come from thoughtfully selecting screens for rotary grain cleaners. For example, a farmer in Iowa reported a significant improvement in grain marketability after upgrading his screens. The adoption of a newly designed synthetic screen allowed for enhanced residue removal without damaging the grain itself.
This experience highlights how choosing the right screen can affect not only the quality of the grain but also the financial returns. Some key points from this farmer’s experience include:
- Improved grain purity led to a higher grade from suppliers, subsequently fetching better prices.
- Reduced energy consumption on cleaner operations due to more efficient screens.
- Minimizing maintenance costs, as the new screen design experienced less wear.
"The difference in grain quality was night and day. It wasn't just about cleaning; it was about setting ourselves up for future success in a competitive market."
End
The discussion surrounding screens for rotary grain cleaners concludes with a solid understanding of their significance. Screens are not just an accessory; they're the backbone of effective grain cleaning operations. The benefits of using the right screens cannot be overstated. Proper screen selection and maintenance lead to cleaner, higher-quality grain, which is essential for market competitiveness.
Summarizing Key Insights
To wrap up, several key insights emerge from our exploration:
- Diversity of screens: Each type of screen has its own unique advantages. Whether it's perforated, woven wire, or synthetic screens, knowing when and how to use them dramatically affects cleaning efficiency.
- Materials matter: Selecting the right material impacts the longevity and performance of the screens. Metal screens are durable but may not be suitable for all grain types, while polymer options offer flexibility and lightweight benefits.
- Regular maintenance is crucial: An ongoing inspection routine is vital to avoid issues such as clogging or premature wear.
- Technological advancements are transforming practices: From smarter screening systems to innovative materials, staying informed about the latest developments is necessary for farmers to remain competitive.
Having these insights at hand can empower operators in making informed decisions on screen usage and maintenance, improving overall grain quality.
Future Trends in Grain Cleaning Technology
Looking ahead, the field of grain cleaning technology promises numerous innovations. Here are a few trends to keep an eye on:
- Smart technologies: As farms shift towards more intelligent systems, the integration of IoT (Internet of Things) in grain cleaning could enable real-time monitoring of screen performance. Such advancements will allow farmers to react faster to issues, optimizing efficiency.
- Sustainability focus: With growing concerns about environmental impact, there is a noticeable trend towards the development of eco-friendly materials for screen manufacturing and cleaning processes.
- Data analytics: The use of big data might find its way into grain cleaning. By analyzing cleaning performance data, operators could refine their processes for better results.
- Automation and robotics: The move towards more automated equipment is likely to simplify maintenance tasks and perhaps even screen adjustments, making it easier to keep everything running smoothly.
In summary, while traditional methods still hold value, the future of grain cleaning technology appears to be on the verge of a significant transformation. Taking note of these trends can lead to smarter investments and better outcomes for all involved.