Understanding the GQF Incubator and Hatcher Guide
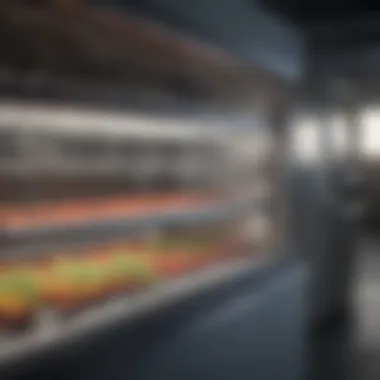
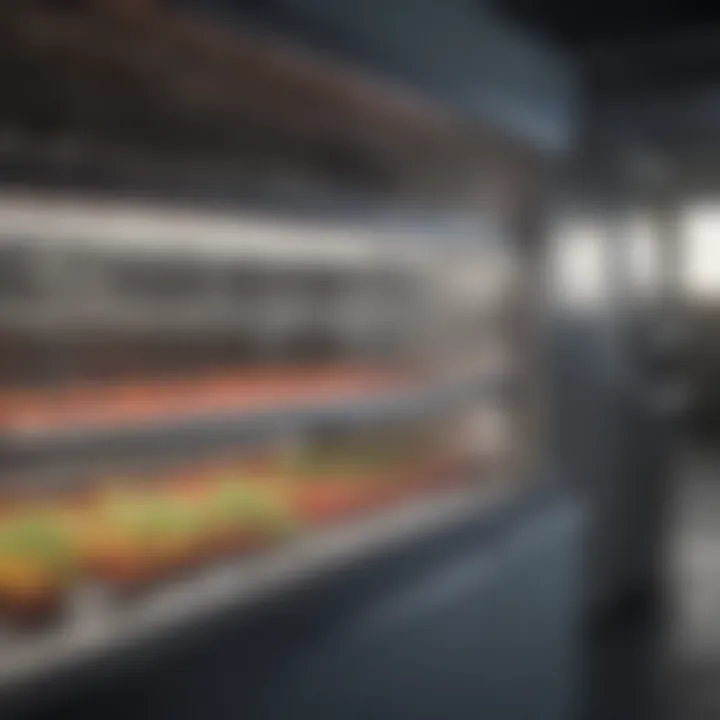
Intro
In the world of poultry farming, having the right tools is crucial for successful reproductive outcomes. The GQF incubator and hatcher are no exception; they are respected machines that any serious poultry enthusiast cannot overlook. As more farmers turn to artificial incubation to boost their production, understanding these devices becomes increasingly important. This article delves into the intricate details that set the GQF systems apart, emphasizing the design features, user functionalities, and modern innovations that contribute to their effectiveness.
Key Concepts and Terminology
Definition of Terms
To ensure clarity throughout this guide, it’s vital to define some specific terms. The incubator is a controlled environment where eggs are placed to allow for development prior to hatching. Meanwhile, the hatcher is where eggs are moved just before they are ready to hatch, adjusting conditions appropriately for the final stages of development.
Overview of Relevant Practices
Mastering incubation practices can also influence your results significantly. The three most relevant elements to keep in mind are temperature, humidity, and ventilation. Proper temperature generally hovers around 99.5°F (37.5°C) for most poultry species, while humidity levels typically range from 45-55% during incubation, increasing to 65-75% just prior to hatching. Ensuring adequate ventilation helps maintain a healthy atmosphere within the incubator.
Current Trends and Innovations
Latest Research and Developments
Recent studies have centered on enhancing incubation efficiency. Advanced models of GQF incubators now feature state-of-the-art technology that allows for precise climate control through automated systems. This research indicates that such improvements can raise the hatch rate, contributing to overall flock health.
Emerging Technologies and Tools
Among the cutting-edge innovations are smart monitoring systems, which utilize mobile apps for real-time monitoring. This means farmers can track temperature fluctuations and humidity levels right from their phones, allowing for prompt adjustments. Such technology is pivotal for those who operate multiple incubators, ensuring that no stone is left unturned in pursuit of successful hatches.
Practical Applications
Step-by-Step Guides
Using a GQF incubator and hatcher requires careful attention, and following a structured approach can yield the best results. Here’s a straightforward guide:
- Set Up: Place the incubator in a quiet, perfectly ventilated area, away from direct sunlight.
- Calibrate: Before adding eggs, ensure the temperature and humidity are at standard levels.
- Load Eggs: Gently place the eggs, wide end up, ensuring even spacing.
- Monitor: Regularly check the settings, adjusting as necessary and keeping a log of any fluctuations.
- Transfer: Move the eggs into the hatcher a few days before the expected hatch date, increasing humidity.
- Hatch Care: Observe the newly hatched chicks to ensure they are warm and have access to food and water.
Troubleshooting Common Issues
As any experienced farmer will tell you, hurdles do appear. Here are a few common problems and some potential solutions:
- Low Hatch Rate: If hatch rates are below the expected norms, check temperature and humidity readings for consistency. Consider recalibrating your device as needed.
- Unexpected Odors: Bad smells can indicate rotten eggs. Frequent candling of eggs is a good practice during incubation to identify any issues.
- Chick Health Problems: If chicks emerge weak or unhealthy, ensure that environmental conditions, especially humidity and temperature, were maintained appropriately during hatching.
"Investing time in understanding your equipment is just as crucial as the equipment itself."
Arming yourself with knowledge about the GQF incubator and hatcher allows poultry farmers to operate more effectively, leading to better productivity and healthier chicks. As new trends continue to evolve, staying informed will ultimately pay dividends in your poultry endeavors.
Preface to GQF Incubators and Hatchers
In the world of poultry farming, understanding the mechanisms behind incubators and hatchers is crucial. GQF incubators and hatchers have carved a niche for themselves, known for their efficiency and reliability. These devices are not just fancy contraptions; they serve as the backbone in successfully breeding poultry. But what exactly makes them so important? Let’s delve into the specifics.
One key aspect of GQF incubators is their unique design tailored for optimal egg development. They create an environment that mimics the natural conditions that eggs would experience under a hen. The precision in temperature control, humidity regulation, and airflow design collectively contribute to a hatching success rate that many traditional methods strive to achieve but often fall short of. The benefits of leveraging such technology are evident. It allows farmers to hatch a greater number of chicks in a shorter time frame while ensuring the health and viability of those chicks.
When choosing to incorporate a GQF incubator into your poultry operation, there’s a lot to consider. It’s not just about throwing some eggs in a box and waiting for them to hatch. Understanding the parameters of temperature and humidity, as well as the mechanical aspects of these machines, is paramount. Thus, education around these topics is imperative for both new and seasoned poultry farmers.
"Investing in a GQF incubator can transform your farming approach; it addresses the age-old struggle of hatching rates and provides a science-backed solution."
With that in mind, let's take a look back in time and see how GQF has become a leading name in the incubation field and the role it plays in modern poultry farming.
Historical Overview
GQF Manufacturing Company has been around for quite some time, with a history that traces back several decades. Founded by a group of poultry enthusiasts, the company aimed to develop superior incubation technology. The first GQF incubators appeared in the early 1950s, and they were rapidly adopted by farmers who realized the shift from traditional methods to more reliable, technology-driven solutions.
As the years went on, advancements were made in design and functionality. What started with simple mechanisms and controls evolved into sophisticated incubators featuring digital controls and state-of-the-art monitoring systems, enhancing hatching success rates significantly. Innovations continue to emerge, allowing farmers to closely monitor and adjust the environment for optimal outcomes. Through the passages of history, GQF incubators have consistently pushed boundaries, setting a standard for others to follow.
Importance in Poultry Farming
The role of GQF incubators and hatchers in poultry farming cannot be overstated. These machines are central to the process of transforming fertilized eggs into healthy chicks, and this process is vital for sustaining poultry production.
- Maximizing Productivity: By automating the incubation process, farmers can hatch more eggs simultaneously, which translates directly to increased production.
- Consistent Environment Control: Unlike natural incubation, GQF systems can maintain precise conditions that are crucial for the developing embryos.
- Disease Prevention: Controlled environments reduce the risk of diseases that may arise in unmanaged settings, which could jeopardize entire flocks.
- Time Efficiency: GQF incubators cut down the time and labor needed for hatching, allowing farmers to focus on other vital aspects of their business.
Key Features of GQF Incubators
Understanding the key features of GQF incubators is essential for anyone serious about poultry farming. These features not only define the quality and usability of the equipment but also influence the success of the hatching process. When selected carefully, incubators can ensure a controlled environment for eggs, leading to healthier chicks and increased yield for farmers.
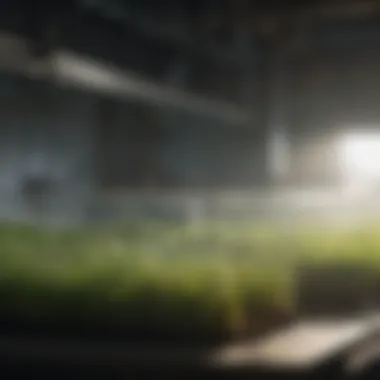
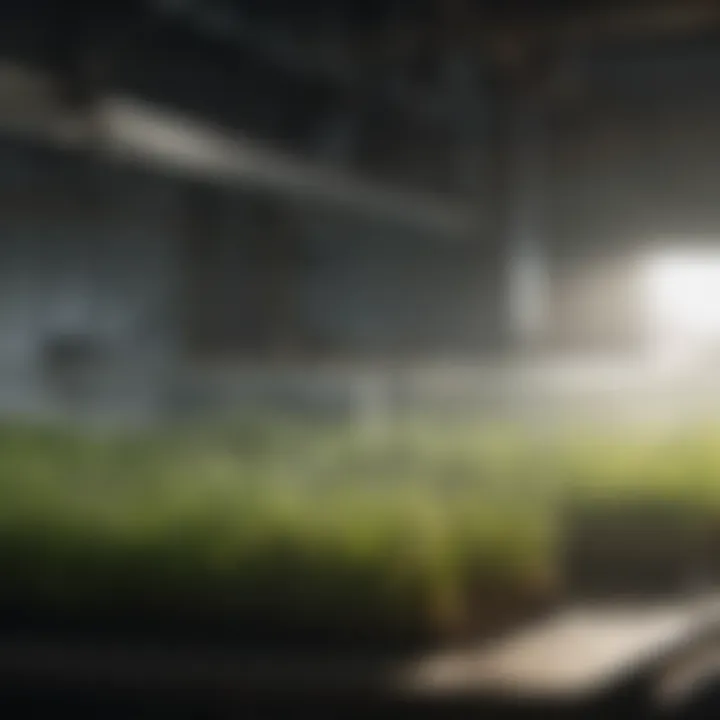
Temperature Control Systems
Temperature control is at the heart of successful incubation. When embedding eggs into an incubator, the right temperature plays a critical role. GQF incubators often come equipped with precise digital thermometers and thermostats that maintain the desired temperature consistently.
Why is this important? The development of the embryos in the eggs is highly sensitive to temperature fluctuations. Even a slight variation can spell the difference between a successful hatch and a failed one. These systems can adjust heating elements based on readings taken from the sensor, ensuring a stable range. Farmers can rely on the incubator’s ability to maintain these levels, allowing them to focus on other aspects of their operations.
Humidity Regulation Mechanisms
Next to temperature, humidity is another key factor in the incubation process. GQF incubators are designed with sophisticated humidity regulation mechanisms that either add or remove moisture within the chamber.
- Maintaining optimal humidity levels is crucial as it affects the weight of the eggs and the proper development of embryos. Generally, 50-65% humidity is recommended for most chicken eggs. Too little humidity can lead to dehydration of the chicks, whereas too much may prevent proper shell hardening before hatching.
Farmers can adjust humidity using built-in reservoirs that either fill automatically or manually. This feature is particularly beneficial during the critical later stages of incubation, where alterations may be necessary to assist the hatching process.
Airflow Design and its Significance
Ever heard the saying "you gotta let it breathe"? This rings true for eggs too. Adequate airflow is vital in an incubator as it helps distribute temperature and humidity evenly. The GQF models are engineered with well-thought-out airflow designs that ensure fresh air circulates while allowing for exhaust of stale air.
- Air circulation assists in temperature regulation by preventing hot and cold spots within the incubator. It also helps manage moisture levels, thereby supporting healthy development.
- Moreover, some models come with fans that can actively distribute air, preventing pockets of stagnant air that can lead to issues.
A well-ventilated incubator, like those made by GQF, enhances not just the likelihood of a successful hatch but also the quality of the chicks produced.
In summary, the features of GQF incubators—temperature control, humidity regulation, and efficient airflow—combine to create an ideal environment for egg incubation, directly impacting the success rate for poultry farmers.
All these elements play into the larger core of successful incubation. By understanding these key features, farmers can make informed decisions that enhance their hatching efficiency.
Understanding Hatching Process
Understanding the hatching process is central to grasping the functionality of GQF incubators and hatchers. This stage, where the miraculous transformation of eggs into chicks occurs, calls for a blend of careful monitoring and understanding of the biological needs of the embryos. When a farmer knows how this intricate process works, they can optimize their setup for maximum hatching efficiency. Recognizing key elements like the role of temperature and humidity, alongside the transition from incubator to hatcher, is instrumental in raising healthy chicks. This section details these vital components, making hatching a topic of great importance for anyone involved in poultry farming.
Role of the Hatcher
The hatcher's role is multifaceted, acting as the grand finale in the egg incubation journey. After spending a significant portion of their development in the incubator, eggs are moved to the hatcher for the final stretch. The hatcher provides conditions specifically tailored for the last few days before hatching. This phase is not merely an extension of incubation; it requires a distinct environment.
One of the hatcher's main jobs is to maintain the temperature and humidity levels that facilitate a smooth transition for the embryos. Too much or too little can lead to disastrous outcomes. For instance, while eggs in the incubator thrive under a stable temperature often around 99.5°F, hatchers generally need to dial this back slightly to improve hatch rates. Humidity levels must also be adjusted, usually rising to around 60-70% to ease the chick's emergence from the egg.
Additionally, the hatcher plays a crucial part in turning the eggs. Ideally, the eggs should be turned a few times daily to ensure the developing embryo doesn't stick to the shell. Automatic turning mechanisms in modern hatchers simplify this task, as humans can't always be around to handle them manually.
Transition from Incubator to Hatcher
The transition from incubator to hatcher isn’t as simple as moving products from one section to another. It involves specific protocols that need careful consideration. First things first, timing is everything. As eggs approach the end of their incubation period—approximately days 18-21 for chicken eggs—farmers must prepare for a seamless shift.
Here’s what farmers should keep in mind:
- Timing: Eggs should be transferred to the hatcher when the embryos are ready to hatch, this ensures they get the correct conditions without delay.
- Conditions: Before transfer, verify that the hatcher has achieved the desired temperature and humidity levels to prevent stressing the embryos during the move.
- Handling: Eggs should be handled gently to minimize the risk of cracking. Care taken in this stage goes a long way to reduce mortality rates among the unborn chicks.
As the hatching day approaches, unlocking the secrets behind the hatching process becomes crucial. In that moment, the right practices can make all the difference between success and failure in a hatchery. In summary, understanding the hatching process is not merely beneficial; it’s fundamentally important for anyone hoping to excel in the art of poultry farming.
Choosing the Right GQF Model
Selecting the right GQF model is a critical aspect for anyone involved in poultry farming. The correct incubator or hatcher can mean the difference between a successful hatch and a disappointing outcome. Each model offers distinct characteristics that can cater to specific needs. Whether you’re a hobbyist or managing a large-scale operation, understanding these differences is essential.
Several factors should guide your choice, ensuring both efficiency and effectiveness in incubation practices.
Factors to Consider
When choosing a GQF model, you need to consider several key elements that align with your specific needs:
- Capacity: How many eggs do you intend to incubate? GQF models range from small capacities suitable for personal or small-scale use to larger models designed for commercial farming. Knowing your scale will help narrow the options.
- Temperature and Humidity Control: Different models may excel in maintaining ideal temperature and humidity levels. Look for features like digital controls and readouts, as they offer greater precision and ease of use.
- Energy Efficiency: Operating costs are essential, especially over the long term. Check the energy ratings of the models; some consume significantly less electricity while maintaining performance.
- User-Friendly Design: An intuitive interface and ease of access for maintenance tasks can save you time and frustration. Certain models may incorporate features like clear windows for easy observation.
- Durability and Build Quality: Invest in a model that is built to last, particularly if you’re in a demanding environment. A sturdy design can endure heavy usage and fluctuating conditions.
- Budget: Determine a budget beforehand to filter out options that exceed your financial capacity without compromising on quality or features.
Comparison of Popular Models
To navigate the landscape of GQF models more effectively, here’s a brief comparison of popular options:
- GQF 1502 Sportsman
This model is a favorite among serious poultry enthusiasts. It offers ample capacity, excellent temperature control, and advanced humidity management. The adjustable racks allow accommodating different egg sizes seamlessly. - GQF 1202
A more compact model, the GQF 1202 is excellent for personal use or smaller quantities. Its simplicity and efficiency make it user-friendly for beginners. - GQF 2500
Designed for a commercial setting, this model can handle larger batches effortlessly. Its automation features make it appealing for larger operations where precision and efficiency are paramount. - GQF 1600 Series Hatcher
Specifically designed for the hatching process, this model emphasizes optimal airflow and high hatch rates. It pairs well with incubators from the same series, making transitions smoother.
- Capacity: Up to 150 eggs
- Ideal for: Serious hobbyists and small farms
- Capacity: Up to 72 eggs
- Ideal for: Hobbyists and beginners
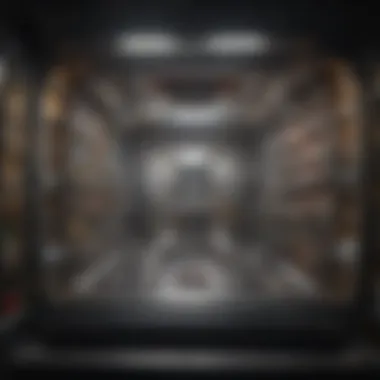
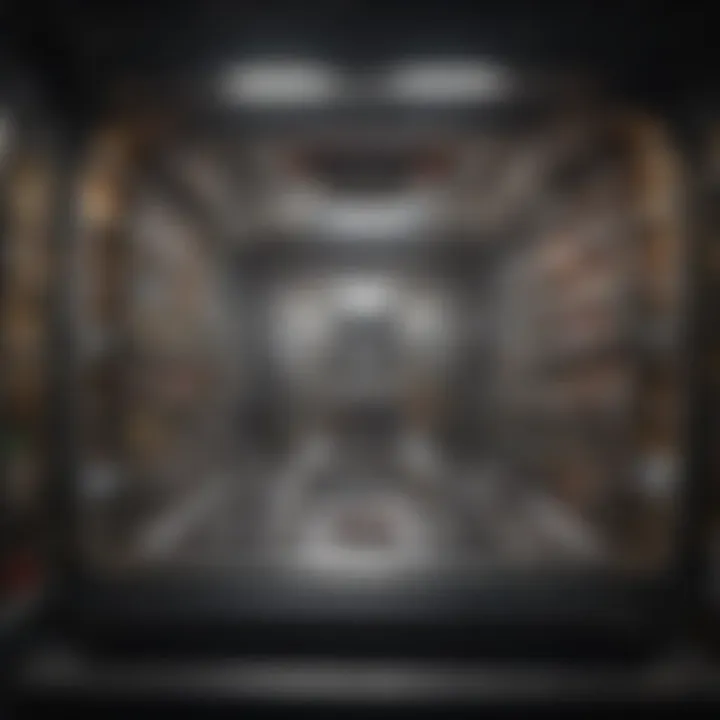
- Capacity: Up to 250 eggs
- Ideal for: Small to medium-sized poultry farms
- Capacity: Up to 120 eggs
- Ideal for: Farms focused on high hatch rates
Each model brings something unique to the table. It’s prudent to weigh these aspects against your own needs to find the one that fits like a glove. Ultimately, the right GQF incubator or hatcher can enhance your poultry farming experience, boosting efficiency and productivity.
Remember: Choosing the right model tailored to your specific needs can lead to successful hatching outcomes, ensuring the health of your chicks and the longevity of your agricultural endeavors.
Installation and Setup
Setting up the GQF incubator and hatcher is a critical step that influences the success of your poultry incubation process. The right installation ensures that you effectively create an environment conducive for hatching, thus maximizing the chances of healthy chicks emerging from their eggs. Ignoring this phase can lead to unwanted complications like inconsistent temperature or humidity levels, which can jeopardize the entire effort.
Site Selection and Preparation
Selecting the right location for your incubator is more than just picking a spot in the barn; several factors come into play. Ideally, the site must be stable, dry, and away from direct sunlight to maintain a consistent temperature. Too much sunlight can heat up the incubator more than desired, throwing everything off balance.
A well-insulated room is also beneficial, particularly in areas that experience extreme temperatures. This not only helps in maintaining the internal conditions of the incubator but also reduces your energy costs. Consider proximity to power sources since these devices usually require consistent electricity. Another thing you want to keep in mind is ease of access; it's critical to be able to monitor and adjust settings without hassle.
Moreover, a clean environment is essential. Dust and debris can affect the performance of your incubator, so a solid cleaning routine before installation is a must.
"Selecting the perfect spot is half the battle won; it’s where your chicks’ journey begins."
Initial Calibration Procedures
Once you have identified the site and set the incubator in place, the next hurdle is calibration. This involves setting the temperature, humidity, and egg turn frequency—each being pivotal in ensuring optimal hatching conditions. GQF incubators generally come with clear guidelines on recommended settings.
- Temperature Setting: Typically, the ideal temperature is around 99.5°F (37.5°C). Use a good thermometer to confirm that the incubator reaches this target. It's wise to let the incubator run for at least 24 hours before placing the eggs, to allow for any fluctuations to stabilize.
- Humidity Regulation: The initial humidity setting often hovers between 40-50% for the incubating phase, then rises to around 65% during the hatching phase. Use reliable hygrometers to keep track of the moisture levels, making adjustments as necessary.
- Egg Turning Mechanism: If your model includes an automatic turner, ensure it operates correctly. If manual turning is your method, establish a schedule—at least three times a day is generally advised.
Finally, don’t skip a dry run. For a couple of days before you start the actual incubation, run the machine with no eggs inside. This gives you a chance to troubleshoot any issues that arise.
In sum, the installation and setup of your GQF incubator and hatcher are foundational elements that can dictate the outcome of your hatching endeavors. Skipping these fundamental steps could lead to all sorts of grief down the line.
Optimal Operating Conditions
Maintaining optimal operating conditions is fundamental to ensuring a successful hatching process. The interplay of temperature, humidity, and egg turning has a significant impact on the health and development of embryos. Let’s delve deeper into two vital elements that contribute to the overall effectiveness of the GQF incubator and hatcher: monitoring temperature and humidity, and understanding egg turn frequency.
Monitoring Temperature and Humidity
Temperature and humidity are the two heavyweights in the arena of incubation. Keeping them balanced is crucial for the embryos’ proper development. In many cases, even a slight deviation can lead to disastrous results. For example, if the temperature is too low, it can prolong the incubation period, leading to unfortunate outcomes.
To effectively monitor these factors, GQF incubators come equipped with reliable thermometers and hygrometers. These devices provide real-time data, allowing for immediate adjustments when needed. It's like having your own weather station right in your poultry operation.
Consider the following points:
- Ideal Temperature: For chicken eggs, the incubation temperature should hover around 99.5°F (37.5°C). A consistent temperature is key, so avoid frequent fluctuations.
- Humidity Levels: Maintain humidity between 40% to 60% for the first 18 days, increasing to about 65% to 70% during the hatching phase to ensure a smooth transition for the chicks.
- Regular Calibration: Instruments can drift over time. Regular checks and calibrations are a must to keep the readings accurate.
"The right conditions are like a nurturing hand; they ensure the best for your hatchlings."
Understanding Egg Turn Frequency
Turning eggs during incubation is a practice seen as essential. One might wonder, why bother? The answer lies in how this action mimics natural conditions experienced in a hen’s nest. Eggs need to be turned multiple times a day, usually every 1-2 hours, to promote even heat distribution and proper development.
Here are some recommendations:
- Turn Schedule: Aim for at least 3-5 times a day. Many incubators, including GQF models, have automatic egg turners to ease the burden.
- Position Matters: Eggs should be turned from one side to another, making sure they don’t stay in the same position for too long. This prevents the embryo from sticking to the shell.
- Monitor Development: If you’re turning eggs manually, be sure to mark the eggs to gauge how frequently they are being turned.
The frequency of egg turning creates a dynamic environment that fosters healthy growth during the critical stages of incubation. Ensuring that both temperature and humidity are maintained at optimal levels, coupled with a regimented turning schedule, lays the groundwork for a successful hatch.
Common Issues and Troubleshooting
Recognizing and resolving problems with GQF incubators and hatchers is crucial for optimizing the incubation process in poultry farming. The significance of addressing common issues directly affects the success rate of hatching, ensuring a healthy start for chicks. Farmers often face challenges related to temperature and humidity, both vital elements that require constant monitoring. When these factors are not regulated properly, it can lead to disastrous results, such as decreased hatchability and the viability of chicks. Thus, understanding potential pitfalls can bolster confidence in managing these technologies.
Identifying Temperature Fluctuations
Temperature control is the linchpin of a successful incubation. Variations can occur due to multiple factors, from external weather conditions to mechanical malfunctions. Identifying these fluctuations promptly is crucial. A well-set incubator should maintain a consistent temperature, ideally around 99.5°F for chicken eggs. However, you might find yourself in situations where this number swings.
- Observe the Thermometer: Regular checks of the built-in thermometer can alert you to anomalies. Consider investing in external thermometers for greater accuracy.
- Listen for Changes in Noise: Some incubators emit sounds when they are heating or cooling. If you notice unexpected noises, it may be time to investigate.
- Check Power Sources: Unstable electrical supply can disrupt the incubator's functionality. Ensure that your power source is reliable.
It's essential to note that even minor fluctuations may trigger eggs to slow their metabolic rates or impact embryo development. As it goes, an ounce of prevention is worth a pound of cure.
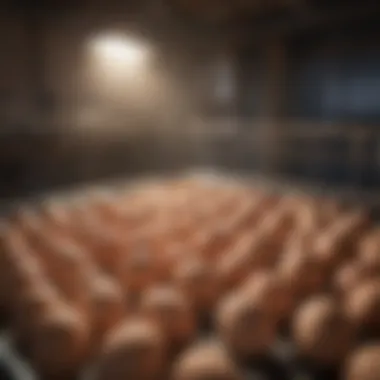
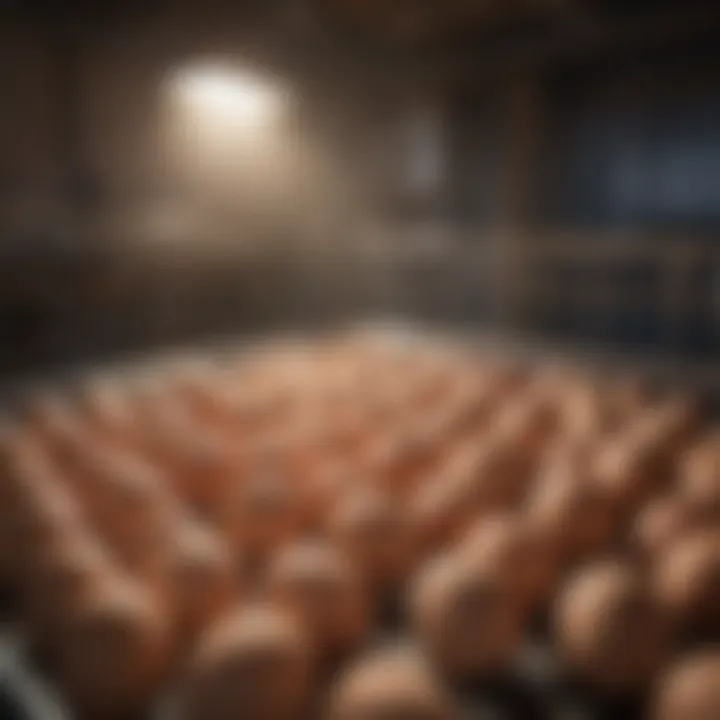
Dealing with Humidity Problems
Humidity is equally vital, playing a key role in the developing embryo's health. The right level can ensure optimum conditions for hatching, while too high or too low can result in significant problems. Aim for relative humidity levels between 40-50% during incubation, then increase it to 60-65% during hatching.
- Use Hygrometers to Monitor: Just like thermometers for temperature, hygrometers can give you reliable readings on humidity levels. A digital model can offer real-time data.
- Water Reservoirs: Many incubators come with built-in trays or reservoirs for water. Ensure they are filled adequately. If humidity is low, adding water can create a more favorable environment.
- Ventilation Adjustments: Proper airflow is required. Sometimes, closing or opening vents may help regulate humidity levels effectively.
Resolving humidity discrepancies involves a bit of trial and error. Don't hesitate to tweak settings to suit your specific environment. Management can become a balancing act, but with patience, you'll find the right mix.
"A successful hatch often hinges on satisfying a delicate balance of environmental conditions. Monitoring goes hand in hand with adjustment to ensure your hatchlings have the best chance at life."
In summary, the ability to troubleshoot temperature and humidity issues is vital for anyone utilizing a GQF incubator or hatcher. Recognizing the signs early can help avert potential failures, giving you a fighting chance in achieving that perfect hatch.
Maintenance and Care for Longevity
Maintaining and caring for GQF incubators and hatchers is critical for ensuring their longevity and optimal performance. These machines are investments in your poultry production business, and taking better care of them can prevent costly repairs and replacements in the future. Well-maintained equipment not only extends the service life but also improves the hatching efficiency, ultimately leading to healthier chicks. It's like polishing a car; a little effort goes a long way in keeping things running smoothly. Here, we explore specific elements that together create a robust maintenance routine.
Regular Cleaning Protocols
Regular cleaning of your GQF incubator and hatcher is vital. Not only does it help keep the machines looking their best, but it also minimizes the risk of bacterial growth and other contaminants that could adversely affect egg health. Cleaning should be done thoroughly and frequently.
Some best practices include:
- Daily Cleaning: Wipe down easily accessible areas with a damp cloth to remove any dust and debris. This will prevent buildup that could interfere with the mechanisms of the machine.
- Weekly Deep Clean: Once a week, empty the incubator and hatcher. Clean and disinfect using a solution such as a mild bleach mix or specialized cleaning products designed for incubators. Allow the inside to air dry completely before reloading with eggs.
- Seasonal Maintenance: At least twice a year, conduct a deeper inspection of all parts, including fans and heating elements. Dust and debris can accumulate here, affecting performance.
Pay attention to signs of wear or damage. If you notice a broken seal or any rust, it might be time for a repair or part replacement.
Regular cleaning and preventative care not only promote hygiene but also enhance incubation effectiveness.
Routine Inspection Practices
Routine inspections play a significant role in maintaining the GQF incubator and hatcher. It’s not just about keeping it clean; it’s about making sure everything is functioning as it should. Establishing a habit of checking key components will help identify potential problems before they escalate.
Keep these points in mind for effective inspections:
- Temperature Monitoring: Ensure that the temperature is consistently in the recommended range. Use calibrated thermometers to verify accuracy, as faulty readings can ruin hatch rates.
- Humidity Levels: Regularly check the humidity gauges. Insufficient humidity levels can lead to dehydration of eggs, while excessive humidity can lead to mold.
- Mechanical Functionality: Examine fans, heating elements, and thermal sensors regularly. Listen for any unusual noises which might indicate a malfunction.
- Egg Handling: Keep track of the egg inventory and check for any cracks or signs of infection. Disposing of affected eggs immediately can save others.
Impact of Technology on Incubation
In a fast-evolving agricultural landscape, the impact of technology on incubation practices cannot be overstated. As poultry farming demands increase, efficient and effective incubation becomes crucial for success. GQF incubators and hatchers are at the forefront of these technological advancements, incorporating features designed to enhance hatching rates and chick vitality.
One significant element is the implementation of smart controls. These systems take the guesswork out of managing incubation conditions. By auto-adjusting temperature and humidity based on real-time data, they ensure eggs are kept in ideal settings, which leads to a higher yield of healthy chicks. Farmers can monitor and fine-tune these parameters remotely, providing a level of convenience and precision that was previously unavailable.
“The future of poultry farming isn’t just about tradition; it’s about merging old practices with new technology.”
Smart Controls and Automation
Smart controls in GQF incubators mark a significant leap forward. These systems utilize sensors and data analytics to maintain optimal conditions continuously. For instance, temperature swings can wreak havoc on embryo growth, and with automated systems, any deviations can be immediately corrected. This not only saves time but also reduces the human error often seen in manual operations.
Additionally, the ability to schedule automated turning of eggs significantly enhances the incubation process. Instead of having to remember to turn eggs manually—a task that can be easily forgotten—smart systems can automate that vital aspect, ensuring each egg is treated uniformly. This leads to more consistent results and higher hatch rates.
Integrating IoT in Incubators
The integration of the Internet of Things (IoT) into incubators represents a pivotal shift in how incubation is managed. IoT devices enable real-time monitoring through internet-connected sensors that alert farmers to changes in environment instantly. If humidity levels begin to dip or temperatures rise unexpectedly, alerts can be sent directly to a smartphone or computer, allowing for quick corrective measures.
Further, farmers can gather historical data over time, analyzing trends in incubation success linked to specific conditions. This data-driven approach fosters continuous improvement, which is invaluable in breeding programs striving for the best results.
Summary and Finale
In wrapping up our exploration of the GQF incubator and hatcher, it’s essential to underscore the pivotal role these devices play in the poultry farming landscape. The heart of effective incubation rests not just on understanding how to set up these machines, but also on recognizing the nuances that can make or break the hatching process. It’s about building a solid foundation of knowledge that empowers farmers and poultry enthusiasts alike, enhancing both productivity and animal welfare.
The significance lies in several key elements. First, the temperature control systems ensure that the eggs are incubated in optimal conditions, crucial for the development of healthy chicks. Meanwhile, humidity regulation mechanisms assist in maintaining the right moisture levels, which can directly impact the success rate of hatching. Furthermore, understanding the airflow design not only promotes consistent temperature and humidity distribution but also significantly contributes to the overall health of the chicks.
By delving into common issues like temperature fluctuations and humidity problems, we equip users with troubleshooting skills that can save entire batches from being compromised. The emphasis on maintenance practices such as regular cleaning and inspections cannot be overlooked, as these actions greatly influence the longevity of incubators and hatchers.
Looking at the future, it's worth considering advancements in technology that are shaping incubation processes. The integration of smart controls and IoT devices is a game-changer, fostering a more data-driven approach to managing the incubator environment. This focus on innovation will help farmers adapt to new challenges and demands in poultry farming.
"The essence of successful incubation is a combination of science, care, and consistent practices that evolve with technology."
Recap of Essential Points
- Temperature Control: Key to ensuring proper development of chicks.
- Humidity Regulation: Ensures appropriate moisture levels for successful hatching.
- Airflow Design: Enhances the overall health of the incubation environment.
- Troubleshooting Skills: Vital for addressing common issues encountered.
- Maintenance Practices: Critical for the longevity of equipment.
- Future Technologies: Smart controls and IoT can revolutionize poultry farming practices.
Future Considerations
As we gaze into the future of incubation technology, embracing innovation will become increasingly vital. Keeping an eye on trends like automated incubation processes, augmented AI in environmental monitoring, and advanced genetic selection for poultry breeds can significantly enhance productivity. Adoption of sustainable practices and eco-friendly incubating methods will emerge as necessary standards, pushing the industry towards a more responsible future.
Farmers and enthusiasts alike should remain adaptable, engage with ongoing research, and continually educate themselves on emerging technologies to stay ahead of the curve. Investing not just in equipment, but in knowledge and skills will undoubtedly pave the way for advancements in poultry farming.