Enhancing Popcorn Production with Sifting Tables
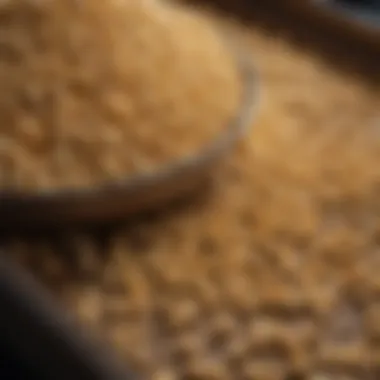
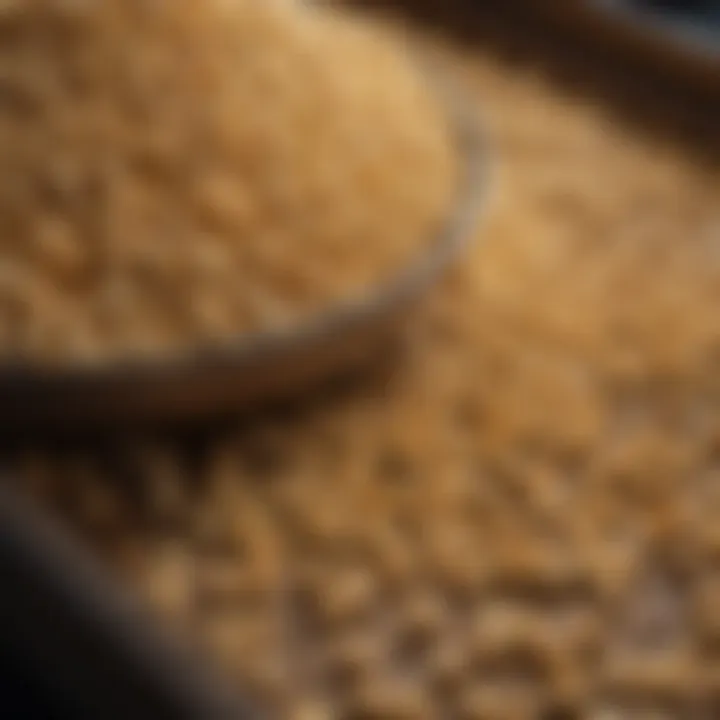
Intro
Popcorn sifting tables play a significant role in the agricultural sector, particularly in the processing of popcorn. Understanding their function and advantages can lead to enhanced efficiency and quality in popcorn production. This article delves into key concepts, current trends, and practical applications related to popcorn sifting tables. The aim is to equip agricultural professionals and enthusiasts with valuable insights that can improve their practices.
Key Concepts and Terminology
Definition of Terms
In discussing popcorn sifting tables, several key terms emerge. Understanding these terms is essential for grasping the full scope of their functionality.
- Sifting Table: A mechanical device designed to filter and separate popcorn kernels based on size and weight, improving the quality of the finished product.
- Sieving: The process of using a sifting table to separate kernels into different classifications, often based on size.
- Grading: The categorization of popcorn kernels based on uniformity, which is crucial for marketability and cooking performance.
Overview of Relevant Practices
The use of popcorn sifting tables is vital to improving both the yield and quality of popcorn. Proper grading and sorting can have a substantial impact on the final product. In addition, these practices minimize waste, ensuring that every kernel is evaluated for its quality. Common practices include:
- Utilizing sifting tables during the initial processing phase to remove debris.
- Implementing multiple layers of sieves to achieve precise sorting based on size.
Current Trends and Innovations
Latest Research and Developments
Current research indicates a growing emphasis on automation in agricultural practices. Newer sifting tables are being developed with advanced features to enhance operational efficiency. Recent studies suggest that incorporating technology can lead to more accurate sorting and grading, ultimately improving yield.
Emerging Technologies and Tools
Emerging technologies have introduced innovative tools that complement traditional sifting practices. Some noteworthy advancements include:
- Connectivity Features: Tables equipped with IoT capabilities enhance monitoring and tracking.
- Automated Adjustments: Sifting tables that automatically adjust based on kernel characteristics, optimizing performance.
Practical Applications
Step-by-Step Guides
- Setting Up the Sifting Table: Ensure the table is leveled properly to prevent incorrect sorting.
- Feeding the Kernels: Feed the popcorn evenly to promote consistent sifting.
- Sifting Process: Allow the table to operate for a specific duration, adjusting settings as needed for desired granularity.
- Collecting Sorted Kernels: Gather the sorted popcorn into designated bins for further processing or packaging.
Troubleshooting Common Issues
It is crucial to address common operational issues that may arise during the use of popcorn sifting tables. Common problems include:
- Poor Sorting Precision: This can usually be addressed by adjusting the speed of the table and ensuring proper alignment of the sieves.
- Frequent Jam-ups: Regular maintenance and checking for debris can minimize downtime.
"The effectiveness of a sifting table greatly influences the quality of the final popcorn product."
Understanding the intricacies of popcorn sifting tables can help agricultural professionals improve their operational processes. Enhanced knowledge surrounding these tools is indispensable to optimize popcorn processing, ultimately benefiting producers and consumers alike.
Prologue to Popcorn Sifting Tables
Understanding popcorn sifting tables is essential for anyone involved in popcorn production. These tables play a crucial role in ensuring the quality of the final product. They separate kernels based on size and remove contaminants. This process increases efficiency and enhances the yield of high-quality popcorn.
Definition and Purpose
A popcorn sifting table is a specialized equipment designed to sort and sift popcorn kernels. Its primary function is to classify kernels according to their size and remove defects. This sorting process is vital for producers as it relates to product quality, market acceptance, and profitability. By ensuring that only the best kernels proceed to further processing, farmers can enhance the overall quality of their products. Additionally, a well-functioning sifting table reduces waste, allowing producers to maximize their harvest.
Historical Context
The use of sifting tables has evolved over time. Traditionally, farmers relied on manual methods for sifting kernels. This process was labor-intensive and often ineffective. With advancements in technology, sifting tables became mechanized, significantly improving both efficiency and accuracy. The introduction of automated sifting tables brought about a new era in popcorn production. Farmers and producers now have access to modern equipment that enhances operational workflow. Understanding this historical context is important for appreciating the current state of popcorn processing. Advances in design and functionality continue to be integrated into new models, reflecting ongoing innovations aimed at improving efficiency in the agricultural sector.
Components of a Popcorn Sifting Table
Understanding the various components of a popcorn sifting table is essential for grasping its overall functionality. Each element plays a significant role in the efficiency of processing popcorn. By examining the surface material, sifting mechanism, and support structure, one can appreciate how these components work synergistically to achieve the desired results in popcorn production.
Surface Material
The surface material of a popcorn sifting table is crucial to its effectiveness and longevity. This material needs to be durable and resistant to abrasion since it comes into direct contact with popcorn kernels. Commonly used surface materials include stainless steel and high-density polyethylene (HDPE).
Stainless steel is favored for its durability and resistance to corrosion. It can withstand the demands of a processing environment, ensuring a longer lifespan. On the other hand, HDPE is lightweight and offers ease of cleaning, which helps maintain the quality of the processed product.
In addition, the texture of the surface can impact the sifting efficiency. A properly textured surface can facilitate the movement of kernels, ensuring effective separation of sizes. Therefore, choosing the right material is not merely a matter of preference but impacts quality and operational efficiency.
Sifting Mechanism
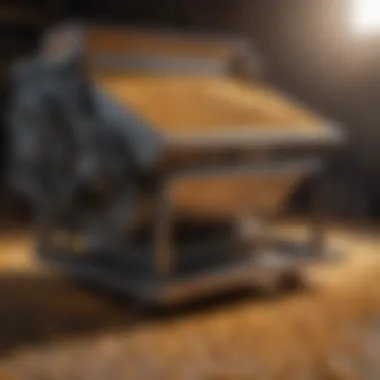
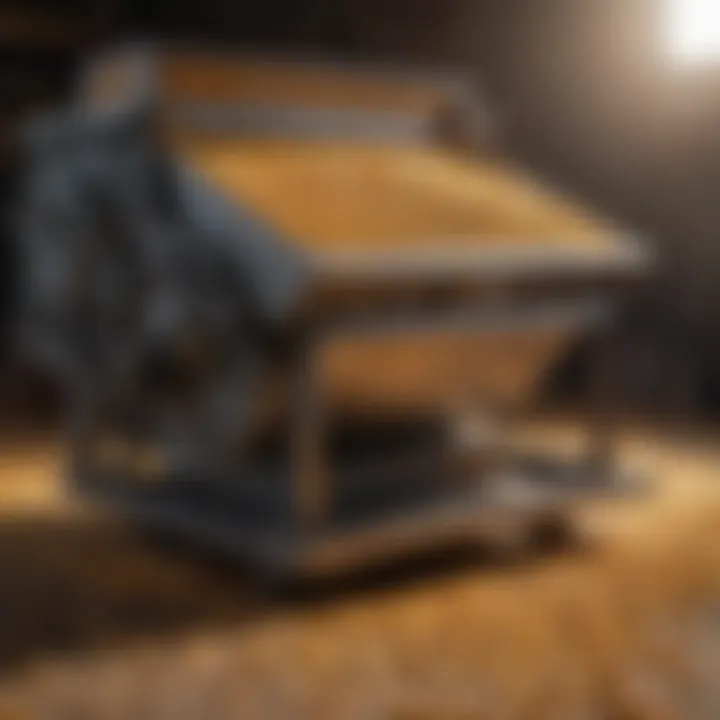
The sifting mechanism is the heart of the popcorn sifting table. This system is responsible for sorting popcorn based on size, weight, and other specifications. Different mechanisms, whether mechanical or vibrational, have unique features and benefits.
- Mechanical Sifting: This traditional method employs various sized screens or perforated plates. Kernels fall through the screens based on size, separating small and large pieces effectively.
- Vibrational Sifting: This modern approach uses vibrations to facilitate the movement of kernels across the surface. The vibrations create a dynamic environment that allows kernels to tumble and sift more efficiently.
Selecting the right sifting mechanism depends on the specific requirements of the operation and desired output quality. A well-designed mechanism minimizes waste while maximizing throughput.
Support Structure
The support structure of a popcorn sifting table provides stability and integrity to the system. It must be robust enough to handle the weight of the popcorn and the equipment without compromising performance.
The materials used for support can vary, but steel frames are prevalent due to their strength and ability to withstand the rigors of a busy processing environment. Proper design considerations should also include vibration dampening features. Such features can prevent unwanted movement during operation, enhancing the overall effectiveness of the sifting process.
In summary, the components of a popcorn sifting tableโsurface material, sifting mechanism, and support structureโ are integral to its functionality. Each element must be carefully considered during the design and selection process to ensure optimal performance in popcorn processing.
Operational Mechanisms
Understanding the operational mechanisms of popcorn sifting tables is crucial for optimizing popcorn processing. These mechanisms facilitate the effective movement, flow, and separation of popcorn kernels from undesirable materials. Each aspect contributes to the overall efficiency in producing high-quality popcorn. The better the operational mechanisms, the more streamlined the process becomes, directly impacting productivity and cost-effectiveness.
Movement and Flow
The movement and flow of kernels through a sifting table determine how effectively materials are processed. Movement typically involves both horizontal and vertical actions that help transport popcorn kernels across the surface.
- Gravity plays a key role in this movement, enabling kernels to shift naturally downward as they are fed onto the table. In many cases, inclined surfaces can further enhance this flow.
- Vibration is another important element; it helps to maintain separation between kernels and debris. This agitation keeps the materials in constant motion, thus increasing the chances of them passing through the various sifting levels.
- Moreover, the design of the sifting table should consider the flow rate of the incoming materials. An appropriate flow rate ensures that the kernels are not overly congested, which can reduce efficiency.
Separation Techniques
Separation techniques are the heart of popcorn sifting tables. These mechanisms are designed to effectively distinguish between popcorn kernels and contaminants, such as husks, dust, and unpopped kernels. Common techniques include:
- Screening: Using different sized screens allows small unwanted materials to fall through while retaining larger kernels.
- Airflow: Adding air jets can help separate lighter materials from heavier popcorn kernels. This method relies on the principle of density, effectively lifting debris away.
- Magnetic separation: In some advanced systems, magnets are used to eliminate metal contaminants. This is vital for ensuring that the popcorn is safe for consumption.
The combination of these techniques leads to a more refined product, ready for packaging or further processing.
Efficiency Enhancements
Enhancing the efficiency of sifting tables involves multiple factors. These enhancements not only improve performance but also reduce operating costs. Important aspects include:
- Automation: Modern systems increasingly incorporate automation features. This includes automatic adjustments in response to varying flow rates and material types, allowing the system to adapt in real-time.
- Regular Maintenance: A routine checking of the components helps in identifying wear and tear. Timely maintenance can prevent breakdowns, which may lead to significant downtimes.
- Training Operators: Staff trained to operate and troubleshoot the machinery contributes significantly to maintaining high operational standards. Knowledgeable operators can enhance the effectiveness of the sifting processes.
The efficiency of operational mechanisms directly correlates to increased productivity and reduced costs in popcorn processing.
In summary, understanding and optimizing the operational mechanisms of popcorn sifting tables leads to better quality control, enhanced productivity, and cost savings for producers.
Design Considerations
Design considerations for popcorn sifting tables play a pivotal role in their efficiency and effectiveness in agricultural practices. Each element of the design contributes not just to the functionality but also to the overall success in quality control during popcorn processing. Understanding these factors can lead to better investment choices and enhanced yield.
Optimal Dimensions
The dimensions of a popcorn sifting table significantly influence its performance and the ease with which it can be integrated into production lines. Tables must be sized appropriately to match the scale of production.
Aspects to consider include:
- Width and Length: The table should accommodate the volume of popcorn meant for processing. Tables that are too small can lead to bottlenecks, affecting efficiency.
- Height: This is crucial for operator comfort and accessibility. The right height decreases the risk of fatigue and enhances productivity.
- Sifting Area: Larger sifting areas can improve the throughput, ensuring that a significant amount of popcorn can be processed within a shorter timeframe.
A well-calibrated dimension allows seamless integration into an existing production workflow. This choice can dramatically decrease processing times and improve overall production efficiency.
Customization Options
Customization in the design of popcorn sifting tables allows operations to tailor the equipment to specific needs and preferences. Each production environment is unique, and having options for customization can lead to better alignment with operational requirements.
- Material Selection: The choice of material for the surface, support structure, and sifting components can affect durability and cleanliness. Stainless steel is often favored for its resistance to corrosion and ease of cleaning.
- Adjustable Features: The ability to adjust the angle of the sifting table can enhance the separation process. This allows operators to fine-tune how the popcorn flows and is sifted, ensuring optimal outcomes for different types of kernels.
- Additional Attachments: Options for integrating aspects like dust collectors, or vibration mechanisms can add functionality. This helps to minimize waste and maintain cleanliness in processing areas.
Customization empowers businesses to create an optimal working environment, maximizing efficiency and maintaining product quality.
Safety Features
Safety in the design of popcorn sifting tables is non-negotiable. Ensuring the safety of operators contributes not only to compliance with regulations but also to the longevity of the equipment and the workforce.
- Guarding Mechanisms: Incorporating guards and covers over moving parts helps to reduce the risk of injury. It is vital that operators are shielded from parts that may create hazards.
- Emergency Stop Controls: Immediate access to emergency stops can enable quick reactions in unsafe situations. This adds an essential layer of safety during operations.
- Non-toxic Materials: Using materials that do not release harmful substances during production is crucial. This ensures that the popcorn remains safe for consumption and aligns with health regulations.
Incorporating these safety features will ensure that operations remain compliant and that workers can perform their tasks in a secure environment.
Design considerations should always balance functionality and safety to promote effective popcorn sifting table performance.
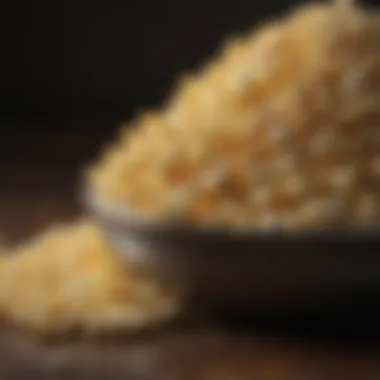
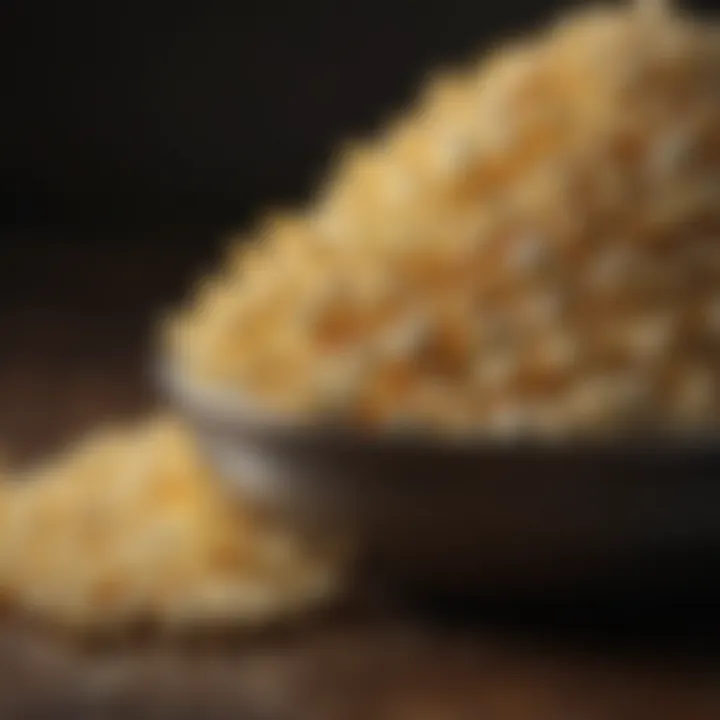
Benefits of Utilizing Sifting Tables
Popcorn sifting tables are a crucial component in the popcorn processing industry. Their primary function is to improve quality and consistency while reducing costs and labor requirements. Understanding these benefits can significantly impact the productivity of agricultural operations that focus on popcorn production.
Quality Control
Quality control is a key aspect of any agricultural practice, including popcorn processing. Sifting tables facilitate this by efficiently removing impurities from the popcorn kernels. This includes foreign materials, broken kernels, and other contaminants that can degrade the quality of the final product.
Using sifting tables helps ensure that only the best quality kernels proceed to packaging or further processing. The consistent performance of these tables minimizes the chances of contamination in the final popcorn product. This quality assurance is vital not merely for maintaining market standards but also for achieving customer satisfaction. A quality-conscious agricultural operation can rely heavily on sifting tables to uphold its reputation.
Cost Efficiency
Cost efficiency in popcorn processing is another significant benefit that sifting tables provide. The use of advanced sifting technology can quickly separate high-quality kernels from lower-grade ones. This separation process reduces waste and improves overall yield, meaning that farmers or processors can obtain more from each batch.
By implementing sifting tables, operations minimize losses and maximize profits. In the long term, this can make a meaningful difference in the bottom line. Labor costs are also lowered since fewer workers are needed to manually sort through kernels. This streamlined process creates a more favorable economic environment for popcorn producers.
Labor Saving
Labor-saving capabilities enhance efficiency in any agricultural operation. Traditional methods of sifting and sorting popcorn often require significant manual effort. Sifting tables automate much of this process, leading to faster throughput and less reliance on human labor. This automation does not only reduce direct labor costs but also lowers the physical strain on workers.
As a result, farms can reallocate labor resources to other pressing tasks, enhancing overall productivity. Additionally, fewer labor errors occur compared to manual sorting, which can often lead to inconsistencies in quality and further issues for popcorn processors. The integration of sifting tables can thus lead to improved operational efficiency, solidifying their value in the popcorn processing sector.
According to industry reports, the adoption of mechanized sifting tables in popcorn production can realize labor savings of up to 30%.
Comparative Analysis
The comparative analysis of popcorn sifting tables is crucial for understanding their role in agricultural practices. This section sheds light on the differences between manual and automated sifting systems, as well as comparing sifting tables to other screening methods. Both comparisons are significant in determining which methods best suit the needs of farmers and popcorn producers. Understanding these distinctions can impact efficiency, cost, and quality of the final product.
Manual vs Automated Sifting
Manual sifting offers simplicity and lower initial investment. It often requires human labor, which some may prefer for artisanal production methods. However, this approach has limitations, particularly in large-scale operations. The manual process is time-consuming and can lead to inconsistencies in the quality of the sifted popcorn. Moreover, labor fatigue can introduce errors in the sifting process.
On the other hand, automated sifting systems present numerous advantages. They enhance throughput significantly, allowing for greater volume processing of popcorn. Automated systems utilize precise mechanical mechanisms to separate kernels from debris consistently. This leads to a more uniform product and reduces the risk of human error. Although the upfront costs of automation can be high, the long-term savings in labor and increased productivity often justify the investment.
Key Considerations:
- Cost: Manual systems generally have lower upfront costs.
- Efficiency: Automated systems are faster and reduce labor needs.
- Quality Control: Automation ensures more consistent quality.
Sifting Tables vs Other Screening Methods
When comparing sifting tables to other screening methods, such as vibration screens or air classifiers, distinct differences emerge. Sifting tables are designed for bulk processing, making them particularly effective for removing foreign materials from popcorn.
Vibration screens, while effective, often require fine-tuning to achieve optimal separation. They can be more suited for smaller items, whereas sifting tables handle larger quantities efficiently. Air classifiers, which use air to separate kernels by weight, can provide high precision but may be costly and less suitable for certain popcorn varieties.
Overall, sifting tables offer a balanced alternative, providing a combination of speed, efficiency, and reliability. For many popcorn processing operations, they become the preferred choice because of their ability to accommodate varying sizes and quantities of popcorn.
"Choosing the right sifting method is essential for quality popcorn production, as it can impact both the efficiency and marketability of the final product."
Consideration Points:
- Capacity: Sifting tables excel at handling bulk popcorn.
- Versatility: They can process different popcorn types efficiently.
- Cost Effectiveness: Sifting tables balance performance with reasonable investment.
In summary, the comparative analysis emphasizes the need for thorough evaluation of sifting methods. It highlights how the choice between manual versus automated sifting, and sifting tables versus other methods, inherently influences not only operational efficacy but also the overall quality of the popcorn produced.
Case Studies
In the realm of popcorn processing, case studies offer valuable insights into real-world applications of popcorn sifting tables. They showcase successful implementations and provide lessons learned, making them pivotal in understanding the practical implications of these devices in agricultural settings. These studies highlight not just the effectiveness of the sifting tables but also the journeys of those who adopted these technologies.
Successful Implementation
Successful implementation of popcorn sifting tables is marked by several key elements. For example, in a recent project at a large popcorn processing facility, a new sifting table was integrated into the existing production line. This facility faced challenges with inconsistent product quality and inefficiencies in separating good kernels from debris. By integrating a sifting table designed with advanced sifting mechanisms, the operation improved significantly. The new table minimized labor costs and reduced waste. Production managers reported a 20% increase in overall efficiency simply by having a more reliable system for sorting.
Benefits from this case include:
- Improved Quality Control: The incorporation of the sifting table led to a notable reduction in broken kernels and unpopped corn, uplifting the overall quality of the end product.
- Cost Savings: With the reduction in spoilage and increase in production efficiency, the facility saw cost savings that facilitated the reinvestment into further technology upgrades.
- Employee Satisfaction: Labor efficiency created less strain on workers, contributing to higher morale as the staff focused on value-added tasks rather than manual sorting.
Lessons Learned
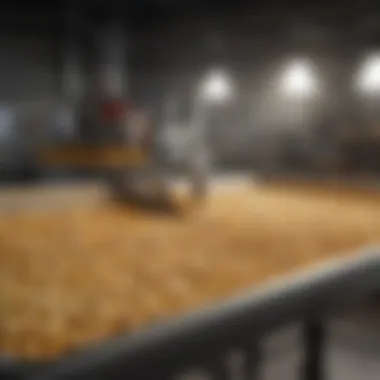
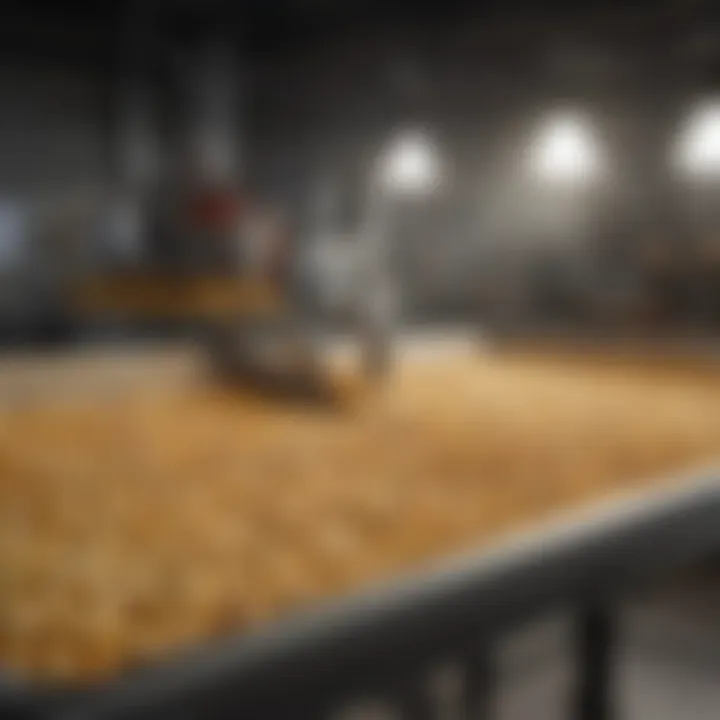
From the implementation case, several lessons emerged that can guide future projects involving popcorn sifting tables. Firstly, selecting the right sifting mechanism is crucial. Facilities that rushed into integration without thorough testing often faced operational setback. Additionally, training staff on the new equipment proved to be an essential aspect of its success.
- Continuous Monitoring: After implementation, constant monitoring of the sifting processes is necessary. This helps in quickly addressing any operational issues before they escalate.
- Adaptation: Each facility from our case studies had unique challenges. Adaptation of the sifting table to meet local processing conditions was necessary. This included adjustments in the angle of the table and speed of operation.
- Feedback Loops: Creating systems for staff to provide feedback about the sifting process greatly improved system refinements. Employee insights often lead to adjustments that enhance both productivity and satisfaction.
Future Trends in Popcorn Processing
The realm of popcorn processing is on the cusp of significant transformation. As markets evolve, new trends are emerging that reflect a blend of technological advancements and an increasing awareness of sustainable practices. Understanding these trends is vital for agricultural professionals. They highlight paths for improving efficiency, reducing environmental impact, and enhancing product quality, all of which are central to the role of popcorn sifting tables.
Technological Innovations
Recent technological innovations are revolutionizing how popcorn is processed. Automation technologies are making sifting tables smart. With sensors and data analytics, these tables can now provide real-time feedback on sifting performance, moisture content, and quality. This connection between machinery and data can streamline operations. For instance, systems like the Grinaker Sifting Table have incorporated advanced vibration controls that optimize the separation process.
These innovations also include the use of machine learning algorithms. They analyze past data to predict operational issues before they occur. This predictive maintenance reduces downtime in operations, resulting in more consistent product quality. Moreover, integration with Internet of Things (IoT) frameworks allows farmers to monitor and control processes remotely, enhancing decision-making capabilities.
"Technological advances are redefining the efficiency and capabilities of popcorn processing systems, allowing for unprecedented levels of precision and control."
Sustainability Practices
Sustainability is becoming a core consideration in popcorn processing. As consumers demand more environmentally friendly practices, the industry is responding by implementing sustainable methods. It begins with choosing materials for sifting tables. Manufacturers are increasingly using recycled or eco-friendly components. This reduces the carbon footprint associated with the production of new materials and minimizes waste.
Energy efficiency is another significant focus. Modern tables are designed to consume less power while achieving higher performance. This is often accomplished through the implementation of energy-efficient motors and drives. Additionally, companies are re-evaluating their waste management practices. By integrating systems that recycle by-products from popcorn processing, businesses contribute to a circular economy, minimizing landfill waste.
Challenges and Solutions
In the context of popcorn processing, challenges and solutions play a pivotal role. Identifying operational difficulties and devising effective strategies can greatly enhance the efficiency of popcorn sifting tables. Understanding these challenges can help agricultural professionals make informed decisions regarding their operations. By addressing these issues, farmers can ensure higher quality output and optimize the processing of popcorn.
Common Operational Challenges
Several challenges may arise during the operation of popcorn sifting tables. These include:
- Material Blockages: Residual kernels or foreign materials can cause blockages in the sifting mechanism. This could slow down operations or require manual intervention.
- Inconsistent Flow Rates: Variations in the flow of popcorn through the sifter can lead to uneven sorting and processing. High or low flow rates may disrupt the efficiency of the table.
- Wear and Tear on Components: Over time, the materials used in the construction of the table may degrade, either due to physical stress or contamination from sifting. Regular maintenance is essential to prevent breakdowns.
- Operator Errors: Unlike fully automatic systems, semi-automated ones require a skilled operator. Inexperienced staff may not optimize the sifting process properly, leading to reduced output.
Addressing these challenges is crucial to maintain operational efficiency and product quality.
Mitigation Strategies
To counter the operational challenges faced by popcorn sifting tables, several mitigation strategies can be employed:
- Regular Maintenance: Schedule routine inspections and maintenance checks. This include cleaning out any blockages and ensuring that all components are functioning properly.
- Flow Regulation: Utilize flow regulation systems to maintain a consistent rate of material processing. This might involve adjusting the size of the feeder outlet or using gates to control the throughput of popcorn.
- Training for Operators: Provide comprehensive training for operators to ensure they understand the equipment's intricacies and capabilities. This promotes better handling and maximizes efficiency.
- Upgrading Materials: Invest in high-quality components that resist wear and provide better reliability. Materials that withstand the rigors of operation without significant degradation will improve the life and performance of the sifting table.
- Regular use of specialized cleaners can prevent residue buildup, especially in areas prone to clogs.
- Implementing sensors and automated feedback systems can also help monitor and control flow dynamics.
- Engage experienced professionals in training sessions to ensure knowledge transfer occurs effectively.
- Consider materials like stainless steel or composites designed for industrial use are recommended.
By implementing these mitigation strategies, agricultural professionals can significantly enhance the reliability and performance of popcorn sifting tables, contributing to improved operational outcomes.
Investing time and resources into understanding and overcoming these challenges pays dividends in the long run through improved efficiency and product quality.
Closure
The conclusion serves as the final reflection on the critical role of popcorn sifting tables in agriculture, particularly within the realm of popcorn processing. This section emphasizes how these tables not only streamline operational processes but also significantly enhance the overall quality of popcorn. It underscores the multifaceted benefits that agricultural professionals can gain from incorporating sifting tables into their workflows.
Summary of Key Points
Over the course of our examination, we have explored several important aspects of popcorn sifting tables:
- Definition and Purpose: These tables are designed to separate unwanted materials, thus ensuring that only high-quality kernels proceed to the next processing stage.
- Operational Mechanisms: Understanding movement and separation techniques reveals how sifting tables function effectively to maximize output.
- Design Considerations: Customizable features and safety aspects contribute to their adaptability and usability in various agricultural settings.
- Benefits: Enhanced quality control, cost efficiency, and labor savings illustrate just a few advantages associated with the use of sifting tables.
In summary, popcorn sifting tables are not just tools; they are integral components in modern popcorn production that can lead to better product quality and more efficient operations.
Future Implications
Looking ahead, the future of popcorn processing with sifting tables appears promising. Several trends and developments indicate that the technology surrounding these tables will continue to evolve. Key implications include:
- Technological Innovations: Advances in automation and intelligent design are likely to enhance the efficiency and effectiveness of sifting tables.
- Sustainability Practices: As farmers seek to minimize waste and environmental impact, incorporating sustainable materials and practices in the design of sifting tables can become a significant focus.
- Integration with Smart Farming: With the rise of precision agriculture, sifting tables may integrate with smart farming technologies, allowing for real-time monitoring and adjustments to processing methods, thus improving quality control further.
As the industry progresses, embracing new technologies will be crucial for maintaining competitive advantage.
In summation, popcorn sifting tables will remain a pivotal element in agricultural practices, and understanding their role can empower farmers and processors to achieve higher standards in the quality of their popcorn products.