Exploring the Jancy Tube Bender: A Comprehensive Guide
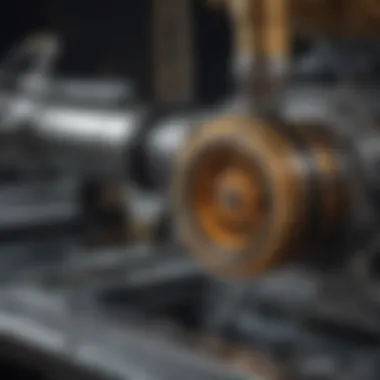
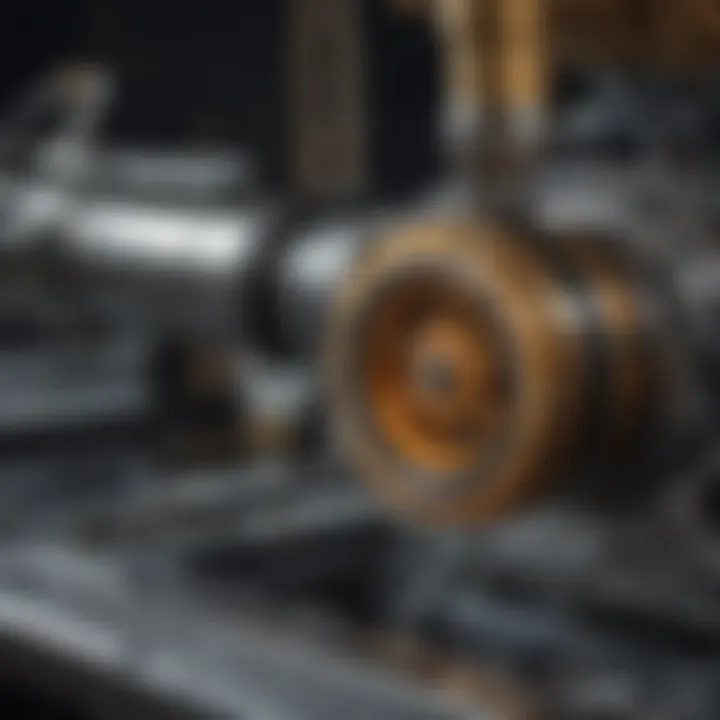
Intro
The Jancy tube bender stands as a pivotal instrument in the realm of metalworking and fabrication, particularly valued for its precision and efficiency. As industries evolve, the demand for durable metal structures grows, especially within agriculture, where frameworks for machinery and buildings require both strength and adaptability. This comprehensive guide dissects the design, functionality, and extensive applications of the Jancy tube bender, offering insight not only for metalworkers but also for agricultural professionals seeking to enhance their operations.
"Understanding the tools of fabrication is essential for anyone serious about optimizing their workflow and improving structural integrity in farming applications."
Key Concepts and Terminology
To fully grasp the significance of the Jancy tube bender, one must familiarize themselves with pertinent terminology and concepts that define its use.
Definition of Terms
- Tube Bender: A machine used to bend a variety of metal tubes into specific shapes or angles without compromising structural integrity.
- Fabrication: The process of cutting, bending, and assembling materials to create components or structures.
- Degrees of Bend: Referring to the angle through which a tube is bent, crucial in achieving desired specifications.
Overview of Relevant Practices
In metalworking, practices like clean cuts, proper angle measurement, and understanding material properties are essential. The Jancy tube bender simplifies these tasks, allowing for repeatable precision in metal shaping. Professionals in agriculture benefit by creating durable and customized frameworks that meet specific operational needs, such as equipment supports or structural reinforcements.
Current Trends and Innovations
The landscape of fabrication is continuously changing, brought on by emerging technologies and methods.
Latest Research and Developments
Recent studies have indicated advancements in CNC (Computer Numerical Control) tube bending, integrating automation into traditional practices. These developments enhance accuracy and reduce labor time, making it a preferred choice in industrial settings.
Emerging Technologies and Tools
With the rise of IoT (Internet of Things) in manufacturing, smart tube benders equipped with sensors are becoming available. These devices monitor bending processes in real-time, providing feedback and adjustments to ensure optimal performance and reduce waste.
Practical Applications
The functionality of the Jancy tube bender encompasses various practical applications, making it a transformative tool in agriculture.
Step-by-Step Guides
To effectively utilize a tube bender, follow these general steps:
- Preparation: Gather materials and ensure the workspace is clean.
- Measurement: Accurately measure the required length and angle for the bend.
- Set Up: Place the tube in the bender, securing it firmly.
- Bending: Slowly initiate the bending process, applying consistent pressure for a smooth finish.
- Final Check: After bending, measure angles and lengths to confirm accuracy.
Troubleshooting Common Issues
Some common problems include:
- Wrinkling: This may occur if the tube is not supported properly during bending. Ensure adequate support.
- Incorrect Angles: Double-check measurements before the bending process to avoid mistakes.
Familiarity with these aspects will aid professionals in maximizing the utility of the Jancy tube bender in their tasks.
Prelude to Tube Bending
Tube bending is a fundamental process in metalworking that allows for the creation of various structures, components, and frameworks. Understanding this process is essential for anyone involved in industries such as agriculture, automotive, or manufacturing. The use of tube benders, like the Jancy tube bender, has transformed how metal is shaped and utilized. By examining the techniques and benefits of tube bending, one can appreciate its increasing relevance in modern fabrication.
Overview of Tube Bending
Tube bending is the technique of deforming a tube or pipe along a defined bend radius. The process can be applied to different materials, including steel, aluminum, and other metals. Depending on the requirements, it can be executed through several methods such as rotary draw bending, roll bending, or compression bending. Each technique offers unique benefits and considerations depending on the project.
Using a tube bender such as the Jancy model significantly enhances the precision of bends, allowing for repeatable results with high accuracy. This is crucial for structural integrity in projects like greenhouses or machinery frameworks where reliability is paramount.
Importance in Metalworking
Tube bending plays an important role in the field of metalworking for several reasons:
- Versatility: It allows for the creation of a wide range of shapes and designs, which are essential in various applications from construction to agricultural tools.
- Structural Strength: Well-executed bends can result in stronger components compared to those made with welded joints, thus enhancing overall durability.
- Material Efficiency: Bending processes often result in less waste compared to cutting and welding, which can promote cost savings and environmental sustainability.
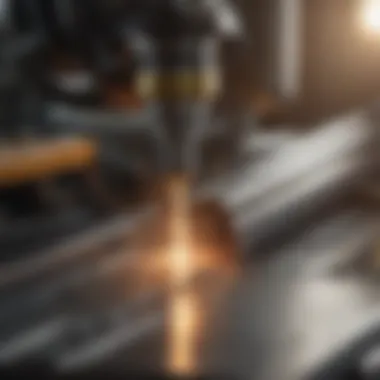
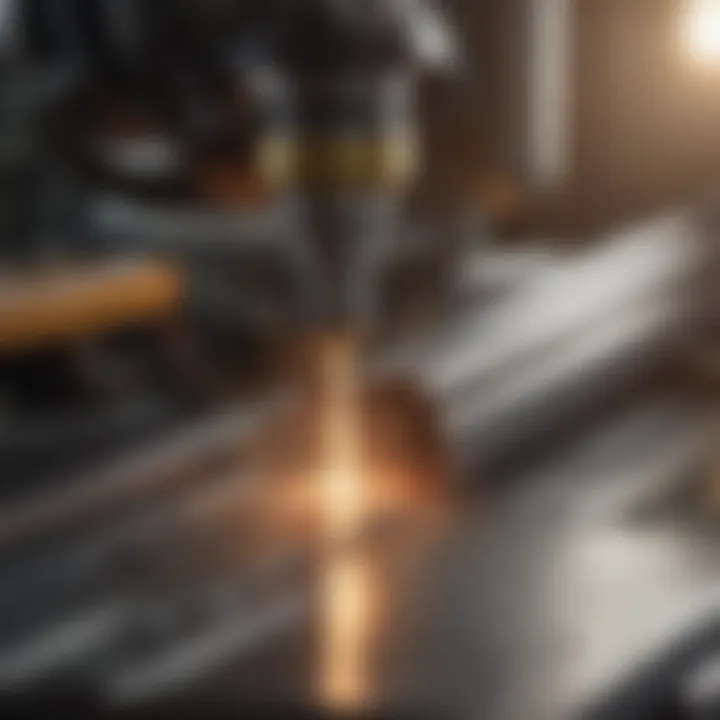
In summary, an understanding of tube bending is crucial for those in the field of metalworking. The Jancy tube bender exemplifies the advancements in this area, making it an invaluable tool in many applications around agriculture, manufacturing, and beyond.
Understanding Jancy Tube Bender
Understanding the Jancy Tube Bender is essential for anyone involved in metalworking and fabrication, particularly in agriculture. This tool is not just a machine; it's a valuable investment that enhances productivity and precision in a variety of tasks. The significance of the Jancy Tube Bender lies in its design and capabilities, which enable it to perform a wide range of bending operations with ease.
History of the Jancy Tube Bender
The Jancy Tube Bender has a rich history that traces back to the evolution of metalworking. Initially designed for simple bending tasks, Jancy continuously developed its technology to meet the demanding needs of industries such as automotive, construction, and agriculture. Over the years, enhancements in functionality, portability, and capability have made Jancy Tube Benders essential in modern workshops. This evolution reflects a broader trend in manufacturing towards automation and efficiency.
Key Features and Specifications
When considering a Jancy Tube Bender, one must look at several key features. Below are some specifications that make the Jancy Tube Bender stand out:
- Bending Capacity: This can handle a range of tube sizes and materials, making it versatile for different projects.
- Precision Controls: Exacting controls enable operators to achieve consistent bend angles and radii.
- Durable Construction: Made from robust materials, these machines are designed to withstand extensive use in industrial settings.
- Portability: Certain models have been designed with a lightweight frame, making them easier to transport.
These features collectively enhance the efficiency of metal fabrication tasks, making Jancy Tube Benders a preferred choice among professionals.
Types of Jancy Tube Benders
Several types of Jancy Tube Benders cater to different needs in the market. Understanding these can help buyers select the right model for their specific application. The main categories include:
- Manual Tube Benders: Ideal for projects requiring minimal bending. They offer greater control, though they demand more effort from the user.
- Electric Tube Benders: Suitable for high-volume jobs, these machines simplify the bending process by automating many tasks.
- Hydraulic Tube Benders: Known for their power, hydraulic benders can handle thicker materials with less manual effort, making them ideal for large-scale operations.
Recognizing the types available can significantly impact operational efficiency, ensuring users select the best fit for their projects.
Mechanics of Tube Bending
Understanding the mechanics of tube bending is essential for anyone working with metal, particularly when it comes to using tools like the Jancy tube bender. The mechanics govern how metal behaves during the bending process, dictating the quality and durability of the final product.
The tube bending process is not merely about shaping metal; it involves an intricate interplay between force, material properties, and the bending tool itself. This section examines the bending process, the tools that assist in achieving precise bends, and the crucial safety measures that must be taken.
Bending Process Explained
The bending process involves several steps that determine how effectively the tube can change shape without compromising its integrity. Initially, the tube is securely clamped within the bender, which ensures that it remains stable during the operation. The bending tool then applies pressure, gradually curving the tube to the desired angle. This is not a simple task, as it requires an understanding of the metal's yield strength and the specific bending radius. Depending on the type of bend required, variations in speed, pressure, and angle will affect the final result.
One critical element to consider is the degree of deformation the metal can withstand. If excessive force is applied, the material can fracture, leading to waste and costly repairs. Furthermore, the accuracy of the measurements taken prior to bending will significantly impact the success of the operation. Using advanced measuring tools and techniques can help achieve the necessary precision.
Tools and Accessories
In addition to the Jancy tube bender, various tools and accessories enhance the bending process. These may include:
- Measuring Tools: Calipers and protractors ensure that angles and lengths are accurately measured before and after the bending process.
- Support Fixtures: These help stabilize the tube during bending, preventing any unwanted movement.
- Lubrication Supplies: Using appropriate lubricants can reduce friction, which in turn minimizes wear on the tools and the material itself.
The right combination of these tools can enhance productivity and accuracy. Without them, the risk of producing defective bends increases significantly. Ensuring that all tools are well-maintained and suited for the specific job helps in maintaining a smooth workflow in metalworking tasks.
Safety Considerations
Safety is paramount when operating a tube bender. The bending process can involve high forces, and without proper precautions, operators can be at risk for injury. Here are some key safety considerations:
- Personal Protective Equipment (PPE): Always wear safety glasses and gloves to protect from metal shavings and sharp edges.
- Tool Maintenance: Regularly check and maintain tools to keep them in safe working condition. Inspect for any signs of wear or damage before use.
- Emergency Protocols: Know how to quickly shut down the machine in case of an emergency. Have a clear understanding of emergency exit routes and procedures.
- Proper Training: Ensure that all operators are trained in the usage of the bender and understand the risks involved.
Proper safety measures not only protect the individual but also ensure the integrity of the work being performed.
By being mindful of these aspects, workers can minimize risks and develop safer work environments. They will not only improve their productivity but also enhance overall job satisfaction.
As we proceed through this guide, understanding these mechanical principles will facilitate a more efficient use of the Jancy tube bender, ensuring better outcomes for various metalworking applications.
Applications of Jancy Tube Benders
Jancy tube benders play a pivotal role in various industries due to their versatility and effectiveness. Understanding their applications allows professionals to recognize their value in enhancing production processes and creating precise metal forms. In agriculture, automotive, and metal fabrication, the Jancy tube bender offers specific functionalities that cater to the unique needs of each sector. This section explores these applications in detail, shedding light on the significant benefits and considerations that come with using Jancy tube benders.
Metal Fabrication
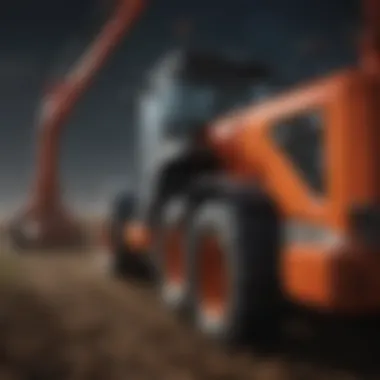
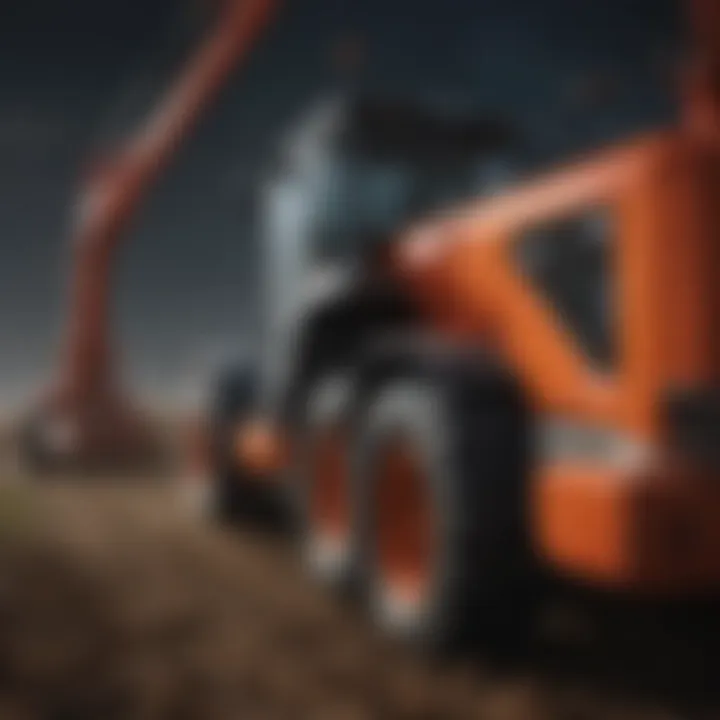
Metal fabrication is an intricate process where raw materials are transformed into finished products. The Jancy tube bender is essential in this domain because it allows for precise bends in metal tubes, contributing to the structural integrity and aesthetics of the products created.
Professionals in metal fabrication must consider the following factors when using a Jancy tube bender:
- Precision: Ensures accurate bends, crucial for maintaining specifications.
- Versatility: Able to work with various metal types and thicknesses.
- Speed: Enhances production efficiency in fabricating metal components.
By utilizing a Jancy tube bender, fabricators can achieve complex shapes that are often required in construction, furniture design, and more. This not only improves the functionality of products but also enhances their overall look.
Automotive Industry
In the automotive sector, tube bending is critical for creating frameworks, exhaust systems, and other components. The Jancy tube bender's capability to produce consistent bends with minimal material waste makes it a preferred choice among manufacturers.
The automotive industry benefits from Jancy tube benders in several ways:
- Quality Control: High-level accuracy reduces the need for reworks.
- Durability: Stronger bends support vehicles' structural integrity.
- Innovation: Facilitates design possibilities that were previously challenging to achieve.
Automotive professionals can streamline production lines and enhance product quality by automating bending processes using Jancy equipment. This efficiency is crucial for meeting consumer demands and maintaining competitive edges.
Agricultural Implements
The use of Jancy tube benders extends significantly into the agricultural sector. These machines help create durable frameworks for various equipment, such as trailers, fences, and even specialized machinery. The advantage of using a Jancy tube bender in agriculture is the ability to customize equipment based on specific farming needs.
Considerations for agricultural applications include:
- Strength: Ensured stability for heavy-duty use.
- Customization: Tailors equipment to suit unique operational requirements.
- Cost Efficiency: Reduces waste and material costs by providing precise bends.
Farmers and agricultural enthusiasts find the Jancy tube bender beneficial not only for productivity but also for creating long-lasting solutions that withstand the rigors of agricultural work. The ability to produce custom solutions directly impacts efficiency and overall farm management.
"The Jancy tube bender is not just a tool; it's an enabler for innovation across multiple sectors, from agriculture to automotive."
In summary, the applications of Jancy tube benders are diverse and impactful. Their role in metal fabrication, the automotive industry, and agricultural implements showcases their utility in enhancing productivity and precision in various projects.
Advantages of Using Jancy Tube Benders
The advantages of using Jancy Tube Benders are manifold and critical to understanding the impact of this tool in the field of metalworking. Utilizing these machines can transform processes in various industries, especially in agriculture. The precision, efficiency, and cost-effectiveness they bring to metal fabrication contribute significantly to productivity and quality of the output.
Precision and Accuracy
Precision is paramount in tube bending. Jancy Tube Benders are designed to provide exceptional accuracy. They allow for repeatable bends that meet strict specifications. This level of precision reduces material wastage and minimizes the need for costly rework. For example, intricate frameworks that are common in agricultural implements demand high precision. Any deviation can lead to poor fitment, which may compromise the structural integrity of the end product. Moreover, using machines with built-in calibration features enhances reliability. It clearly defines the role of accuracy in ensuring that every piece matches the required design.
Efficiency in Production
Efficiency is another key advantage of using Jancy Tube Benders. These machines streamline the bending process, allowing operators to produce bends in less time than manual methods. The speed of operation is crucial, especially in high-volume production environments. By reducing the time spent on each bend, businesses can significantly increase their output without sacrificing quality. For farmers and manufacturers, this means they can meet increasing demands in a timely manner. The integration of automation features in some models further contributes to production efficiency.
Cost-Effectiveness
Cost-effectiveness plays an essential role in selecting a tube bender. Investing in a Jancy Tube Bender, despite the initial cost, often results in savings over time. The increased accuracy leads to reduced waste, and the enhanced efficiency speeds up production, translating to lower labor costs. In the agricultural sector, this is particularly important, as maximizing profit margins is a constant challenge. Additionally, the durability of Jancy Tube Benders means they are less prone to breakdowns, which translates to lower maintenance costs. This consideration makes them a smart investment for any organization focused on long-term sustainability.
"Investing in a high-quality tool like the Jancy Tube Bender is an investment in precision, efficiency, and cost reduction—essential factors for competitive success in any industry."
In summary, the advantages of Jancy Tube Benders encompass various aspects. Their ability to provide precision and accuracy, improve efficiency in production, and maintain cost-effectiveness not only enhances productivity but also supports the overall operational goals within the agricultural and metalworking sectors. This solid foundation makes Jancy Tube Benders a valuable asset for professionals aiming for excellence.
Maintaining Your Jancy Tube Bender
Ensuring the longevity and functionality of your Jancy tube bender is crucial for optimal performance in metalworking. Proper maintenance not only extends the lifespan of the equipment but also enhances efficiency and precision in bending processes. Neglecting maintenance can lead to common issues such as misalignment, tool wear, and even machine failure. By employing routine practices, troubleshooting methods, and knowing when to seek professional assistance, users can ensure their tube bender remains in excellent working condition.
Routine Maintenance Practices
Routine maintenance practices are essential for keeping your Jancy tube bender running smoothly. Here are some key practices to consider:
- Regular Cleaning: Dust and metal shavings should be cleared from the machine to prevent buildup that can affect its operation.
- Lubrication: All moving parts must be lubricated according to the manufacturer’s guidelines. This helps reduce friction and wear on components.
- Inspection: Periodic inspections of all mechanical and electrical systems should be done. Check for any signs of wear or damage, including hoses, fittings, and electrical connections.
- Calibration: Ensure the bender is calibrated to specifications. Regularly check and adjust settings to maintain accuracy in bends.
Following these practices can greatly enhance the performance and safety of your Jancy tube bender.
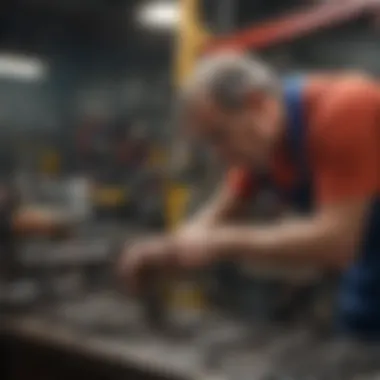
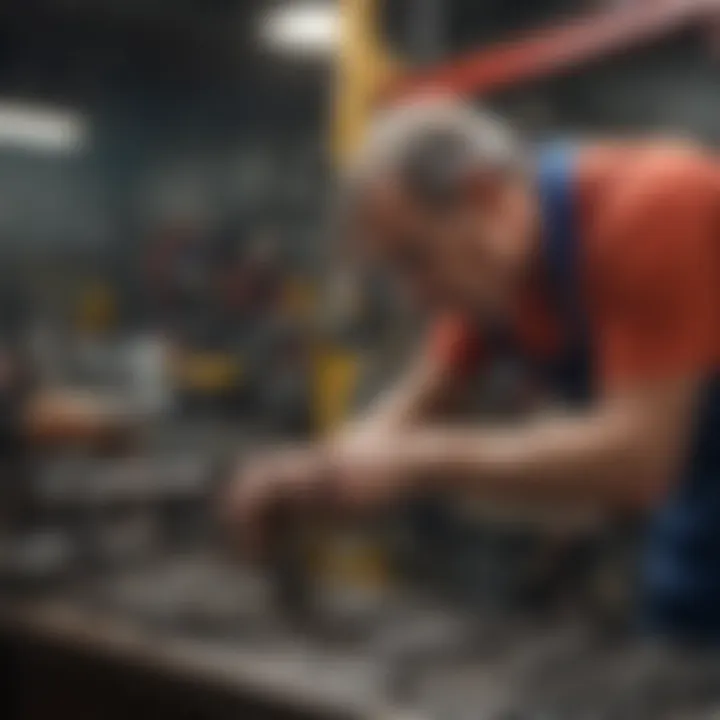
Troubleshooting Common Issues
Users may encounter various issues while operating their Jancy tube bender. Here are some common problems and their potential solutions:
- Inconsistent Bends: This could be due to incorrect setup or calibration. Double-check alignment and re-calibrate if necessary.
- Tool Wear: Dull or damaged tools can affect the quality of bends. Regularly inspect tools and replace them when needed.
- Electrical Problems: If the machine does not start or exhibits erratic behavior, inspect the electrical system and connections. A malfunction may require professional evaluation.
- Fluid Leaks: Observe for any hydraulic fluid leaks, which could indicate worn seals or fittings. Address leaks promptly to avoid further damage.
By knowing how to troubleshoot these issues, operators can efficiently maintain their equipment without interruption in work.
When to Seek Professional Help
While routine maintenance can often address many issues, there are situations when professional help is necessary. Consider consulting a professional if you experience any of the following:
- Complex Repairs: If repairs involve significant disassembly of the machine, it is best to have a qualified technician perform the work.
- Persistent Problems: If an issue continues despite troubleshooting and routine maintenance, outside help can provide insights and solutions that may not be apparent.
- Upgrades or Modifications: For upgrades to the machinery, consulting a professional ensures compatibility and optimal performance.
In sum, maintaining your Jancy tube bender is a critical aspect of ensuring its reliability and efficiency. Routine care, quick resolution of common issues, and knowing when to call in expert help will contribute to peak performance in all metalworking tasks.
Selecting the Right Tube Bender for Your Needs
In the vast landscape of tube bending, choosing the right equipment stands as a keystone decision. The effectiveness and precision of tube bending tasks hinge on proper selection. Your project’s requirements, including material type and specifications, will play a substantial role in determining the most suitable Jancy tube bender. A mismatch between the machine and the job at hand may lead to inefficiency or compromised quality.
When selecting a tube bender, understanding the unique features of Jancy products can aid significantly in making an informed choice. Each model may present different capabilities, whether it relates to the degree of bend achievable or the size and thickness of tubes it can handle. Therefore, comprehensive knowledge of the project requirements becomes paramount.
"Selecting the right tube bender is not just a choice; it’s a strategic decision that can influence production efficiency and end product quality."
Ultimately, well-considered decisions foster better outcomes in both productivity and cost effectiveness.
Assessing Project Requirements
Assessing the specific aims of your project is a foundational step in the selection process. One must consider the type of materials involved – whether you are working with steel, aluminum, or other alloys. Each material has its own bending properties which the bender must accommodate. Furthermore, knowing the diameter and wall thickness of the tubing is essential.
Parameters to assess include:
- Tube material – metal types possess varied conductivity and flexibility.
- Diameter and wall thickness – influences the type of bender required.
- Bending radius – sharp bends require specialized benders.
- Volume of production – high volumes may benefit from automated options.
In addition, examining the end-use of the bent tubes can provide insightful data. Consider whether you need precise bends for structural integrity or more flexible bends for aesthetic applications. The objectives guide you in choosing between models that excel in precision versus those that offer better overall throughput.
Budget Considerations
Budgeting for a tube bender adds another layer to your decision-making. The price range of Jancy tube benders can vary significantly based on specifications and features. Allocating financial resources judiciously ensures you acquire a machine that meets project needs without overextending your budget.
First, evaluate the cost of operation in relation to the benefits gained. Sometimes, an initial higher investment may lead to lower operating costs in the long run due to durability and efficiency. Additionally, consider the expenses related to maintenance and potential repairs over time.
When crafting a budget plan, be clear about:
- The initial investment required for the desired model.
- Long-term costs such as maintenance and part replacements.
- The return on investment based on expected output and quality.
Understanding these elements provides clarity and ensures that the selected equipment aligns both technically and financially with your operational objectives.
End
The conclusion of this article encapsulates the essential insights into Jancy tube benders and their pivotal role in various applications. Tube bending, particularly using the Jancy brand, offers significant advantages in precision and efficiency. Understanding these benefits helps professionals, especially in the agriculture sector, to make informed decisions that enhance their operational outputs.
Future Trends in Tube Bending Technology
The landscape of tube bending technology is continually evolving. Future trends indicate a shift towards automation and integration of advanced software solutions. These innovations aim to improve accuracy and reduce waste throughout the production process.
Another notable trend is the development of more eco-friendly materials and processes. Manufacturers are seeking ways to minimize the environmental impact of tube bending operations. This transition will likely involve using recyclable materials and energy-efficient machinery.
As technology progresses, professionals in the industry must remain adaptable to leverage these advancements effectively.
Additionally, data analytics is expected to play a significant role in enhancing the efficiency of tube bending operations. By analyzing performance metrics, users can make proactive adjustments that lead to improved outcomes.
Final Thoughts on Jancy Tube Benders
In summary, Jancy tube benders represent a valuable investment for those engaged in metalworking. Their versatility and reliability are undeniable. With features designed to address various bending needs, Jancy tube benders are tailored to meet the demands of both small-scale and large-scale operations.
While selecting the right tube bender, careful consideration of specific project requirements and budget constraints is vital. This article has explored critical aspects of Jancy tube benders, equipping readers with the knowledge necessary to optimize their use.
By focusing on the benefits, applications, and future developments in tube bending technology, it is clear that the Jancy tube bender is not just a tool, but an essential component that can elevate quality and productivity in metalworking and agricultural frameworks.